Dual-clutch gearboxes are not all that new in the car world where they feature on light hatchbacks through to the venerable Bugatti Veyron. But when it comes to trucks, dual clutch gearboxes are yet to make an impact. Volvo is hoping to change that with its I-Shift Dual Clutch gearbox, which it claims is the first of its kind for heavy vehicles.
Dual-clutch set ups allow lightning quick shifts by always having another gear at the ready. Volvo's transmission features two input shafts and a dual-clutch, essentially meaning that two gears can be selected at the same time. The clutch dictates which of the two selected gears is engaged.
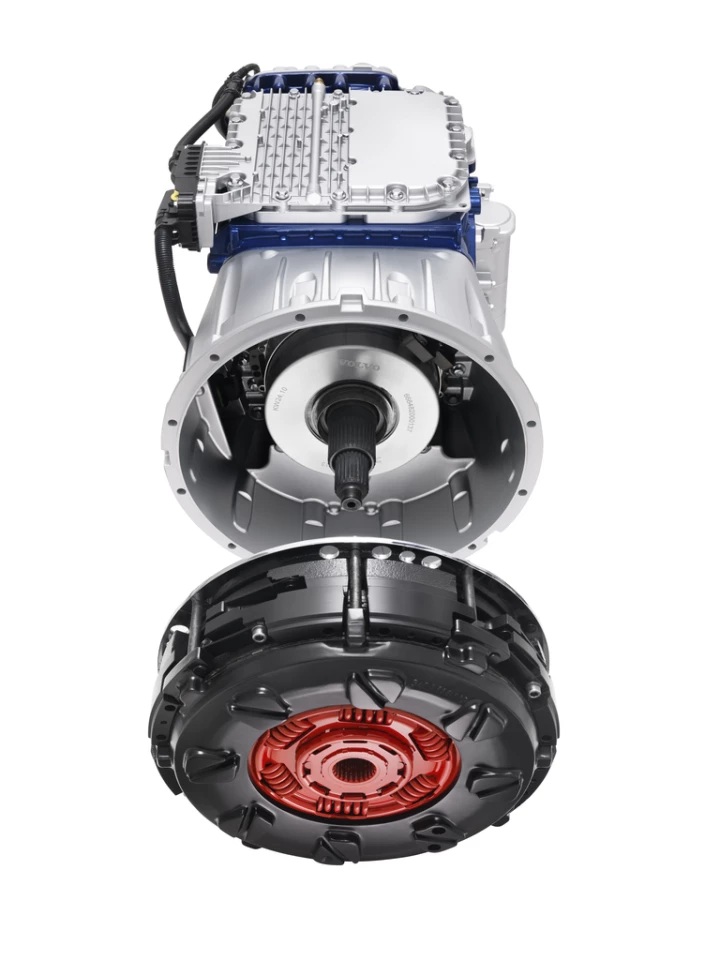
"When driving it feels like you have access to two gearboxes. When one gear is selected in one gearbox, the next gear is already prepared in the other," says Astrid Drewsen, product manager for drivelines at Volvo Trucks. "With dual clutches, gear changes take place without any interruption in power delivery. As a result, engine torque is maintained and driving comfort is significantly improved."
Volvo argues that these benefits are even more relevant to trucks because of their size, and because they regularly cover terrain where a lot of gear changes are required. This means that those hauling sensitive cargo are set to benefit most from the dual-clutch set up, along with drivers who travel in wet or uneven conditions, like logging truckers who travel through forests to collect their cargo.
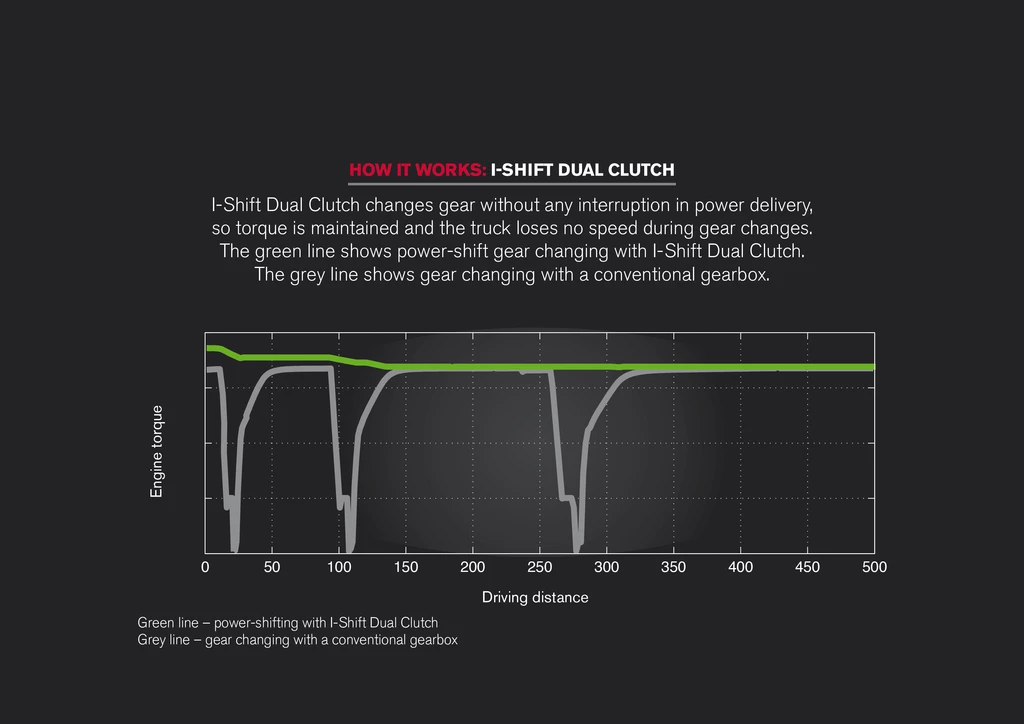
Volvo says that the smoother shifts the dual-clutch provides should also lessen wear on other driveline components, meaning lower maintenance costs, while fuel consumption remains the same as the standard I-Shift transmission.
When it is best to skip gears, the I-Shift Dual Clutch system can act in the same way as Volvo's standard I-Shift setup.
The I-Shift dual-clutch will be available on Volvo's FH, and can be coupled with D13 engines that make 460, 500 or 540 hp (343, 372 and 403 kW, respectively).
Volvo's video below details how the I-Shift Dual Clutch system works.
Source: Volvo Trucks