To paraphrase Samuel Johnson, there was a time when 3D metal printing was like a dog walking on his hind legs – it wasn't done well; but you were surprised to find it done at all. Now that laser sintering or Selective Laser Melting (SLM) is used for everything from printing rocket engine components to semi-automatic pistols, the time for surprise may b long past, but the technology still has plenty of room for improvement. That's why researchers at the Lawrence Livermore National Laboratory (LLNL) are working on simulations to improve the speed of 3D laser printing and the quality of the final product by using higher-powered lasers.
SLM is a form of additive printing where, instead of squirting melted plastic out like cake icing, an object is built up layer by layer using metal powder that’s melted into a pool by a high-power laser. As each layer is fused into the desired shape, the printer adds another layer of powder and the process repeats until the printing is completed. Then, you remove the excess powder, give the printed object a polish, and you’re done.
The problem is that 3D printing is rapidly developing from a novelty into a mainstream manufacturing technique. That means that processes like SLM need to improve quickly in terms of predictability, quality, and speed of output. In the case of SLM, a key question is how to get the resulting metal as close as possible to full density in as short a time as possible.
This is where the LLNL study has concentrated its efforts. Currently, laser printing works best when the laser is kept below 225 W. The researchers wanted to figure out how to get the same results with lasers in the 400 W range, but that meant dealing with a wide range of factors, such as laser power, laser speed, the distance between laser scan lines, the scanning strategy, and powder layer thickness.
Since SLM works by melting powders, porosity was a major problem. If the grains of powder don’t melt properly, the metal, in this case 315L stainless steel, becomes porous, and therefore weaker. For many applications, engineers require porosity of less than 1 percent, but that means balancing the various factors.
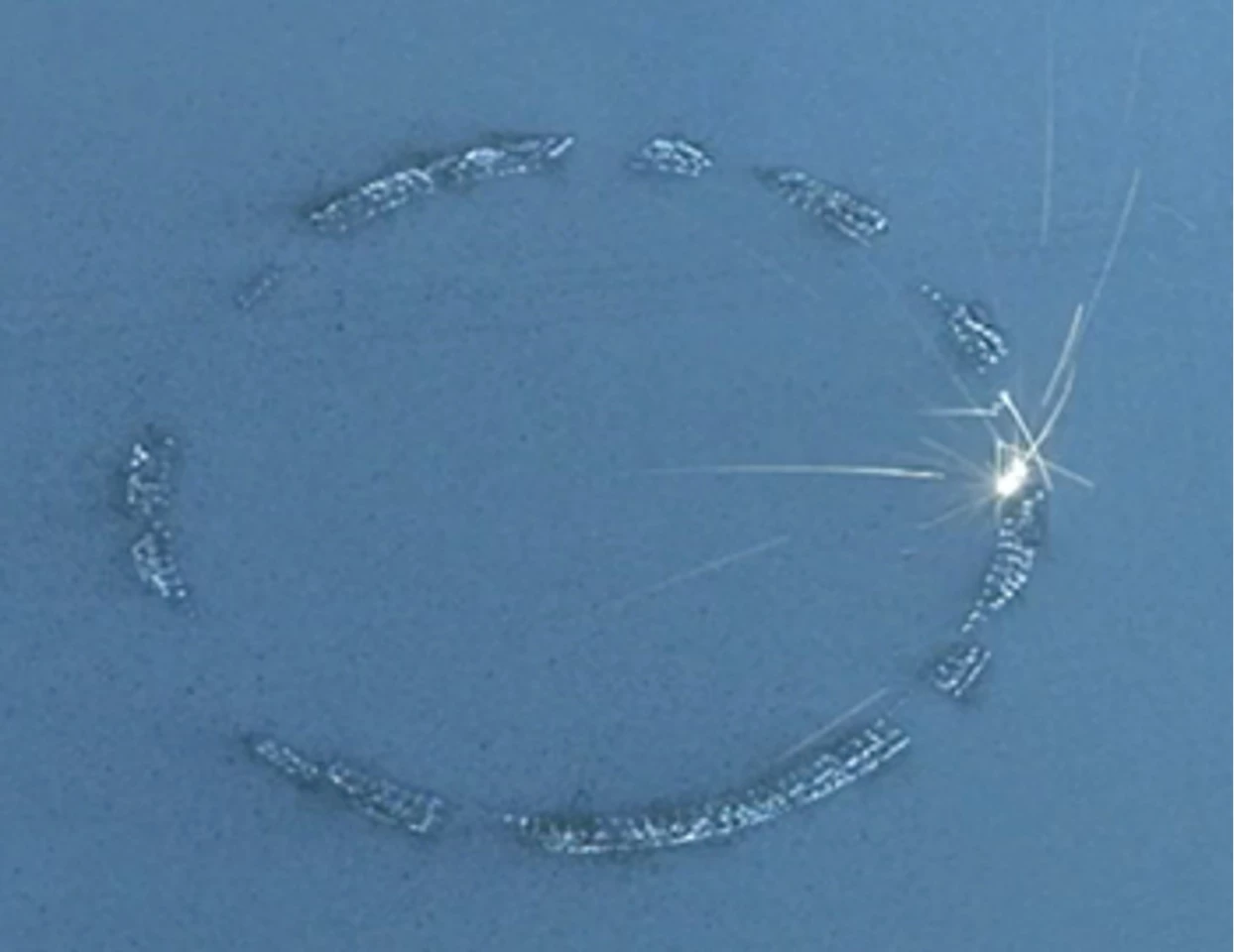
To achieve this balance, LLNL is developing computer models that predict the optimum balance of the various parameters for the fastest and most cost-effective way of carrying out a particular high-density printing process.
"We mine the simulation output to identify important SLM parameters and their values such that the resulting melt pools are just deep enough to melt through the powder into the substrate below," says Chandrika Kamath, an LLNL researcher. "By using the simulations to guide a small number of single-track experiments, we can quickly arrive at parameter values that will likely result in high-density parts."
"We found that the metal density reduces if the speed is too low, due to voids created as a result of keyhole mode laser melting, where the laser drills into the material," added Kamath. "At the same time, too high a speed results in insufficient melting. The key is to find the right parameters where the melting is just enough."
One result that’s of particular interest is that the team learned that using higher power provided a more consistently high density material for a wide range of metal powders, while lower powers had a greater range of porosity. According to the team, the simulations will be helpful in understanding the process parameters and certifying the properties of printed metal parts.
The teams results were published in the International Journal of Advanced Manufacturing Technology.