Self-healing “smart building materials” have the potential to reduce structure repair costs, lower cement-production carbon emissions and even save lives. One barrier that has kept these materials from being commercialized, however, is their potentially labor-intensive and thus expensive production process. Recently, an engineering student from the University of Rhode Island (URI) announced that she has developed a self-healing concrete that would be inexpensive to produce.
Michelle Pelletier, collaborating with URI Chemical Engineering Professor Arijit Bose, created a concrete matrix that was embedded with a micro-encapsulated sodium silicate healing agent. When cracks formed in the concrete, the capsules ruptured and released the agent into the adjacent area. The sodium silicate reacted with the calcium hydroxide already present in the concrete, and formed a calcium-silica-hydrate gel that healed the cracks and blocked the concrete’s pores. The gel hardened in about one week.
When Pelletier’s concrete was stress-tested to the point of almost breaking, it proceeded to recover 26% of its original strength. By contrast, conventional concrete only recovers 10%. Pelletier believes that she could boost the strength of her mix even higher, by increasing the quantity of the healing agent.
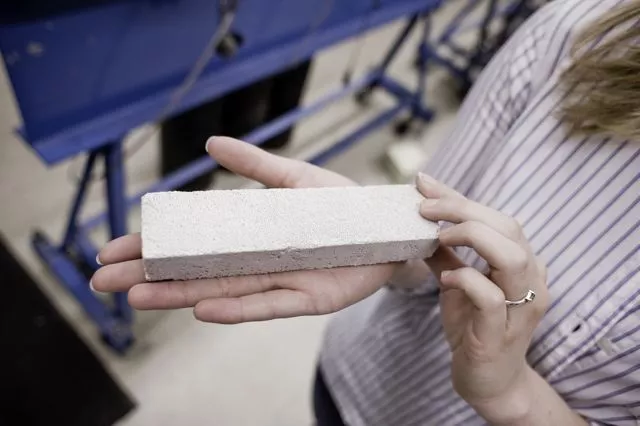
Other researchers have tried using bacteria spores that secrete calcium carbonate, or glass capillaries filled with a healing agent. According to Pelletier, her mix would be more cost-effective because it would be simpler to produce, and function more efficiently. “Smart materials usually have an environmental trigger that causes the healing to occur,” she said. “What’s special about our material is that it can have a localized and targeted release of the healing agent only in the areas that really need it.”
Pelletier is now researching how well the healing agent would work for minimizing the corrosion of steel rebar within concrete structures.