Inspired by the surface tension of a droplet of liquid, researchers have created an adjustable wheel that alters shape in real-time, tackling uneven surfaces and high obstacles with ease. It’s opened the door to developing wheelchairs or mobile robots that can better traverse rough terrains.
Essential components of cars, trucks, and bikes, wheels are so ubiquitous we often take them for granted. But when it comes to wheelchairs, the wheel’s poor performance traversing uneven surfaces or surfaces containing obstacles means that wheelchair-bound folk are mostly confined to staying ‘on-road’. The same goes for mobile robots.
Now, a group of Korean researchers has, quite literally, reinvented the wheel, developing an adjustable wheel that changes shape in real-time to overcome obstacles on the ground to allow travel off the beaten path.
Okay, ‘reinventing the wheel’ is probably hyperbole. A couple of years ago, tire giant Hankook collaborated with Seoul National University and Harvard to come up with transforming wheels inspired by origami. Many years before that, graduate student Ackeem Ngwenya developed his ‘Roadless’ wheel system, whose tread adjusted from narrow to wide with the turn of a screw. And, between times, NASA created tires for its rovers made from a nickel-titanium alloy that could deform right down to the axle and then return to their original shape.
The problem posed by uneven or obstacle-laden ground can be overcome using a track-based locomotion system, a specially designed mechanism that increases the wheel’s surface area. However, a track system is limited to relatively low speeds and consumes more energy than a wheeled system because of the high friction caused by increased contact between the system and the ground.
Using airless – or non-pneumatic – tires to traverse harsh terrains provides an advantage, namely because they’re resistant to punctures, leaks and blowouts. But their stiffness means they’re not great at overcoming obstacles, particularly high ones, because they’re less deformable or less able to adapt to the ground they’re traveling over.
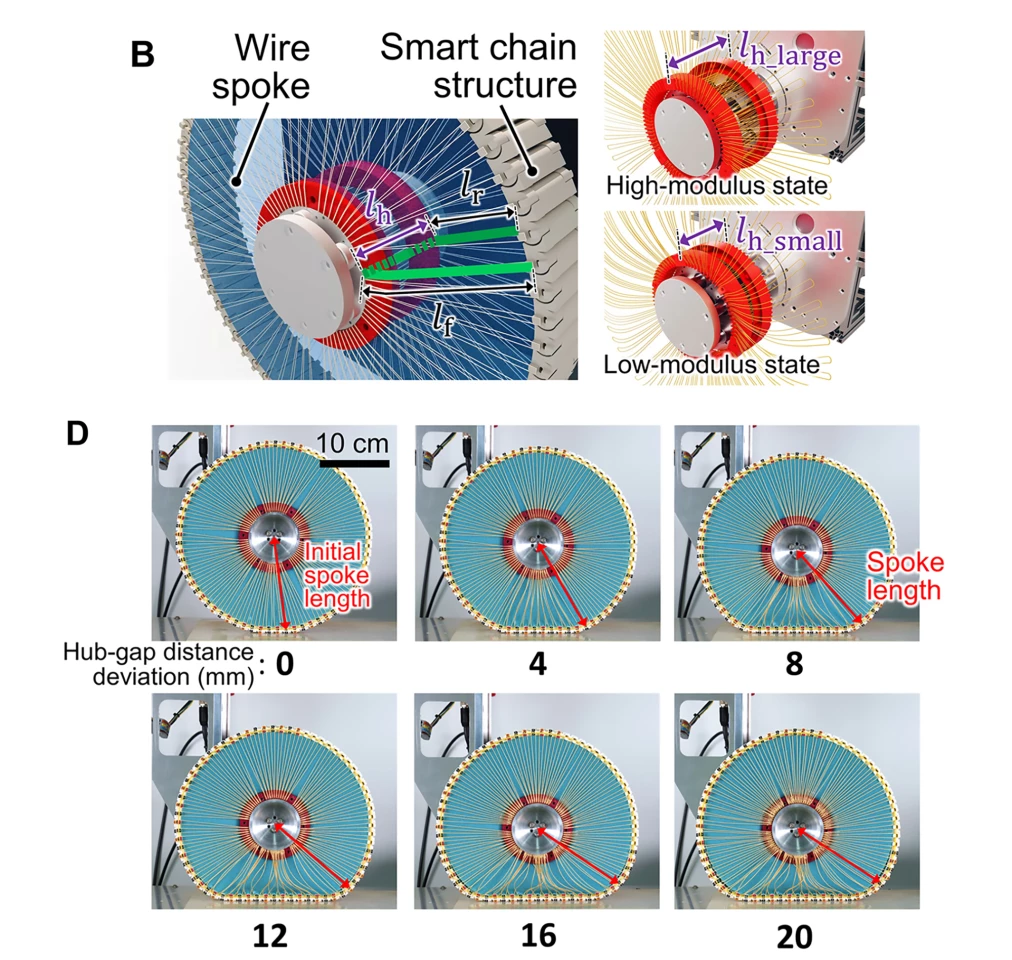
So, inspired by the surface tension of a liquid droplet, the scientists created a variable-stiffness wheel that can overcome rough terrain and obstacles while maintaining the advantages of a regular wheel driving on flat ground. The surface tension of a liquid results from an imbalance in the attractive or cohesive forces between molecules. Whereas a molecule in the bulk liquid experiences cohesive forces with other molecules in all directions, one at the surface of a liquid only experiences net inward cohesive forces. In a droplet, as the cohesive force of the surface molecules increases, the net force pulling the liquid molecules inward also increases, resulting in the droplet reverting to a circular shape.
A key aspect of the deformable wheel is its ‘smart chain structure,’ comprising a chain of blocks around the outside of the wheel connected by wire spokes to opposite sides of a central hub. By changing the gap between the two sides of the hub, the researchers could vary the length of the spokes and, therefore, the shape of the outer chain of blocks. Increasing the hub-gap shortened the spokes, forcing the chain block inwards and creating a circular wheel for quick locomotion. Reducing it lengthened the wire spokes and loosened the chain block, allowing it to deform and traverse over obstacles it encountered.
The researchers tested their adaptable wheel in a two-wheeled wheelchair and a four-wheeled vehicle and found that each could adapt to and drive over large steps and irregularly shaped rocks 1.2 times higher than the wheel radius.
The video above demonstrates how the two-wheeled wheelchair system, which weighed 120 kg (265 lb), easily covers uneven, grassy ground – although, the extreme forward tilt of the chair does make one concerned for the safety of its eventual occupant. The researchers haven’t made available a video of the four-wheeled vehicle in action, but images are below.
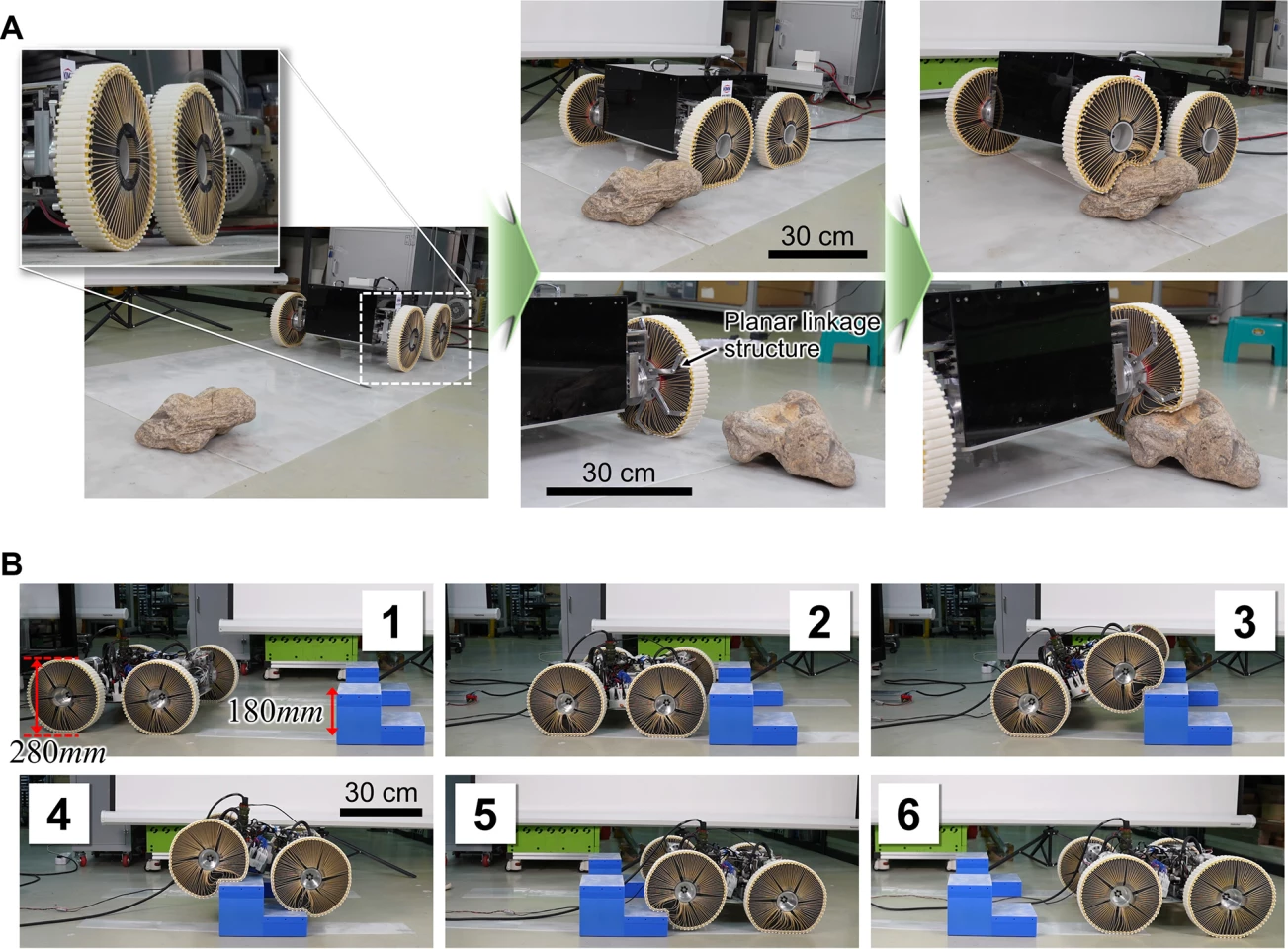
The researchers did note that dust and particles entered the areas between the smart chain blocks and caused damage to the wheel, so they’re working on adding a wheel cover structure to future iterations. They see great potential in their adaptable wheel.
“This study demonstrates real-time stiffness variation at the scale of actual wheels used for a wheelchair, suggesting broader common applications in wheel-based robots and transportation systems for efficient driving on rough terrain,” the researchers said.
The study was published in the journal Science Robotics.
Source: EurekAlert!