Like something out of a Robert Heinlein novel, students at the University of California, San Diego (UCSD) have built a metal rocket engine using a technique previously confined to NASA. Earlier this month, the UCSD chapter of the Students for the Exploration and Development of Space (SEDS) at the Jacobs School of Engineering conducted a hot fire test for a 3D-printed metal rocket engine at the Friends of Amateur Rocketry launch site in California’s Mojave Desert. This is the first such test of a printed liquid-fueled, metal rocket engine by any university in the world and the first designed and printed outside of NASA.
The Tri-D rocket engine, as it’s called, was designed and built with the cooperation of NASA’s Marshall Space Flight Center as part of an effort to explore the feasibility of printed rocket components. For purposes of the exercise, it was designed to power the third stage of a Nanosat launcher, that is, one capable of launching satellites that weigh less than 1.33 kg (2.93 lb).
Tri-D is only about 7 in (17.7 cm) long and weighs about 10 lb (4.5 kg). Made of a chromium-cobalt alloy, it burns kerosene and liquid oxygen and produces about 200 lb (90.7 kg) of thrust. The students’ main contribution was design of the injector plate, which is a key component used to inject fuel into the combustion chamber. In this case, the injector has a Fuel-Oxidizer-Oxidizer-Fuel inlet arrangement with two outer fuel orifices converging with two inner oxidizer orifices.
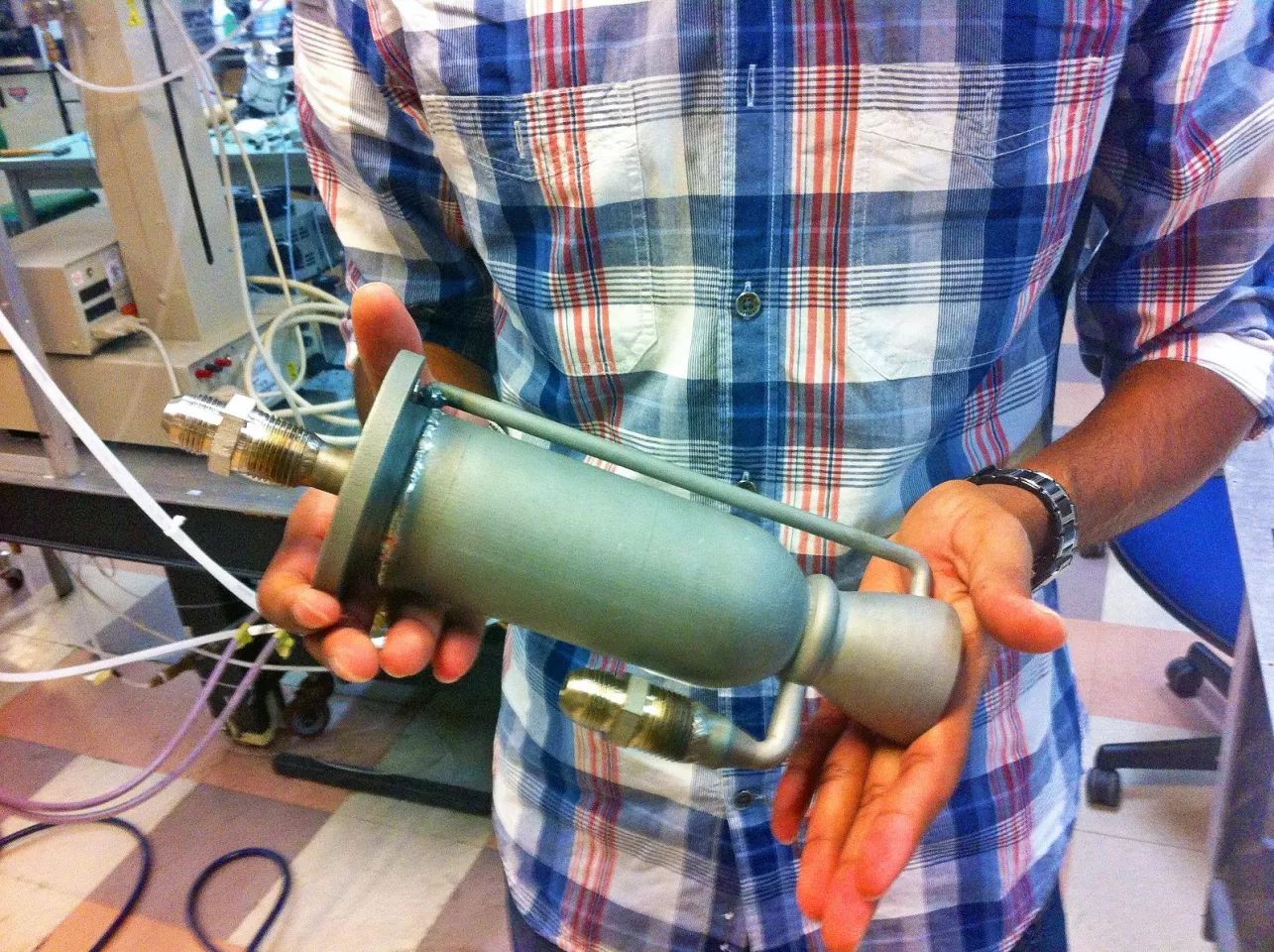
The rocket has a regenerative cooling jacket that extends to the nozzle to keep the engine cool while firing. It was designed to burn the fuel in the middle of the combustion chamber to keep as much heat as possible away from the chamber walls, while insulating them with a boundary layer of relatively cool gases.
The Tri-D engine cost only US$6,800 with NASA putting up US$5,000 and the students collected the balance with fundraisers, such as barbecue sales.
The engine was printed by GPI Prototype and Manufacturing Services using a technique called Direct Metal Laser Sintering (DMLS). In this 3D printing process, a powder of the chromium-cobalt alloy is spread in a thin layer by the printing machine. A computer-controlled laser then fuses the powder into a cross section of the engine component. The machine spreads a second layer of powder and the process repeats until the component is complete. The excess powder is then removed as are any temporary supports printed to hold the component together during printing, then it’s hardened, polished and assembled.
The advantages of 3D laser printing is that it’s much cheaper and faster with jobs normally taking weeks being completed in hours. Also, printing allows for more intricate designs for each piece and, therefore, fewer parts for the finished product. In addition, printed alloys have greater tensile strength than castings.
According to UCSD, the the tests at Mojave went without a hitch and the engine exhaust achieved supersonic velocity. "It was a resounding success and could be the next step in the development of cheaper propulsion systems and a commercializing of space," says SEDS President Deepak Atyam.
In addition to the successful test, the Tri-D design won the Student Prize award in the DIYRockets competition hosted by DIYRockets Inc.
The video below shows the test firing of the Tri-D rocket engine.
Source: UCSD