Current monitoring of large structures such as bridges, wind turbines and mines generally relies on time consuming visual inspections that use specialized instrumentation and equipment. Translation: it's expensive. But if damage can be detected before any structural damage occurs, maintenance bills can also be significantly reduced and safety increased. Researchers at the University of Strathclyde in Glasgow are tackling the issue with a smart paint they claim not only detects microscopic faults before structural damage occurs, but does so at a cost of just one percent of current widely used inspection methods.
Like other structural monitoring technologies we've looked at, such as wireless sensors, self-repairing sensors, and nanocomposite materials, the smart paint allows continuous monitoring of structures without the need for costly inspections.
The main material used to make the paint is fly ash - which is generated in combustion and is a recycled waste product produced in the combustion of coal. This is mixed with highly aligned carbon nanotubes, to form a paint that can be sprayed onto any surface. After it is applied, the paint is embedded with electrodes that can detect structural damage long before it is obvious or failure occurs. These electrodes are paired with wireless communications nodes that also have power harvesting and communications capabilities to allow them to keep running and remotely send out a warning when damage is detected.
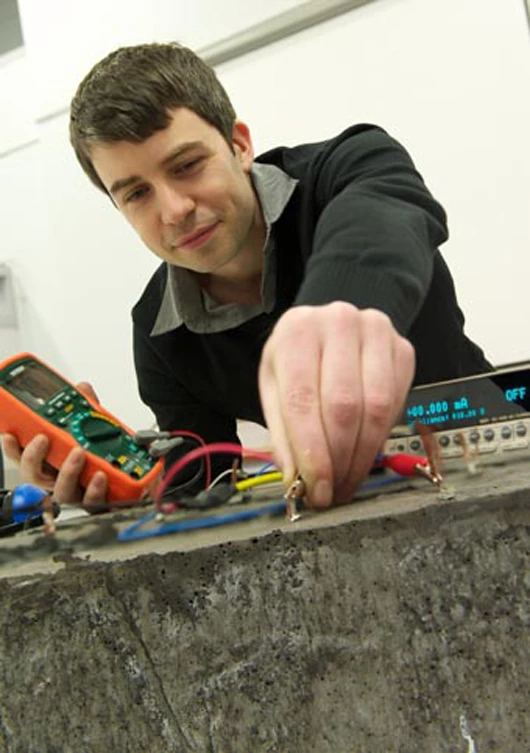
In addition to being able to continually monitor the entire surface of a structure, the researchers say the paint has a cement-like property that also makes it ideal for harsh environments.
"Current technology is restricted to looking at specific areas of a structure at any given time, however, smart paint covers the whole structure which is particularly useful to maximize the opportunity of preventing significant damage," said Dr Mohamed Saafi, of the University of Strathclyde's Department of Civil Engineering. "The properties of the fly ash give the paint a durability that will allow it to be used in any environment which will be a massive advantage in areas where the weather can make safety monitoring particularly difficult."
But it is the low cost of the smart paint - which the researchers estimate at just one percent of current widely used alternative inspection methods - that is potentially the smart paint's biggest selling point for cash-strapped government departments.
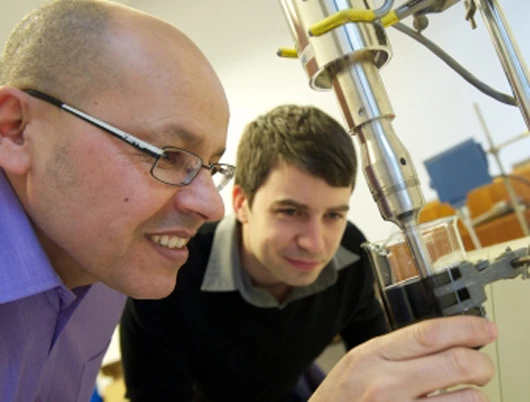
"There are no limitations as to where it could be used and the low-cost nature gives it a significant advantage over the current options available in the industry," says Dr Saafi. "The process of producing and applying the paint also gives it an advantage as no expertise is required and monitoring itself is straightforward."
The research has been carried out at the University of Strathclyde with Dr Saafi working alongside David McGahon, who initiated the work as part of his PhD project. They have already carried out tests on a prototype with positive results and now hope to demonstrate its effectiveness on a large structure.