One little button in a piece of CAD software is threatening to fundamentally change the way we design, as well as what the built world looks like in the near future. Inspired by evolution, generative design produces extremely strong, efficient and lightweight shapes. And boy do they look weird.
Straight lines, geometric curves, solid surfaces. The constructed world as we know it is made out of them. Why? Nature rarely uses straight lines. Evolution itself is one of the toughest product tests imaginable, and you don't have a straight bone in your body, no matter how much you might like one.
Simple shapes are popular in human designs because they're easy. Easy to design, especially with CAD, and easy to manufacture in a world where manufacturing means taking a big block or sheet of something, and machining a shape out of it, or pouring metals into a mold.
But manufacturing is starting to undergo a revolutionary change as 3D printing moves toward commercially competitive speeds and costs. And where traditional manufacturing incentivizes the simplest shapes, additive manufacturing is at its fastest and cheapest when you use the least possible material for the job.
That's a really difficult way for a human to design – but fairly easy, as it turns out, for a computer. And super easy for a giant network of computers. And now, exceptionally easy for a human designer with access to Autodesk Fusion 360 software, which has it built right in.
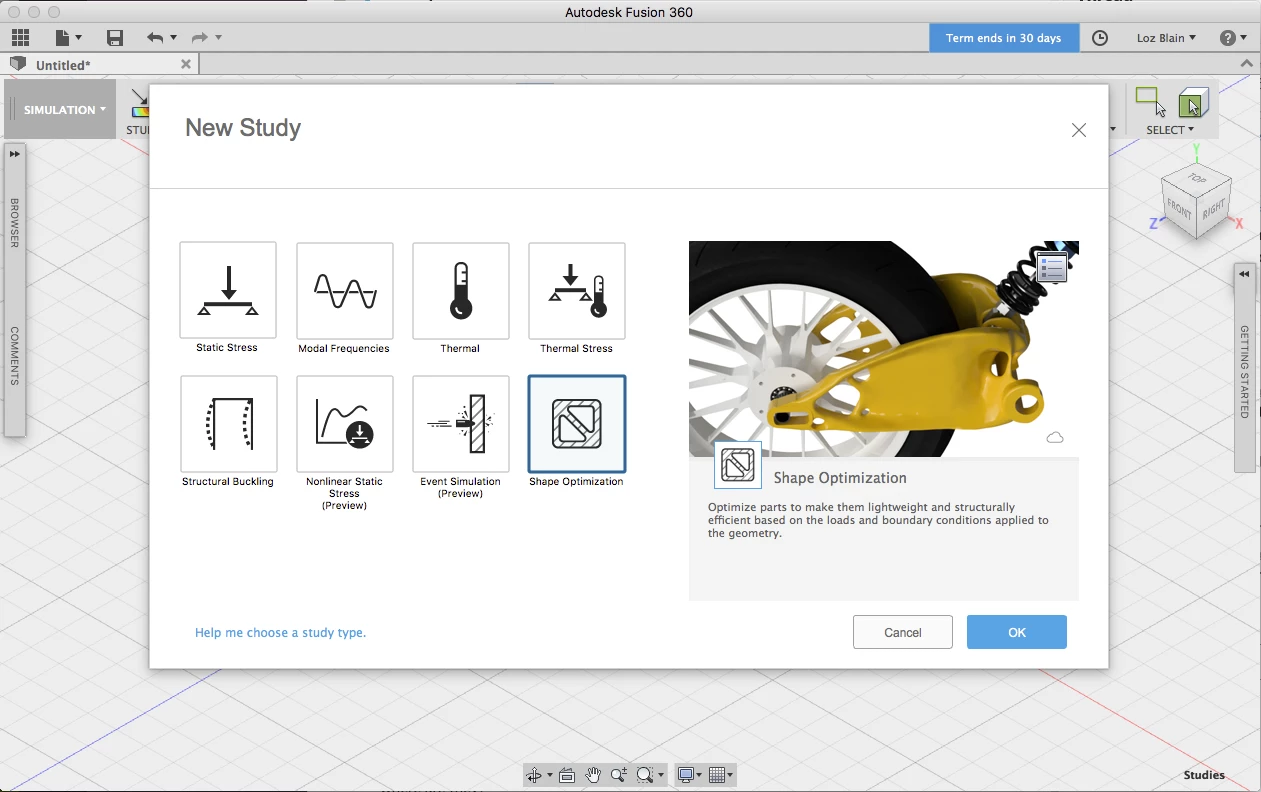
Autodesk's generative design tool works roughly like this: you design a rough shape for a component, then you lock in certain areas like mount points, or cylindrical holes that a bearing needs to go into, for example. You can choose to maintain symmetry down certain axes if that's important to you. Then you tell the system what loads the part needs to endure, from which angles, and what it's optimizing for – for example, stiffness and light weight.
Then, with the click of a button, the computer takes your basic shape and runs a heap of simulations, removing bits here and there and analyzing what each change does for its load bearing capacity. You can accelerate the process using the distributed power of cloud computing to get your results quicker.
At the end of the process, the computer spits out a design, or a range of designs, that meet your design criteria while optimizing for, in our example, stiffness and weight. Unsurprisingly, there's barely a straight line to be seen. The forms are decidedly skeletal to look at; the computer's accelerated simulation process appears to come to a lot of the same conclusions evolution has. Where there's stress, things get thicker and denser. Where there's not, things get thinner and lighter.
You can see how quick and easy this whole process is in the (nearly unedited) video below.
Now, while these forms are often prohibitively difficult to manufacture using traditional means, they're a perfect use case for 3D printing.
Effectively, what seems to be on the horizon is a two-headed design and manufacturing revolution that not only changes the way we build things, but the shapes of the products themselves. A new world where we see far more organic shapes, and fewer perfect geometric ones in our industrial design, our furniture, our cars, our architecture.
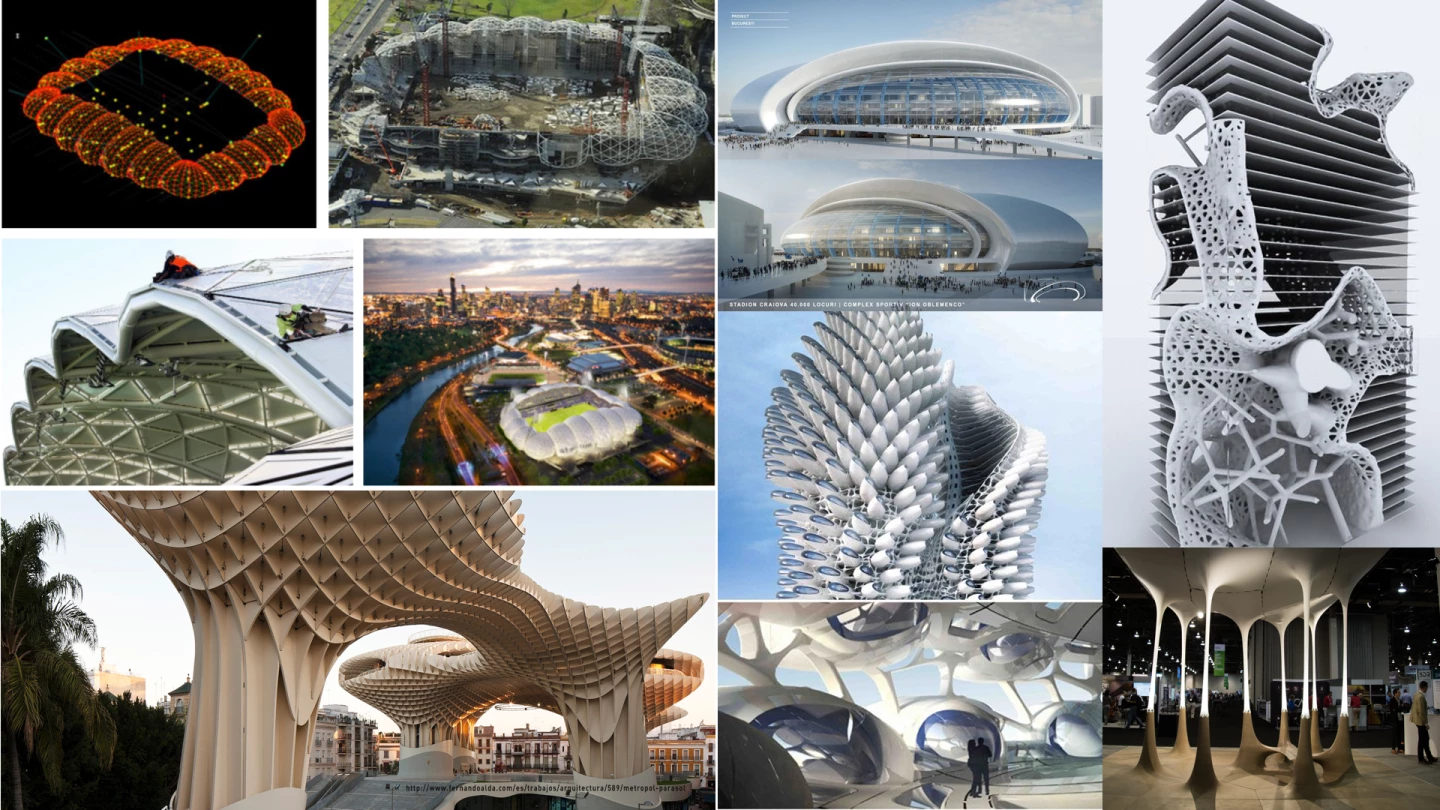
This is clearly exciting stuff. We spoke to Autodesk's Richard Elving about the generative design tool, the coming design and manufacturing revolution and which countries are best placed to take advantage of it – as well as "Project Dreamcatcher," the next step in generative design, where products begin re-designing themselves using real-world usage data.
A transcript of our chat follows:
Loz: From a basic level, what is generative design?
Richard Elving: It's a fascinating technology that could re-shape the way we look at everything. The easiest way to explain it is that for the last 100 years, we've been approaching manufacturing by taking material, and removing parts of it, whether it be wood, or steel, or whatever, to create the product that we imagine.
There's a human drawing the lines, drawing the shape, and then removing parts of it to create out end product. That's what we've been doing for hundreds of thousands of years, if you look at it, from stone or from steel.
With generative design, we have the potential for humans not to draw the lines and shapes anymore. A computer will generate the optimized design or product or building for us. And it'll produce such optimized, organic shapes that we can no longer use subtractive manufacturing. We'll have to use things like additive manufacturing to print the product.
You can tell the computer "I want to create a chair. And the chair needs to be at this price, in this material, and it needs to be able to hold this much weight, and with roughly these dimensions.
And then the computer generates hundreds, or thousands, of different designs that suit your criteria. And your job as the designer or engineer of tomorrow will be to pick the design that fits your purpose best.
It'll basically run a heap of algorithms to produce organic shapes. These are likely to be impossible to produce using traditional manufacture, they'll need to be printed. In a lot of cases, they're half the weight of the equivalent parts we've been using, but just as strong, and they use far less material. It's fascinating.
Loz: I've been fascinated by just how easy this tool seems to be to use, I've been watching some videos on YouTube. Can you talk me through the steps you need to go through to take advantage of that tool?
The current technology that we're shipping today, that Autodesk customers have access to – like what Top EV Racing's 5,000 horsepower dragster is using – the process is that you go in and design a component. Let's say a bracket component in the engine. Once you've created your solid object, and you've selected where it needs to be fixed and mounted and such, then you go into the generative design tool – it's built into Autodesk Fusion 360 that Top EV has used.
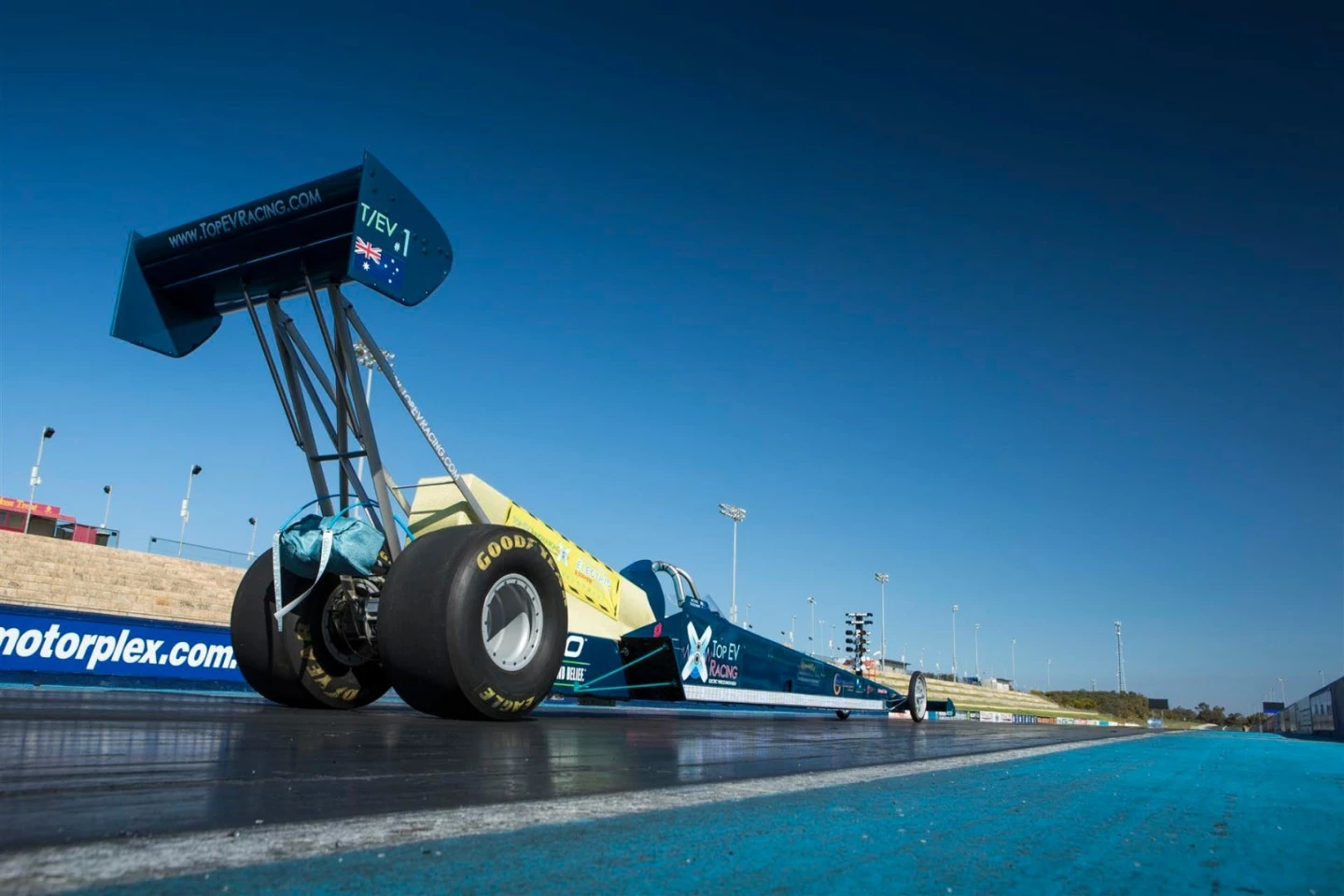
And then you say "I wanna be sure that this component can endure this much stress, from these directions, and it needs to be made in this material." And it runs a series of calculations, and gives you a suggested optimized design.
This optimized design, you'd have to look at it, but based on the calculations and the input of the computer, you'll now have a more organic shape. And you have to take into consideration whether that's going to work in your design, but the computer has basically co-worked with the designer to produce an optimal design.
Loz: So it's really a matter of getting the constraints exactly right?
That's right. That's stage one, that's the existing technology. What we're doing with stage two is that we're going to be able to mount sensors on the chassis, or the components of the vehicle. These sensors will pick up the stresses and the impacts that these different components endure in the field. And once we get the vehicle back for a service, we can take all the information back from those sensors, analyze it, put it into the generative design tool, and then it'll generate a further optimized design based on real-world impact.
It's called Project Dreamcatcher, it's pretty mind-blowing. So I, as a designer, won't be drawing the lines or shapes of the component, they'll be generated out of real world analysis.
As manufacturers, we might draw a steel frame a certain way because that's what we've always done. It's been there for 30 years. But with generative design, bringing in a product's real-world stress loads, it has the potential to re-generate an entire product in a way we've never thought of.
One company we've been doing that with is Hackrod. They're making a generatively designed speedster car called "La Bandita". They built a chassis, and then we put the sensors on to feed information back to the tools, and the tools generated an organic chassis that's 30 percent lighter than the one we started with.
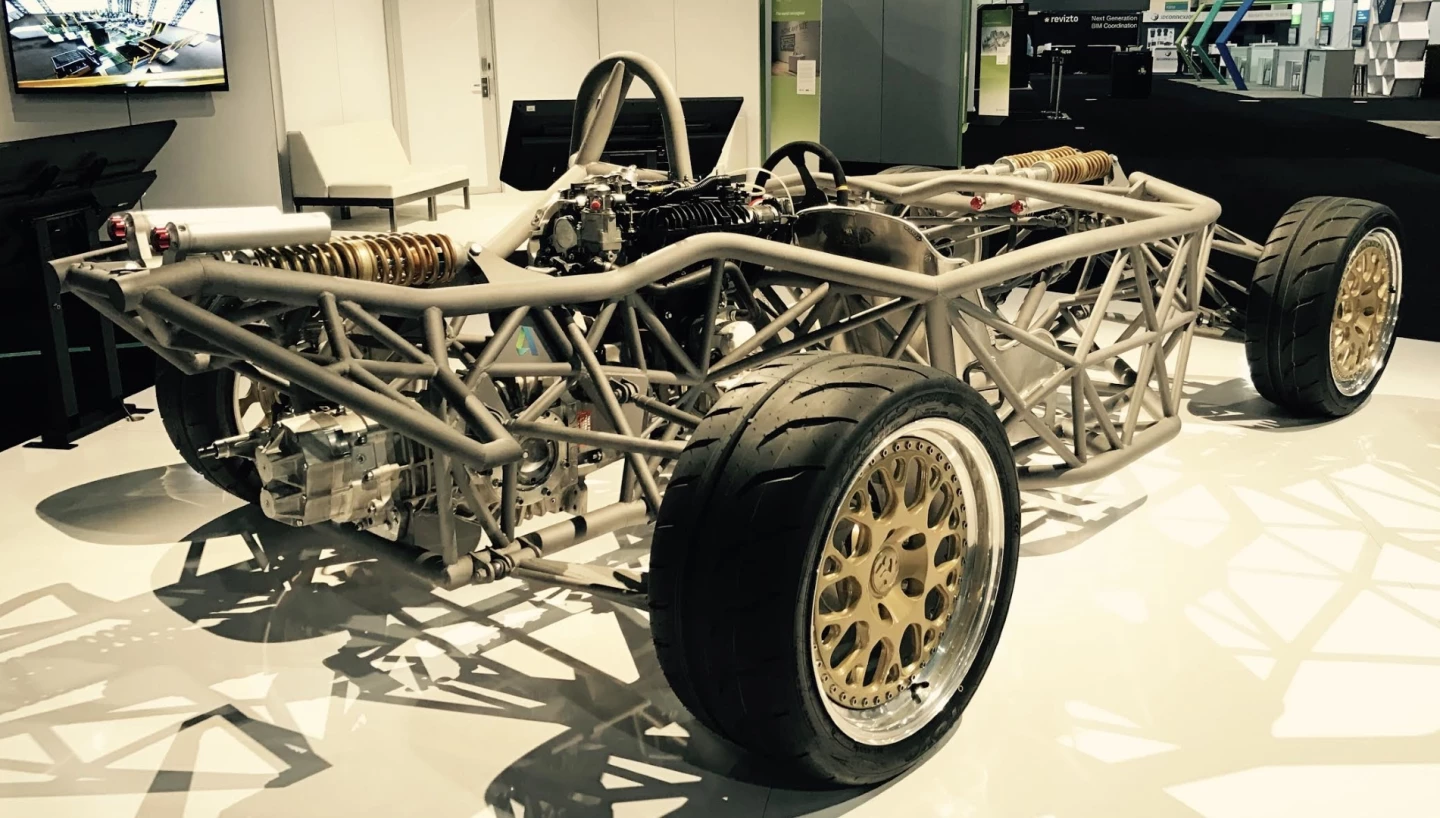
No human has basically been involved in the design process. That's where we are today. The first generation, everyone with Autodesk has access to that. The next generation, we expect to release that in early 2018. It's not that far away, six months' time.
Manufacturers in Australia and around the world will have access to this powerful technology, and I don't think manufacturers have fully realized what it means. If we don't investigate and adopt this technology today, companies in Germany, America, China will adopt it, and invent at a much faster rate than what we're doing, and effectively they may make us redundant. That's how serious it is for manufacturers.
Loz: So it seems like the key advantages you can get from running your parts through this kind of process are using less material, strength and light weight. Are there any other kinds of things you can optimize for?
At the moment, those are the main benefits. And with less material, the product will be lighter, but it'll also be cheaper to manufacture as well. A lot of the materials that go into products as they exist today, maybe they don't need to be there.
We do have a habit of over-designing and over-engineering our products. And we do it because we've always done it that way. The problem with that, let's take the transportation industry… That leads to excessive emissions and fuel costs, things like that.
Loz: We've talked quite a bit about the automotive area; what other industries are you seeing huge benefits for?
Well, today, obviously automotive and aerospace – companies like Airbus are using this technology already. We've been working with them over the last year to optimize one of the partitions in the Airbus 320. We were able to reduce it to 30 percent of the weight, and of course that makes a huge difference for efficiency and emissions, and ultimately helping the airlines bring the ticket costs down.
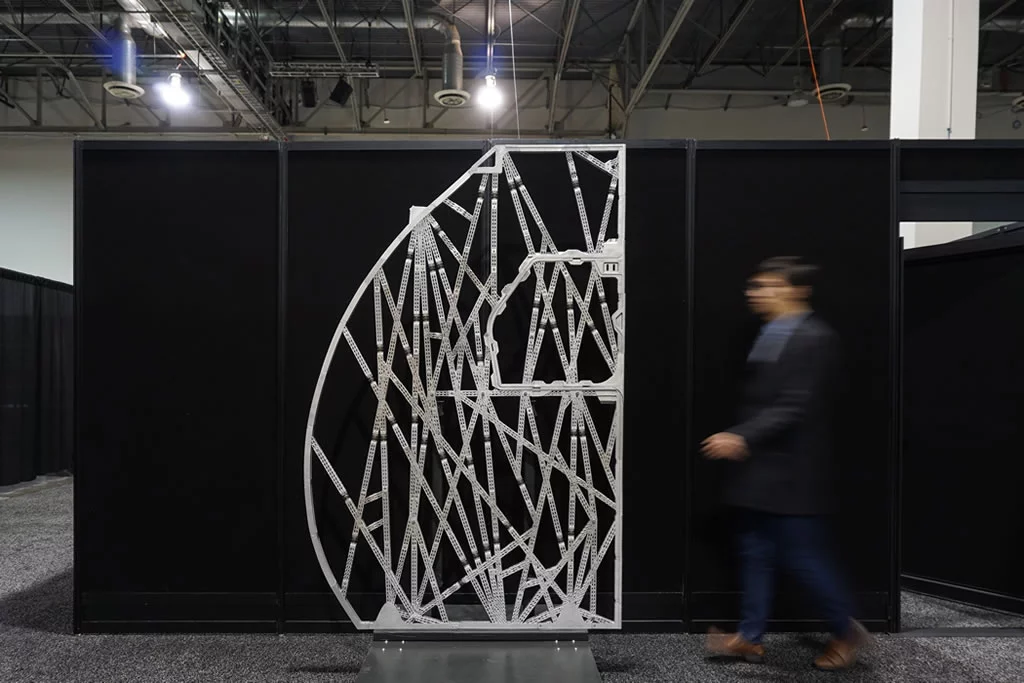
Automotive and aerospace are such an easy return on investment, because they're all chasing weight and space. But it doesn't have to be limited to that. It could be anything where the cost of materials is expensive to manufacture.
It could be any components that need to be in titanium… we do some work with medical devices and implants. If you need to do a jaw implant, for example, you want to use as little titanium as you can. You don't want to go around putting extra metal in your body if you don't have to.
So in some cases we're using generative design where we take the shape of someone's jaw, and putting the information in on where things need to be fixed, or how things need to look to maintain the shape of someone's face, and we're running it through generative design to optimize the shape.
Loz: That's almost like using a computer to beat evolution at its own game.
It is! That's exactly what it is. This is AI when it comes to design. In some cases this has the potential to change people's lives.
We have also been working with Under Armour, the shoe manufacturer. They're 3D printing the bottom of the shoe. They're trying to work out how to make the lightest sports shoe. And in that case, we took the information of what the shoe looks like currently, and put that into the generative design tool, and of course it produced this organic, cool looking bottom of the shoe that could only be 3D printed.
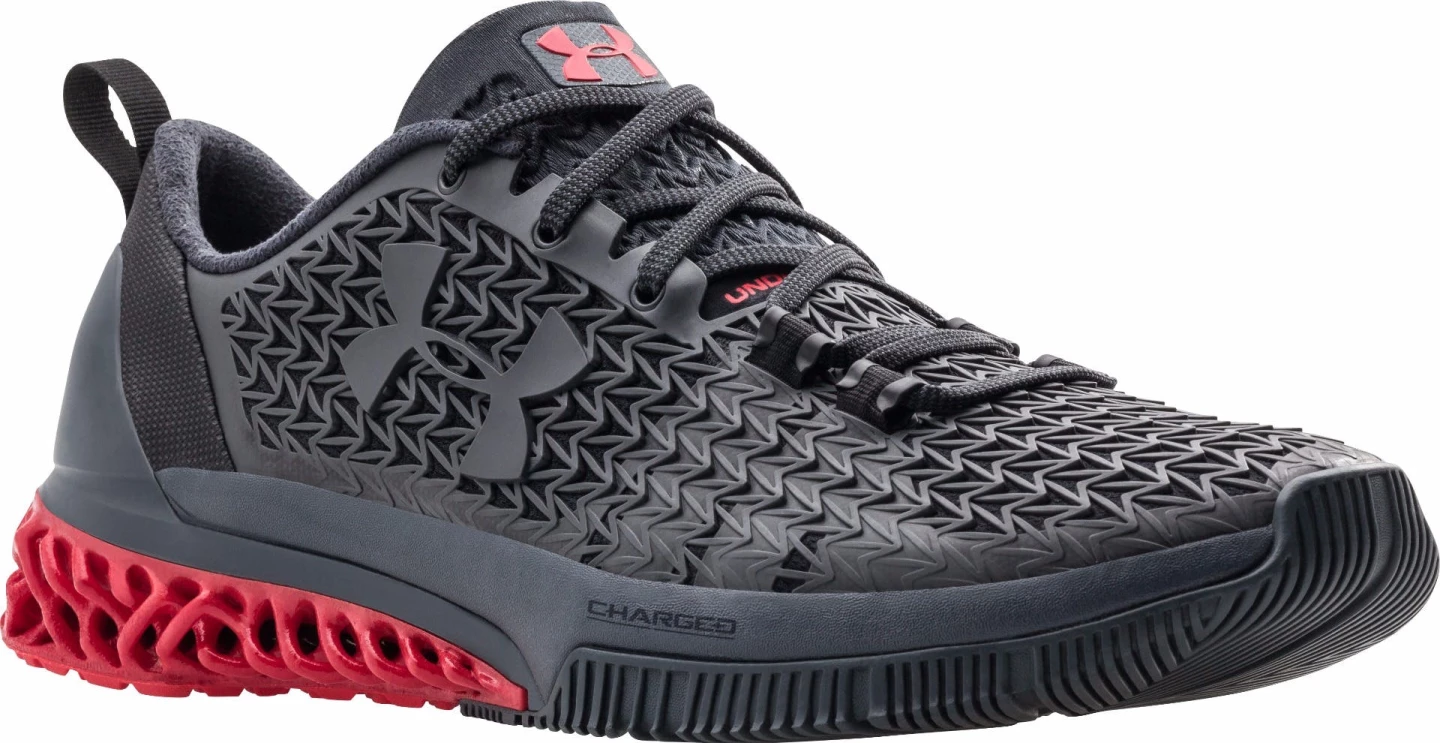
It'll all become smarter with time.
Loz: And it all relies on the progression of 3D printing.
Yes. Let's say 5 percent of a product today is manufactured using additive. But in the future, that could be up around 40 or 50 percent. There was an article I read yesterday, with metal 3D printers becoming 100 times faster and 10 times cheaper. Fascinating.
These two things coupled may disrupt the market. Generative design tools and, say, a metal 3D printer coming out of Perth from Aurora Labs that's gonna cost AU$50,000. That's the vision of the founders, they're not shipping the product yet. Any company can afford that. So if you're a traditional company that's drawing the lines, not running the simulations, and a startup comes along. You might have been in business 30 years, but overnight your product becomes redundant. They can produce quicker, do one-offs, they're optimized.
Loz: What sort of timeframe do you see for this flip, when additive becomes competitive with traditional manufacture?
We believe that by 2020, this is not going to be sci-fi anymore, it'll be everyday. That's the message we're taking to manufacturers. You look back 10 years, we didn't have the iPhone. If you look how quickly things have changed in the last 10 years, with social media, instant access, CAD software on your mobile phone, your iPad, in the cloud…
We think that it's going to continue to accelerate. The kinds of leaps that happened in the last 10 years might happen in five. Things are going to speed up. If you look at the designers of tomorrow, like the guys out at Top EV, this younger generation, they're already starting to take this kind of stuff for granted.
Tomorrow's students and engineers, they'll just look at the job a lot differently. I think by 2020, nobody's going to want to interview me about this stuff. It'll be everyday.
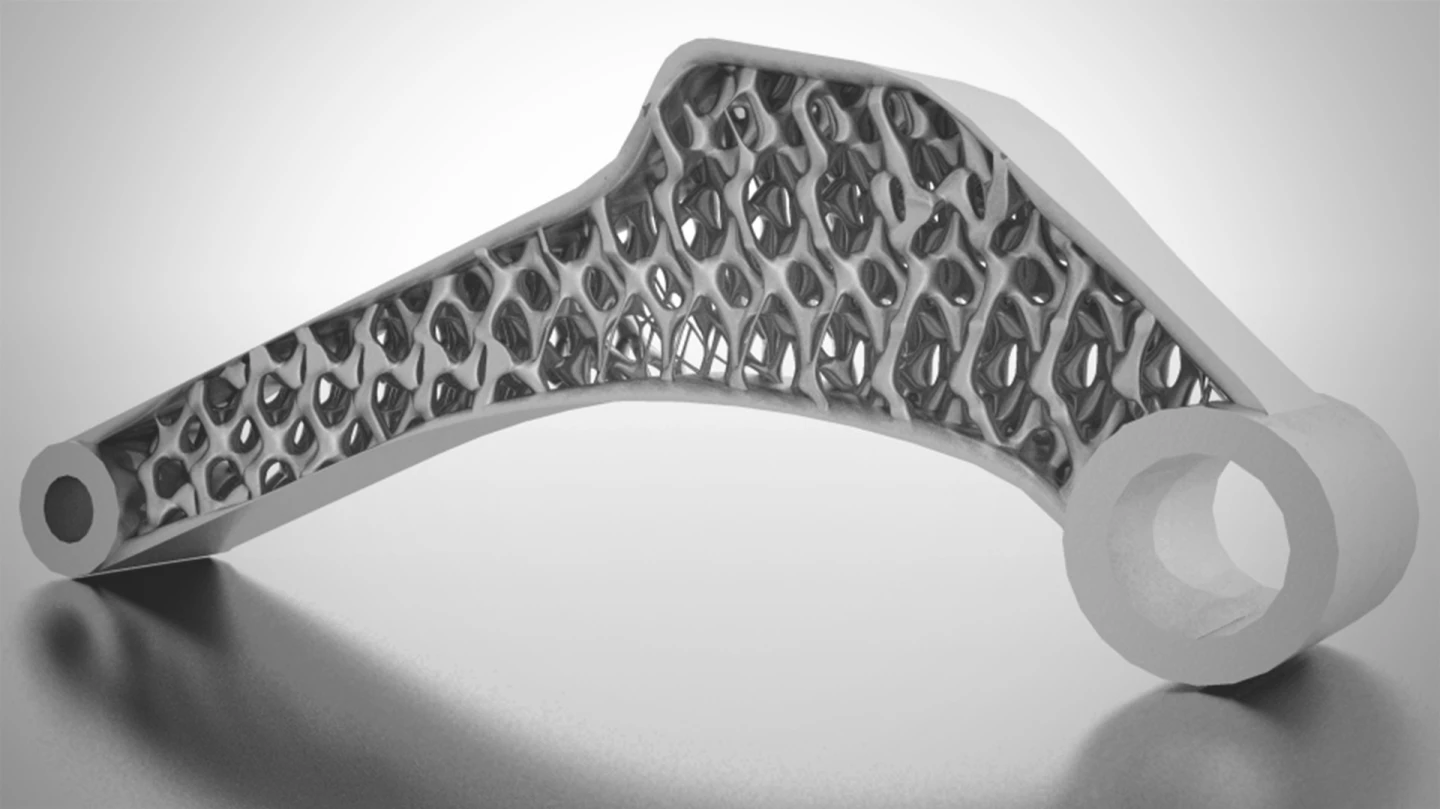
Loz: What metrics will we need to see before we know that additive has taken over?
What's holding it back today is the cost of the hardware. As soon as that comes down, and you've got machines that can print on large scale for the cost of CNC, I think that'll happen very quickly.
But we also hope these things will be available through what we call push-button manufacturing, where if you want to print something, you can go online, find a free 3D printer somewhere, upload your model and have it printed straight away. It's really only the hardware cost that's holding us back today.
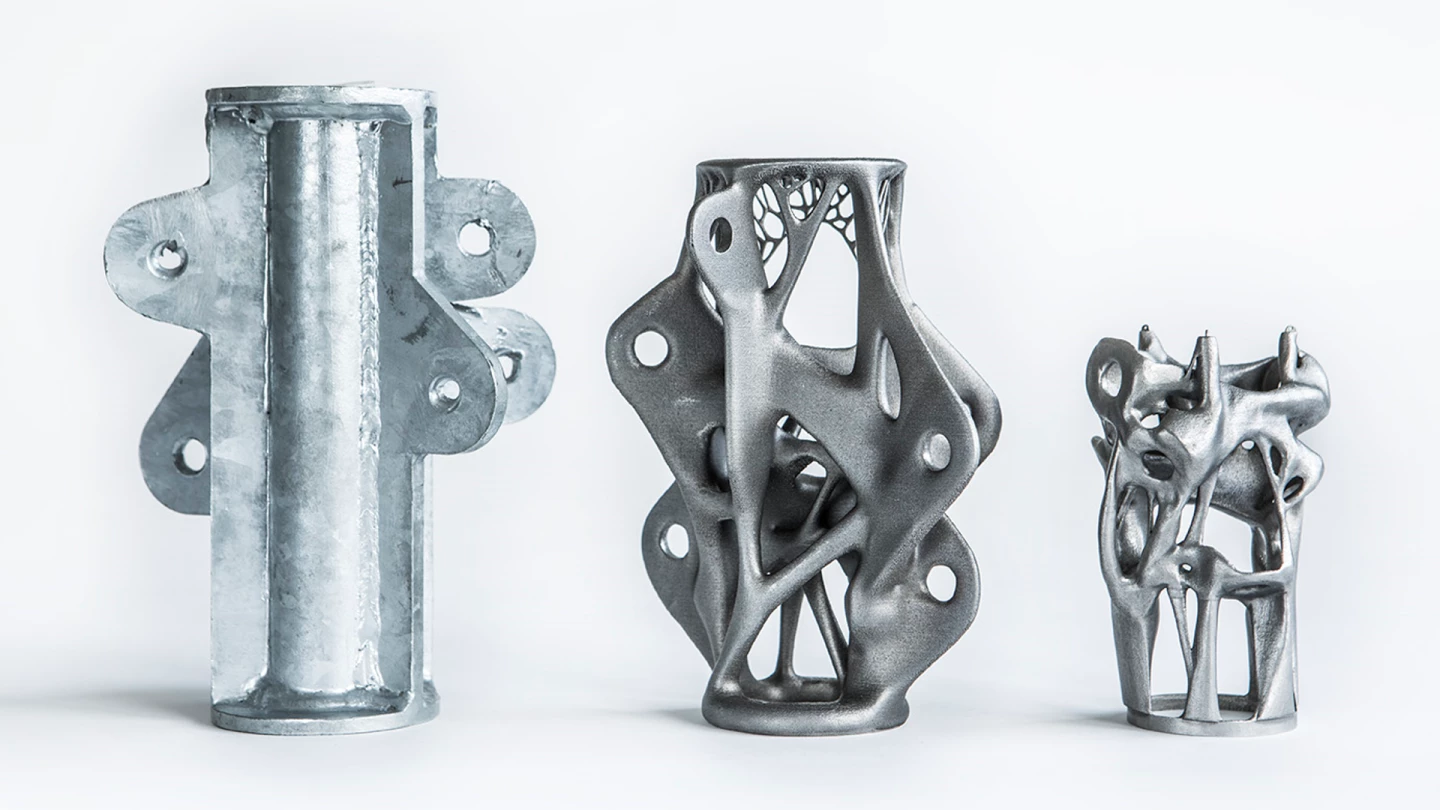
Loz: We're getting a little off track here, but when this starts happening, which countries are best placed to compete in this new economy?
Unfortunately, it's not Australia. I'm very passionate about Australian manufacturing, I've been here for 10 years, originally from Sweden. We're not up there. The short answer is that it's America, Germany and China that lead the way when it comes to 3D printing.
In China, they've already 3D printed things like buildings, they've come a lot further than us when it comes to portable buildings and manufacturing them offsite. In Australia, 3D printing is still more about quick prototyping or showing off the technology, we're not actually producing the end product. In those countries I mentioned, they're shipping 3D printed products.
And as we know, it's a global economy now. You can be anywhere in the world and come up with a cool generative design, optimize it, find a local 3D printer, get yourself a million dollars on Kickstarter and go disrupt a field within a few weeks.
More information: Project Dreamcatcher