Spectators of the DARPA Robotics Challenge finals in 2015 would have noticed that many of the competing robots were padded up for protection in case they took a tumble. MIT's Computer Science and Artificial Intelligence Laboratory (CSAIL) is looking to build customizable shock-absorbing protection into robots by using 3D printing to produce soft materials that not only dampen the impact of falls, but also allows them to carry out safer, more precise movements.
Robotics engineers have long had a keen interest in soft materials. At their simplest, such materials can protect robots against falls and collisions, but can also protect people in environments were robots and humans are increasingly working together. Going beyond this, soft materials also allow for making completely soft robots that can mimic animal design.
Using 3D printing technology, CSAIL is creating soft materials that can change the basic capabilities of the robot. Called programmable viscoelastic material (PVM), it's based on the idea of controlling the stiffness and elasticity of a substance to change how it moves and responds. In this way, engineers can tailor the material for the task at hand.
Rubbers and plastics are viscoelastic and are the most common dampers, but their properties are set by the manufacturer and it's difficult and expensive to make bespoke versions. According to CSAIL, the answer was to use 3D printing to customize PVMs by adding pockets of liquid in pre-planned quantities and distributions that determines the stiffness or elasticity of not only the end material, but specific parts of the end material if so desired.
For the MIT process, an inkjet printer laid down droplets of different materials layer by layer and a UV light solidified the non-liquid areas in the desired pattern, leaving behind the liquid-filled cavities.
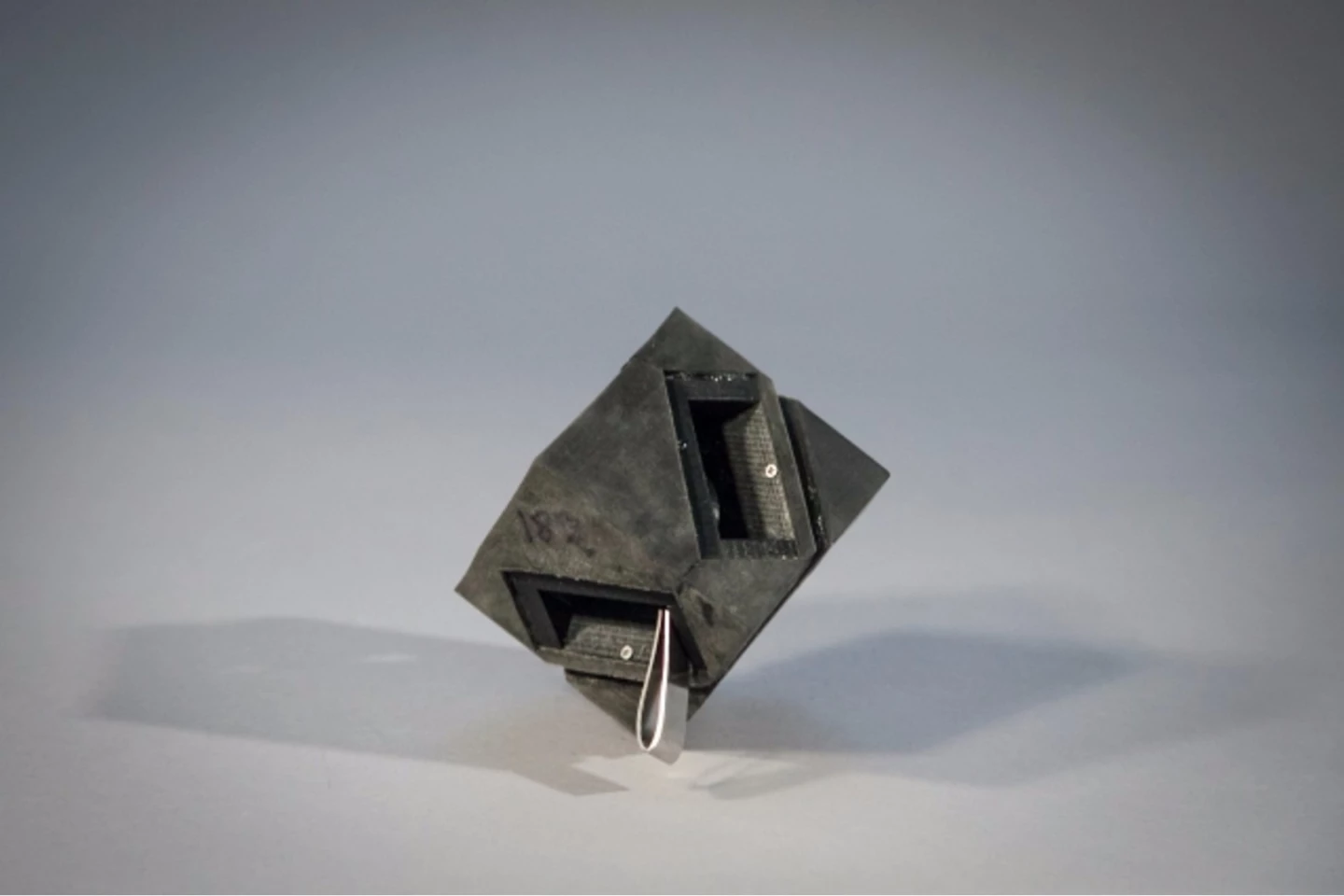
To test the new materials, CSAIL built cubical robots with a rigid body, two motors, a microcontroller, battery, four layers of looped metal strips acting as springs for propulsion, and inertial measurement unit sensors. These were all wrapped with the various test materials to serve as shock-absorbing skins for evaluation.
The results were some robots that could bounce very high, or others that bounced very little and could land on a desired spot with four times the precision of the high bouncer. CSAIL says that not only does this allow for the construction of much more durable robots that transfer less than half the energy normally transferred to the ground on impact, but ones where the properties can be set as desired at the moment of printing instead of relying on a bespoke factory run.
CSAIL sees a wide range of applications of 3D-printed PVMs. Aside from improving the safety and controllability of robots, it could also be used to prolong the life of delivery drones, improve running shoes and safety helmets, and protect the delicate mechanisms in cameras and sensors.
"Being able to program different regions of an object has important implications for things like helmets," says postdoc student Robert MacCurdy. "You could have certain parts made of materials that are comfortable for your head to rest on, and other shock-absorbing materials for the sections that are most likely to be impacted in a collision."
The team will present their paper (PDF) at the IEEE/RSJ International Conference on Intelligent Robots and Systems in South Korea.
The video below outlines how the MIT softbot technology works.
Source: MIT