The list of materials capable of being extruded through a 3D printer seems to grow by the week, moving well beyond plastics, food and metals to now include another unlikely substance: glass. And while previous 3D printing methods have used powdered glass and silica sand, a team of researchers led by Neri Oxman out of MIT’s Mediated MatterGroup has developed a 3D printer that extrudes molten glass.
Dubbed G3DP (Glass 3D Printing), the method is the first-of-its-kind optically transparent glass printing process that uses a fully functional material extrusion 3D printer. It essentially takes the ancient process of glassmaking developed some4,500 years ago and updates it with 3D technology to produce an array of quite beautiful glass objects worthy of a Dale Chihuly exhibit.
The most common type of 3D printer – fused deposition modeling (FDM) – has been limited to using material in filament form due to its inability to handle materials that require a high melting point. Unfortunately, this limits the size and scale of the final product. Advantages of glass in additive manufacturing are its hardness, durability and optical qualities, as well as its affordability and availability, with cheap and abundant silica sand, soda ash and limestone the main ingredients.
Working with molten glass presented unique challenges to the team. Glass objects need to be cooled down to room temperature in a slow, controlled fashion through a specific temperature range in what is known as the annealing process. This removes built-in stresses associated with thermal gradients that may otherwise lead to spontaneous breakage of the glass. The group initially used propane torches manually, but this proved too difficult to control and the objects cracked. A solution was found with the addition of a heated annealing chamber that the glass object was 3D printed into, allowing for a consistent and controlled temperature.
“The lower chamber acts as an annealer: it keeps the glass warm and it cools it down slowly to release the stresses,” said Giorgia Franchin, one of the researchers with Mediated Matter Group.
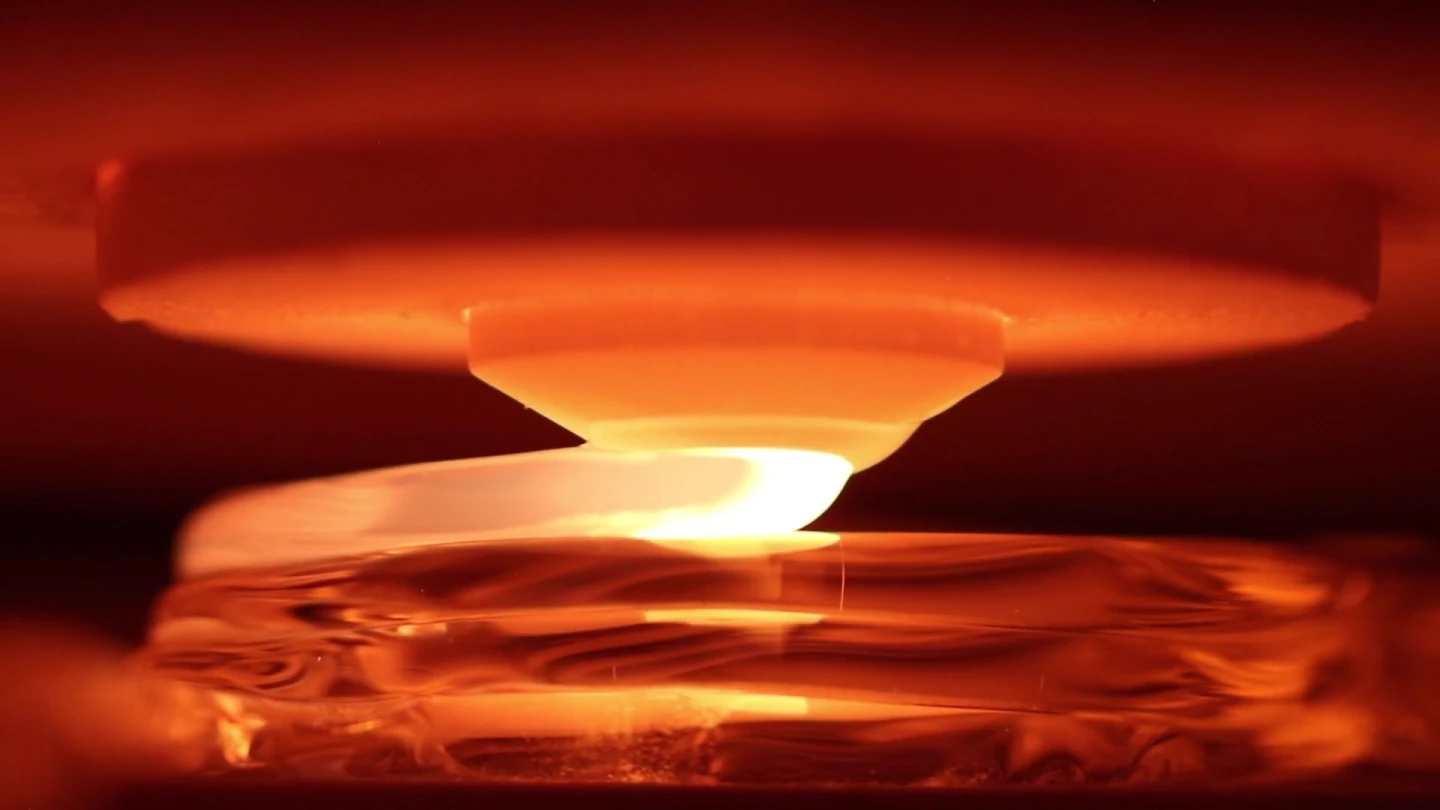
The 3D printer assembled by the group is made up of a kiln cartridge where molten glass beads are top loaded into a 1,800-watt crucible kiln chamber, which is essentially a furnace able to melt and maintain molten glass between1,040 and 1,165° C (1,904 – 2,129° F). The temperature, which affects glass viscosity, flow rate, layer height and feed rate, can be adjusted depending on the desired output. Using simple gravity, the molten material is extruded through a 10 mm-diameter, 300-watt ceramic nozzle heated to 1,000° C (1,832° F).
The size of the printed glass objects are currently limited by the size of the annealing chamber, which measures 250 x 250 x 300 mm (9.8 x 9.8 x 11.8 in). But the chamber comes equipped with a transparent ceramic window to monitor the building process, which resembles honey squeezed out of a bottle as it’s layered on top of previous levels.
Besides the artful glass objects created by the process, potential applications include bespoke lab equipment and parts for the aerospace industry.
The paper detailing the glass printer was published in the journal 3D Printing and Additive Manufacturing.
Source: Mediated Matter