Super-black nanotechnology might sound like something ripped from the pages of a comic book, but instead of being in the hands of a super-villain, it's a NASA-researched technology that is set to make spacecraft instruments more sensitive without increasing their size. John Hagopian, an optics engineer at NASA's Goddard Space Flight Center, and his team have demonstrated the ability to grow a uniform layer of carbon nanotubes on oddly shaped platforms, which will extend the potential of the technology by allowing nanotubes to be grown on 3D components.
We first learned of NASA's super-black coatings a couple of years ago, but at that time they could only be grown on flat surfaces. This limitation has now been overcome through the use of a technique known as atomic layer deposition (ALD), which dramatically increases the potential applications of the technology, such as suppressing stray light that can overwhelm faint signals that sensitive detectors are designed to detect.
Since Hagopian is an optics engineer, he tweaked the super-black material for use in optical instruments, though the material could have other uses in the future. The team tuned the material to absorb an average of more than 99 percent of the ultraviolet, visible, infrared, and far-infrared light that strikes it. So, super-black is a fitting name as virtually no light is reflected off of the material.
The nanotubes are grown like a forest on materials used on spacecraft. Minuscule gaps between the nanotubes trap light while the carbon absorbs the photons, hence the lack of reflection and the super-black moniker. The super-black material consists of a thin coating of multi-walled carbon nanotubes that are about 10,000 times thinner than a strand of human hair.
With the ALD technology, the technicians deposit a foundational catalyst layer of iron oxide that acts as a base for the nanotube growth via a reactor chamber. ALD reactions typically use two chemicals that react with a surface one at a time in a sequential, self-timing manner. Within the reactor chamber, the researchers pulse different gases to deposit an atom-thin film on the component. They then move the component to another oven and heat it to about 750° C (1,382° F), while dousing it in carbon-containing feedstock gas.
The team married this ALD technique with growing nanotubes to aid in laying down a uniform catalyst. Hagopian explains that traditional techniques could only "apply coverage in the same way you would spray something with paint from a fixed angle." These methods would lead to an uneven catalyst surface for nanotube growth when working with three-dimensional components, whereas ALD allows control of the thickness and composition of a deposited film, even on 3D shapes.
NASA Goddard co-investigator Vivek Dwivedi, through a partnership with the University of Maryland at College Park, is advancing ALD reactor technology customized for spaceflight applications. Hagopian utilized the services of the Melbourne Centre for Nanofabrication (MCN), through the Science Exchange, an online marketplace where scientific service providers and experimenters can collaborate, to determine the viability of ALD for his work.
The MCN team, headed by Lachlan Hyde, an expert in atomic layer deposition, calibrated a precise recipe of chemicals for the thin-film catalyst layer. This recipe consisted of the gases needed (known as precursors) and the temperature and pressure needed within the reactor.
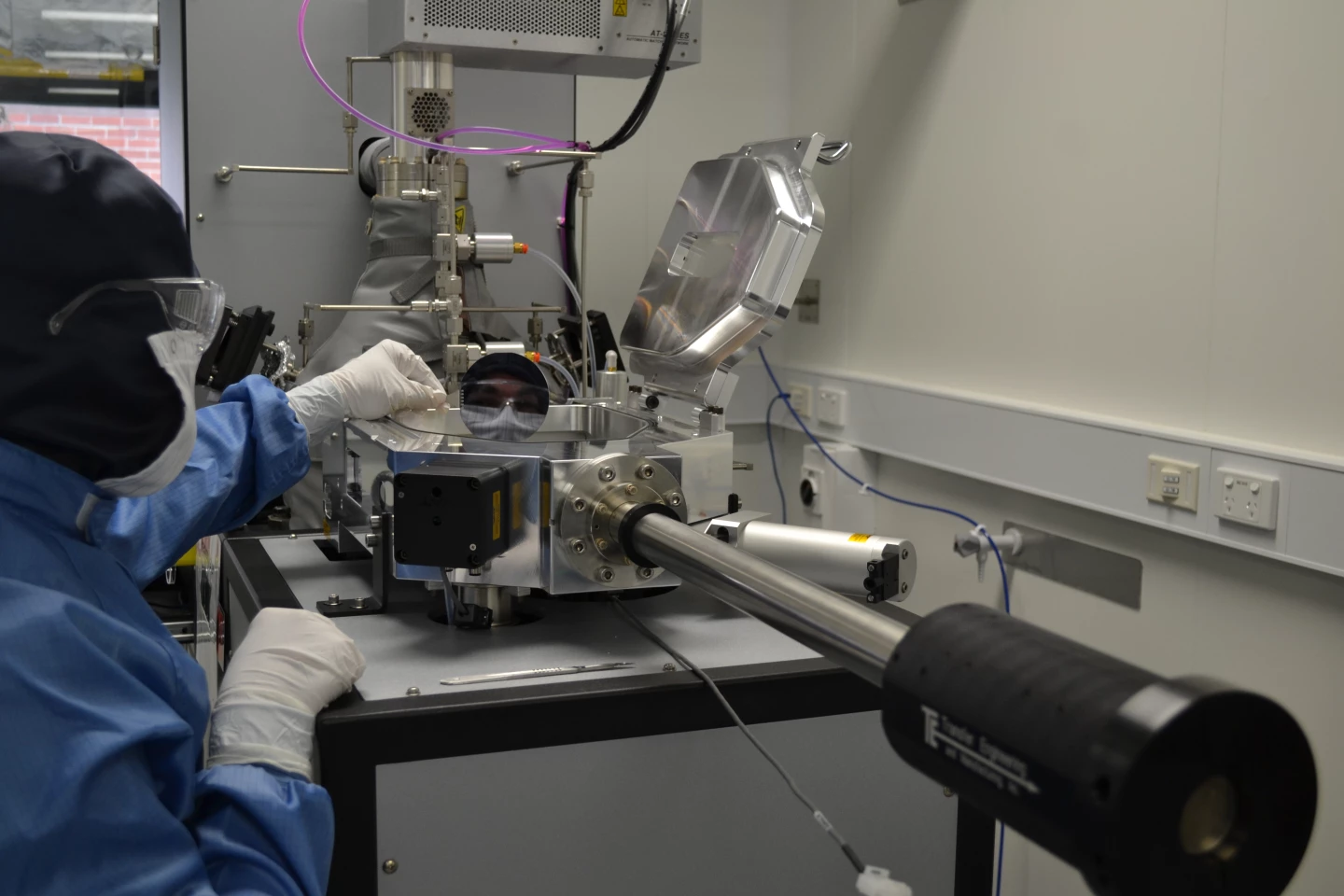
Hyde's team was successful in depositing the catalyst film on several components from NASA, including an elaborately shaped occulter, which the space organization uses for observing distant planets around other stars. The hope is to employ Hyde's techniques on components using Dwivedi's customized reactor technology.
Hagopian's team has already managed to grow carbon nanotubes on sample components, and they are looking to take more optical technologies into the super-black as soon as possible.
The video below is a 2010 file video that describes work on carbon nanotube technology at NASA's Goddard Space Flight Center.
Source: NASA