In the early 20th century Henry Ford revolutionized automobile production with the introduction of the assembly line for the iconic Ford Model T. Now, almost a century later, a car has been produced using a process that could prove just as revolutionary – 3D printing. Code-named, Urbee, the streamlined vehicle is the first ever to have its entire body, including its glass panel prototypes, 3D printed with an additive manufacturing process.
Designed from the ground up with environmentally sustainable principles in mind, Urbee offers some pretty impressive fuel efficiency numbers. The electric/liquid fuel vehicle uses both electric and gas motors in a series/parallel hybrid setup that allows it to achieve more than 200 mpg (1.2L/100km)on the highway and 100 mpg (2.3L/100km) in city driving with either gasoline or ethanol. For combined city and highway use, the Urbee gets about 150 mpg (1.6L/100km) and costs just two cents per mile. It can be charged overnight from a standard home electrical outlet.
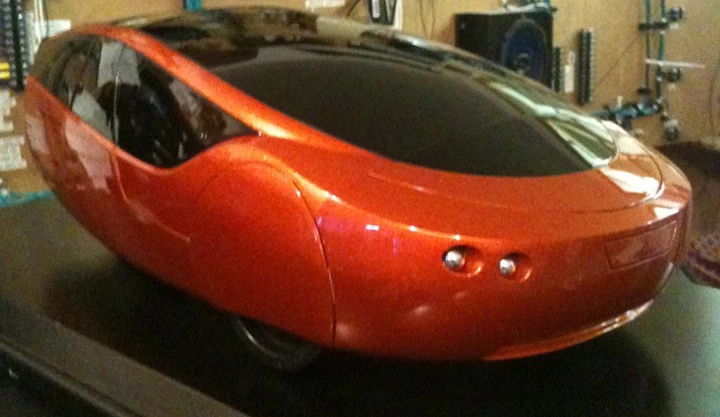
Urbee is the result of a collaboration between Winnipeg engineering group, Kor Ecologic, which designed the vehicle, and Minneapolis maker of additive manufacturing machines, Stratasys, which is responsible for printing all the vehicle’s exterior components. Stratasys used fused deposition modeling (FDM), which creates plastic parts by applying real thermoplastics in layers from the bottom up and allows the elimination of tooling, machining and handiwork and allows improved efficiency when a design change is needed.
The Urbee competed in the 2010 Automotive X-Prize Competition and a full-scale Urbee prototype as well as a 1/6 scale finished model will be displayed for the first time in the U.S. at the SEMA automotive show in Las Vegas from November 2 to 5.