3D printing single objects out of different materials can be difficult, if those materials cure at different rates. The new Inkbit system addresses that problem, and has been used to print a highly complex functional robotic hand … in just one print job.
Commonly used "additive manufacturing"-type 3D printers build objects up by depositing successive layers of molten polymers or other materials. On cheaper printers, the ridges where those layers don't perfectly line up with one another are often visible.
Much fancier 3D inkjet printers still build things up in layers, but they utilize multiple nozzles to deposit multiple types of polymer resin at the same time. An ultraviolet light is then used to cure the resins, after which an integrated scraper is utilized to shave down the ridges between layers.
This curing and shaving process goes on rapidly and continuously throughout the printing process.
Things get trickier when one of the resins cures considerably slower than the others. In this scenario, if the scraper moves in fast enough to keep the print job going quickly, the still-soft resin will smear. It will also cling to the scraper, gumming it up.
That's where the Inkbit system comes in.
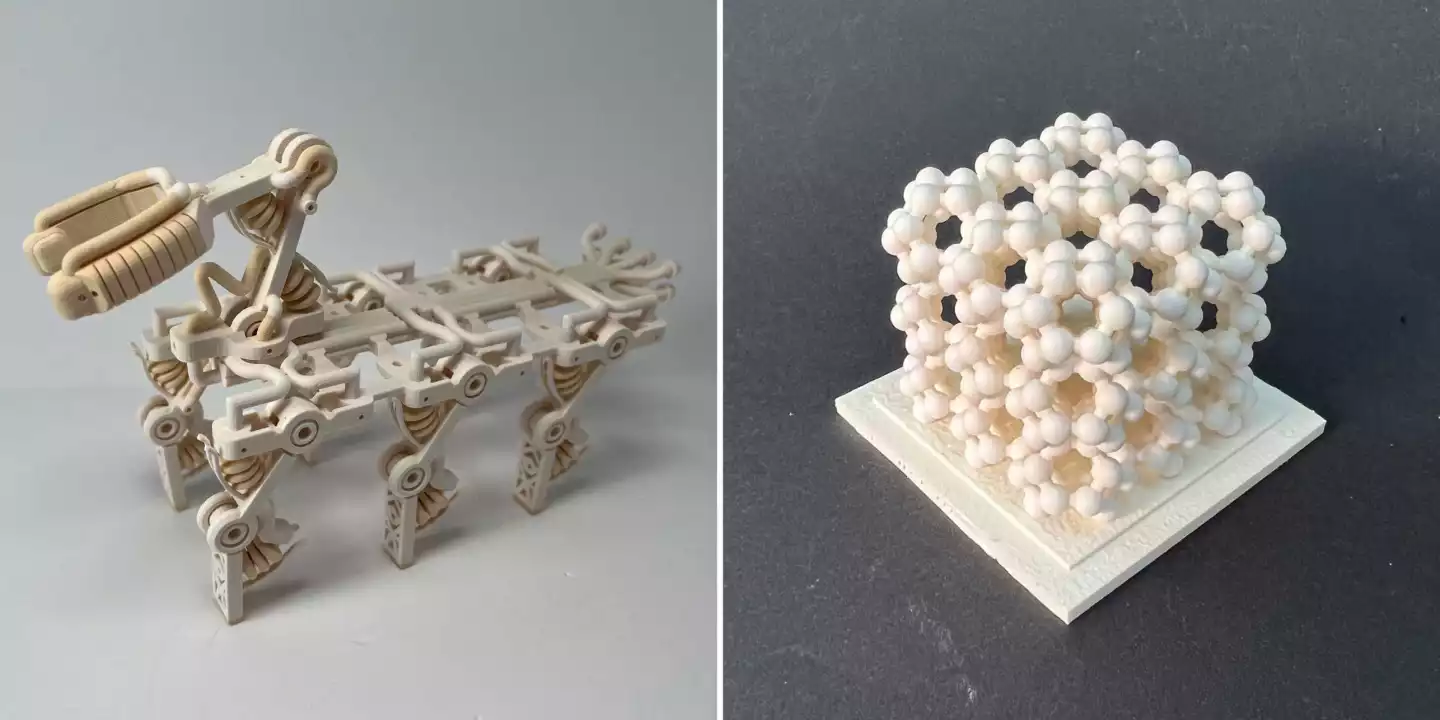
Developed via a collaboration between scientists at the ETH Zurich research institute and MIT, it does away with the scraper. Instead, it utilizes a technology called vision-controlled jetting, in which four high-frame-rate cameras and two lasers continuously scan the surface of the object being printed.
These scans are used to create an intricate depth map of the object, in which any imperfections on each layer are recorded as soon as it's deposited. When the successive layer is being deposited, the flow rates of the nozzles are adjusted in order to compensate for those imperfections, creating a smooth transition between layers.
As a result, the slower-curing resins have a chance to harden, and no ridges are present on the finished product.
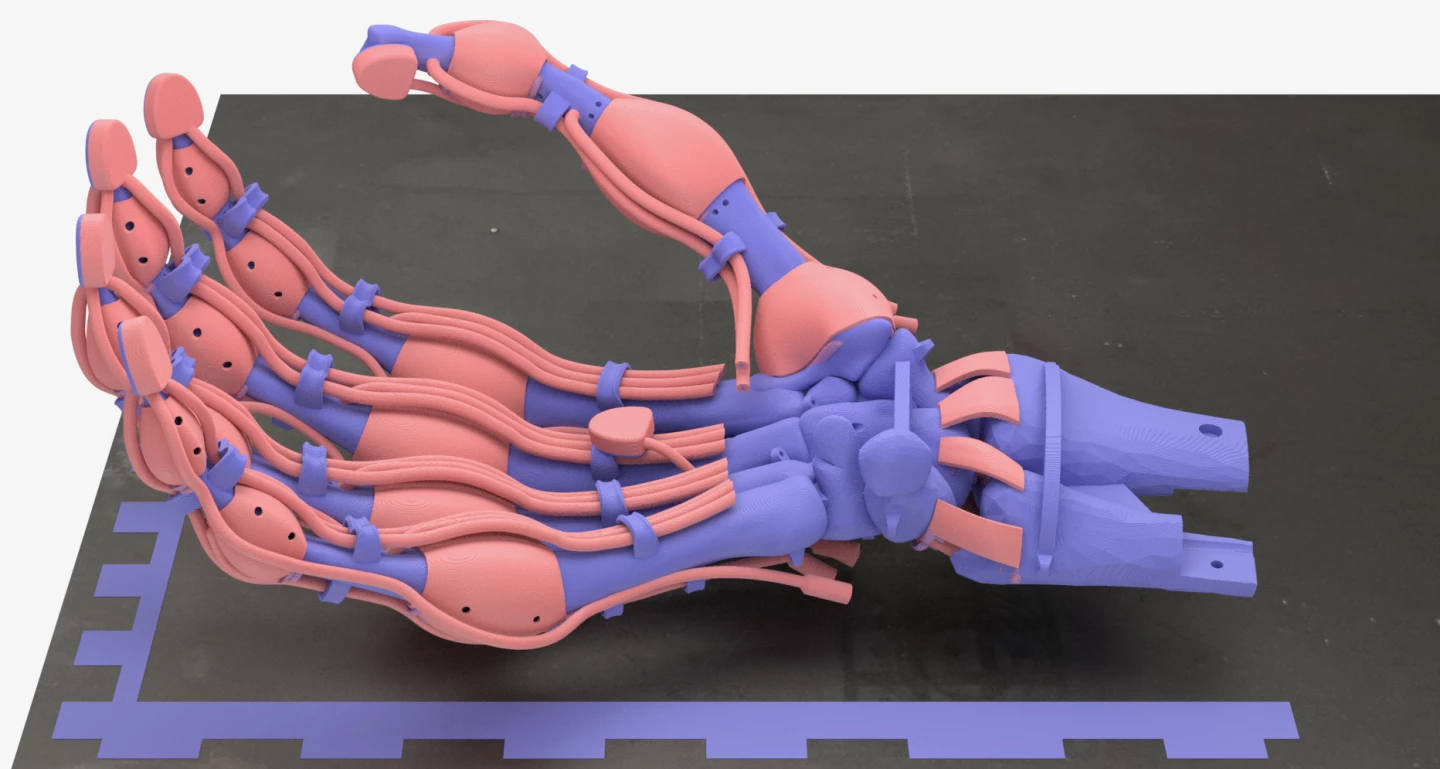
In a demonstration of the technology, it was utilized to print a highly detailed robotic hand complete with simulated bones, ligaments and tendons. It's important to note, the hand was built in one continuous print job, out of both rigid and elastic polymer resins that cured at different rates. No post-print assembly was required.
The Inkbit company – which is an MIT spinoff – is now accepting print jobs from commercial clients.
There's more information in the video below. A paper on the technology was recently published in the journal Nature.
Sources: ETH Zurich, MIT