Researchers have come up with a 3D printing method using liquid metal that's claimed to produce structures at least 10 times faster than existing metal additive manufacturing processes, though it does so at the expense of fine detail.
The liquid metal printing (LMP) process was developed by a team that included Skylar Tibbits (co-director of MIT's Self-Assembly Lab, and associate professor in the Department of Architecture) and Zain Karsan (a PhD student at ETH Zurich), and was part-funded by the Aisin Group, Amada Global and furniture company Emeco.
Inspired by previous work with rubber, the research group first constructed a "bread-loaf-sized" electric furnace to heat up aluminum – a commonly used material in construction – beyond its melting point. The liquid metal is then held within the machine's graphite crucible before being gravity-fed through a ceramic nozzle.
"Molten aluminum will destroy just about everything in its path," said Karsan. "We started with stainless steel nozzles and then moved to titanium before we ended up with ceramic. But even ceramic nozzles can clog because the heating is not always entirely uniform in the nozzle tip."
The molten metal is extruded onto a predetermined path formed on a print bed of 100-micron glass beads, where it hardens to form a 3D structure without needing supports.
Unfortunately, though the technique proved faster than other additive manufacturing methods using metal, and can produce larger objects, it does so at relatively low resolutions – meaning that the aluminum chair frame pictured below ain't pretty, but is functional.
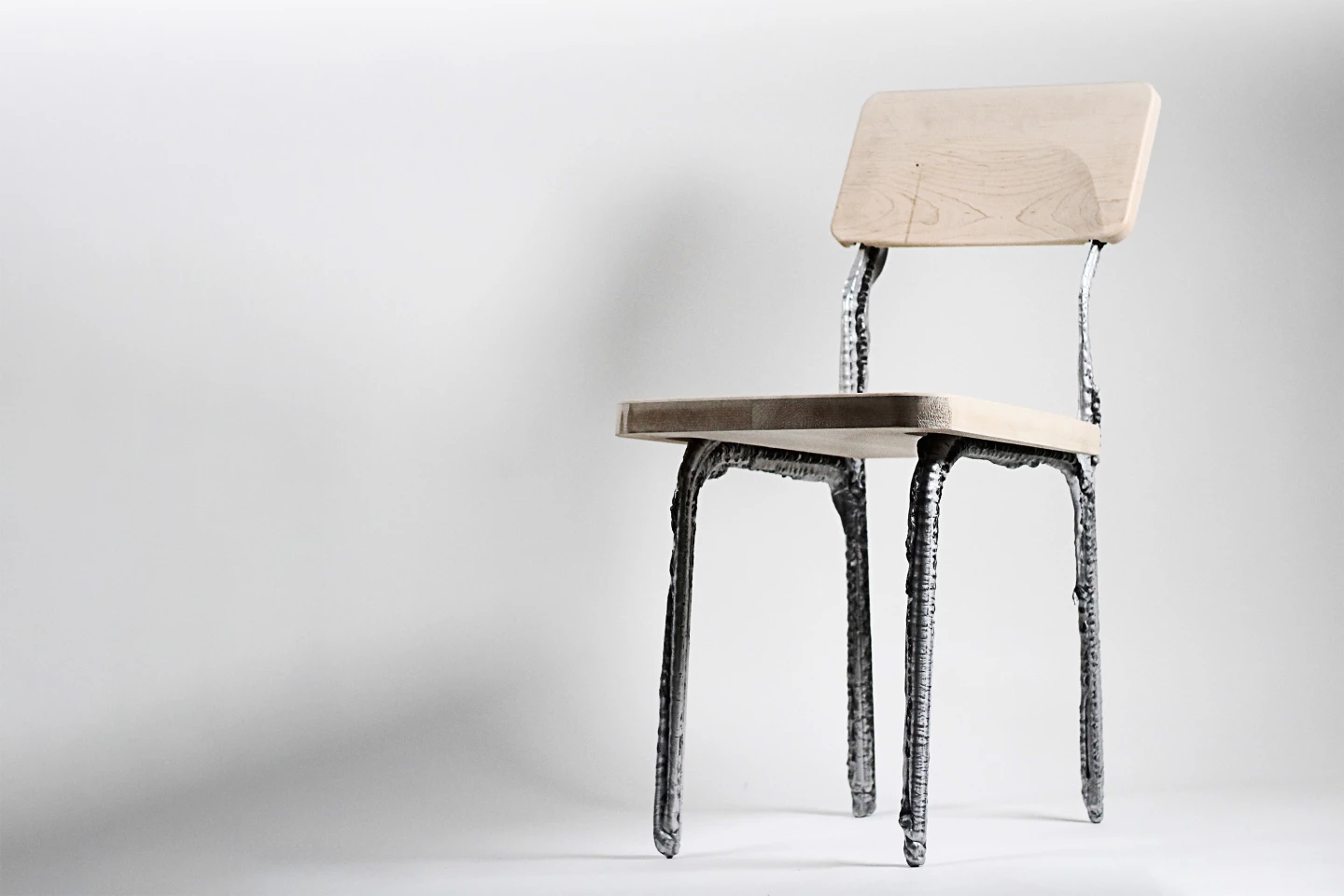
However, the team says that the development could not only make use of recycled or scrap metal, but could find use in construction and industrial design where high resolution is not a vital attribute. The printed material can also withstand post-machining like milling.
"This is a completely different direction in how we think about metal manufacturing that has some huge advantages," said Tibbits. "It has downsides, too. But most of our built world – the things around us like tables, chairs, and buildings – doesn’t need extremely high resolution. Speed and scale, and also repeatability and energy consumption, are all important metrics."
Another advantage over existing methods, such as wire arc additive manufacturing that's common in architecture projects, is that because the metal is molten throughout the printing process, it's less susceptible to cracking and warping.
The team plans to keep tweaking the process for improved flow control and more consistent nozzle temperatures to prevent clogging.
"If we could make this machine something that people could actually use to melt down recycled aluminum and print parts, that would be a game-changer in metal manufacturing," added Tibbits. "Right now, it is not reliable enough to do that, but that’s the goal."
The development is introduced in a paper that was recently presented at the Association for Computer Aided Design in Architecture Conference. The video below has more.
Source: MIT