Injection molding is the widely preferred method for shaping plastic medical components, but now a new type of machine promises to slash energy and materials costs. Ultrasion's Sonorous 1G uses ultrasound to produce highly targeted and efficient heating to melt its plastic base material.
The Sonorous 1G was on show this week at the Medtec UK, a trade exhibition for medical technologies and devices. Despite its uses in the medical sector, it has uses in a host of different industries.
Research into technology used by the Sonorous 1G began about six years ago, with European Commission funding and help from the Barcelona-based ASCAMM technology centre. ASCAMM spun off Ultrasion as a company to take the technology commercial.
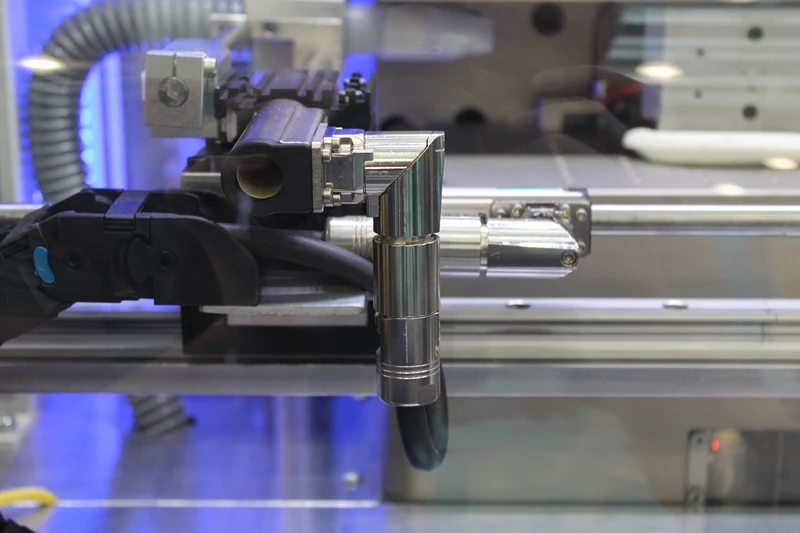
Ultrasound itself does not impart any heat. The process for melting the plastic for molding is caused by ultrasonic waves causing the plastic to vibrate and liquify. Any heat that is produced is, in fact, only a by-product. As such, the process is far more targeted and efficient than other methods that heat a whole area in order to melt plastic. Ultrasion estimates that energy costs can be reduced by around 90 percent using ultrasound.
The more highly targeted approach that is enabled by ultrasound also means that less base material can be used. The injection molding process results in a surplus of melted material that must be purged from the machine and wasted. Ultrasonic molding uses only the precise amount of material needed per molding cycle. As such, it requires between 60 and 80 percent less base material, according to Ultrasion.
An ultrasonic horn (the sonotrode) contacts the plastic base material, which causes it to melt and flow into the shape of the mold. The molded parts are then removed and the cycle is repeated. Ultrasion says that the process takes no longer than existing injection molding approaches.
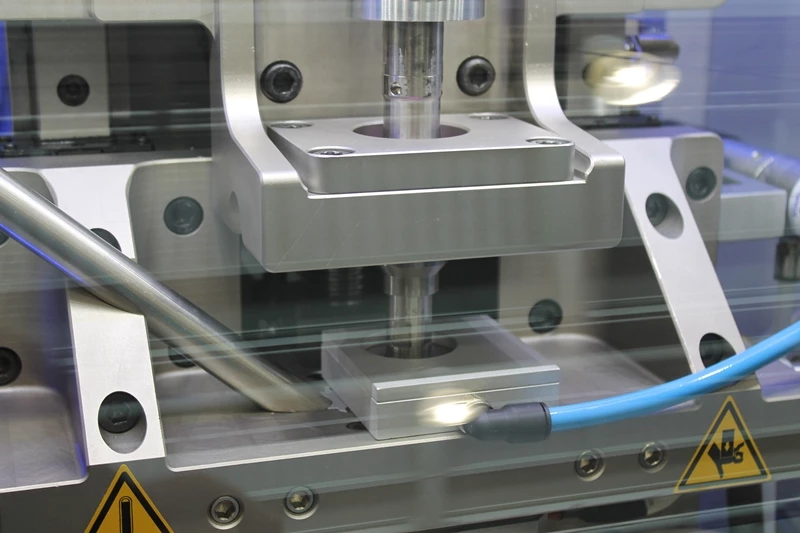
In addition to reduced energy costs and wastage, research into this technique found that using ultrasound melted plastic to a much lower viscosity. Working with "thinner" liquid means that longer, flatter, thinner and more detailed parts – previously impossible parts – can now be created. Lower viscosity also means that lower pressures can be used to facilitate the molding process, helping to avoid damage to components when overmolding and damage to the core pins used in some parts.
"All other micro molding technologies are large scale machines that have been reduced in size," explains Ultrasion Manager Enric Sirera to Gizmag. "This can only work to a point. By making machines this way, they remain much bigger than they need to be and use much higher injection pressures, molding pressures and clamping pressures than are actually necessary. This is what makes them energy inefficient."
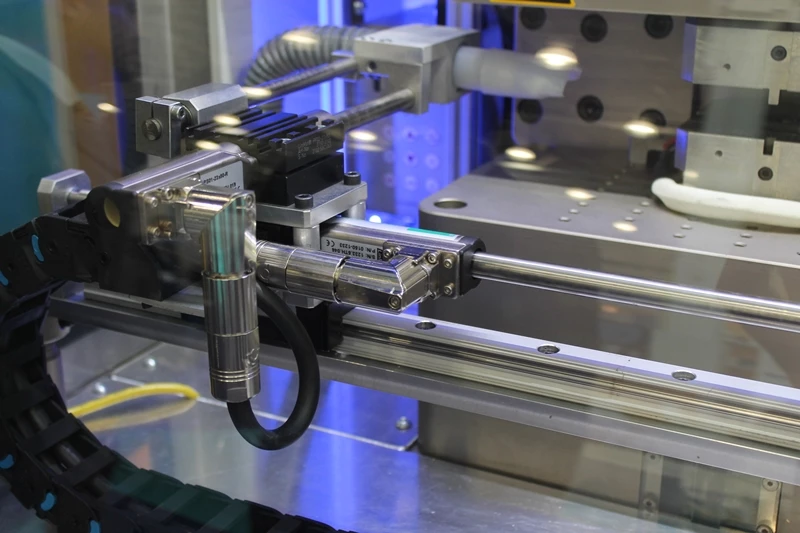
Sirera says that other existing molding methods tend to rely on old technology (such as screws, barrels, heater bands), making wasteful use of material. Likewise, the heating and melting methods used, he says, can cause degradation of the melted plastic and affect the integrity of the end product.
"Using this new approach, you have a machine that is of a size appropriate for micro molding and that uses much less energy and material," Sirera says. "So the economies of scale that you should expect making smaller products are finally attainable."
The Ultrasion Sonorous 1G is in the process of being rolled-out globally.
Source: Ultrasion