Star Trek's Mr. Scott will have fewer reasons to panic as the day comes closer when even rocket engines can be cranked out on 3D printers. In recent tests, NASA and Aerojet Rocketdyne fired a rocket engine injector at NASA's Glenn Research Center in Cleveland, Ohio that was made using a 3D printer. The project, done in collaboration between NASA and private industry, aims at speeding up the manufacture of rocket components while reducing costs as well as eventually printing them in space.
The 3D printing process that was used is known as a laser additive process. Unlike other 3D printing techniques that deposit layers of plastic or other materials to build an object, this process uses high-powered lasers focused on a bed of metallic powder. The laser melts a fine line of this powder into solid metal and then another powder layer is added. In the end, the excess powder is brushed off and the final product remains.
The purpose of the tests was to study the ability of the current state of technology to design, manufacture and test a critical rocket engine part using 3D printing. The tests did not involve the manufacture and firing of a complete liquid rocket engine, but instead just the rocket engine injector assembly – a key component that mixes propellants and determines the performance of the engine. There are several types of rocket injectors, but NASA did not specify which was used in the tests.
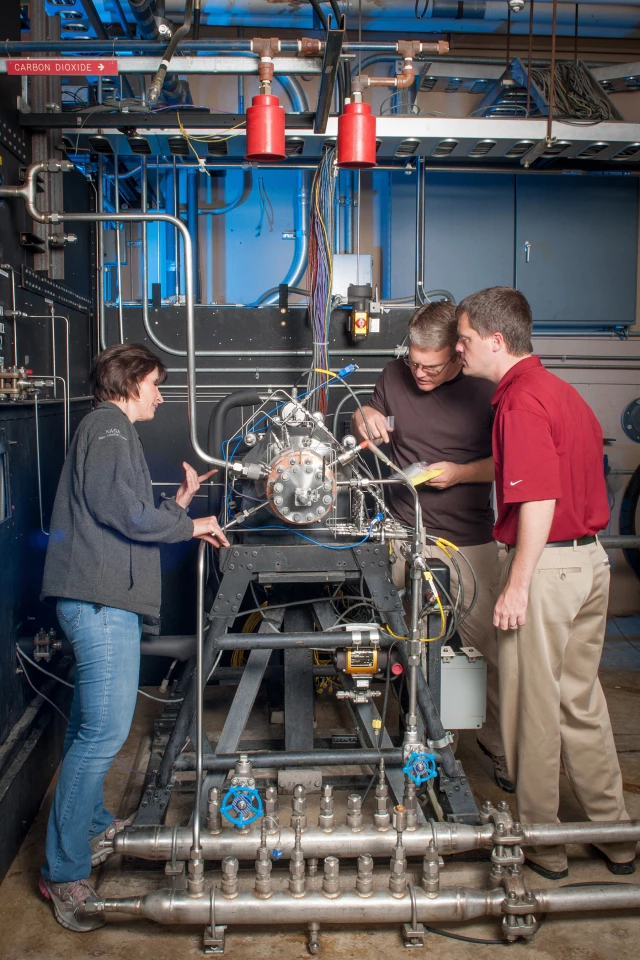
"NASA recognizes that on Earth and potentially in space, additive manufacturing can be game-changing for new mission opportunities, significantly reducing production time and cost by 'printing' tools, engine parts or even entire spacecraft," says Michael Gazarik, NASA's associate administrator for space technology. "3-D manufacturing offers opportunities to optimize the fit, form and delivery systems of materials that will enable our space missions while directly benefiting American businesses here on Earth."
According to NASA, the benefits of 3D printing of rocket components are considerable. With 3D printing, a component that would take a year to make could be manufactured in less than four months at cost 70 percent below that of conventional methods.
Source: NASA