Visitors to this year's Genoa Boat Show – which apparently is taking place in a physical venue – will see a rather unique watercraft. Made by Milan-based Moi Composites, the MAMBO is claimed to be the world's first "real" 3D-printed fiberglass boat.
Its name an acronym for Motor Additive Manufacturing BOat, the MAMBO was printed in several pieces via a process known as Continuous Fiber Manufacturing (CFM). This involved using two Kuka Quantec High Accuracy robots – in Milan and at the UK facilities of project partner Autodesk – which built the parts up by strategically depositing and UV-curing continuous fibers impregnated with thermosetting resin.
The completed sections were subsequently joined together and laminated in the shipyard of Italian catamaran manufacturer Catmarine.
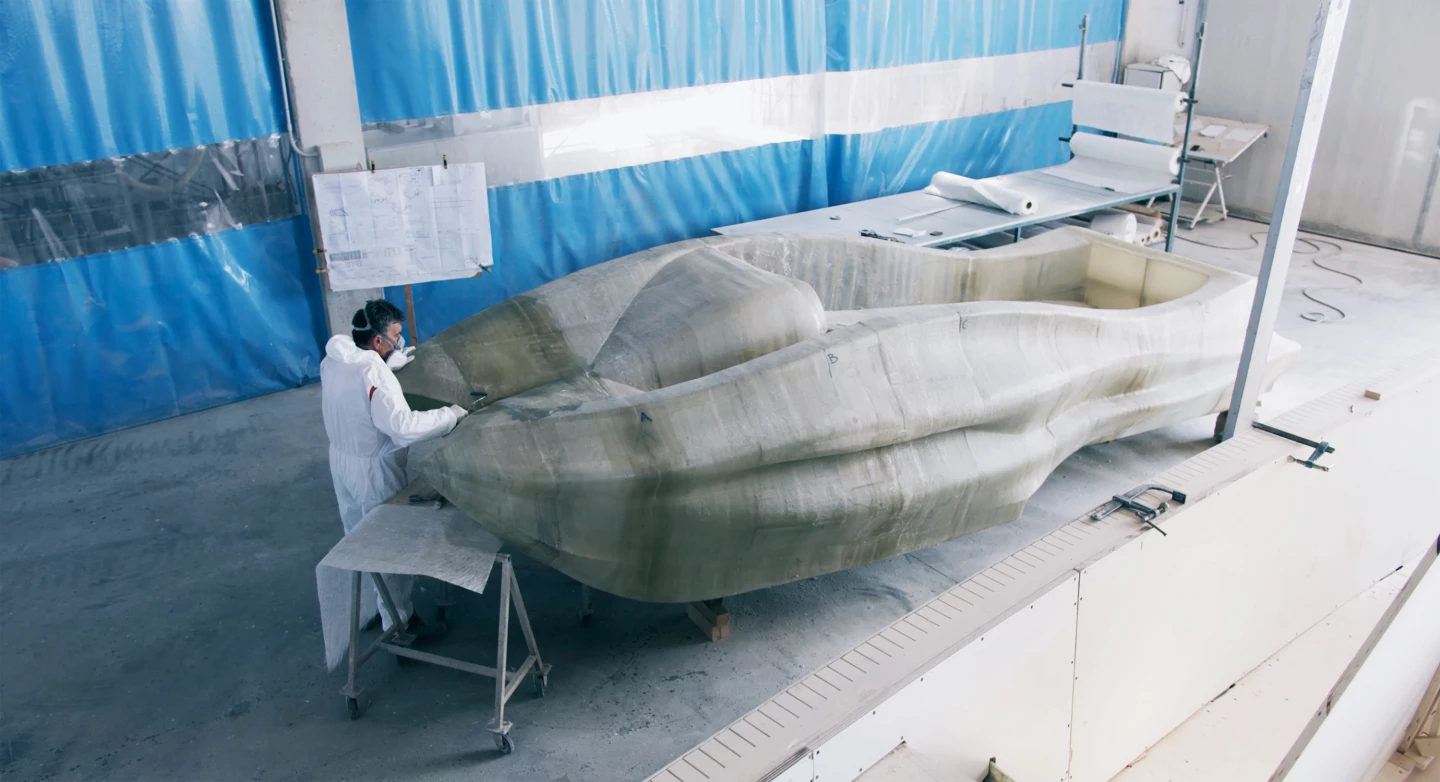
According to Moi, its printing system allows for the creation of products with mechanical characteristics similar to those of traditionally made unidirectional fiberglass, but without the need for molds or other tooling equipment. This reportedly means that fiber-reinforced prototypes or small-run production items can be manufactured relatively cheaply and easily.
Built as a one-off to promote the CFM technology, the finished MAMBO measures 6.5 meters long by 2.5 m wide (21.3 by 8.2 ft) and tips the scales at about 800 kg (1,764 lb). It's fully functional, incorporating a 115-metric horsepower motor, a navigation system, white leather seats and cork flooring.
The 2020 Genoa Boat Show runs until Oct. 6th at the Piazzale John Fitzgerald Kennedy in Genoa, Italy.
Source: Moi Composites