Ordinarily, if you want to change the shape in which an object is 3D-printed, you have to alter the computer model that tells the printer what to do. A new and simpler technique, however, allows the printer to initiate the changes itself, as the print job is in progress.
The technique was developed at Illinois' Northwestern University, by a team led by Assoc. Prof. Cheng Sun.
It's applied to an existing type of 3D printing known as digital light processing (DLP), in which focused patterns of ultraviolet light are shone through the transparent sides of a vat of photosensitive resin – doing so causes select areas of the resin within to polymerize into layers of solid material. The first layer forms on a submerged build platform, which is incrementally raised so that successive layers can be added, one below the other. Finally, the platform is raised right out of the vat, with the completed 3D-printed object hanging beneath it.
Normally, the build platform rises straight up. In the new system, however, it's attached to a robotic arm which moves it not only vertically but also horizontally. Therefore, if the user wants to change the shape of an object in a given way – without changing the digital model – they can instruct the arm to gradually pivot or slide the platform in the appropriate direction(s), causing the build to skew accordingly. Additionally, unlike typical DLP systems, this one doesn't pause between layers. As a result, it can print 4,000 layers in about two minutes.
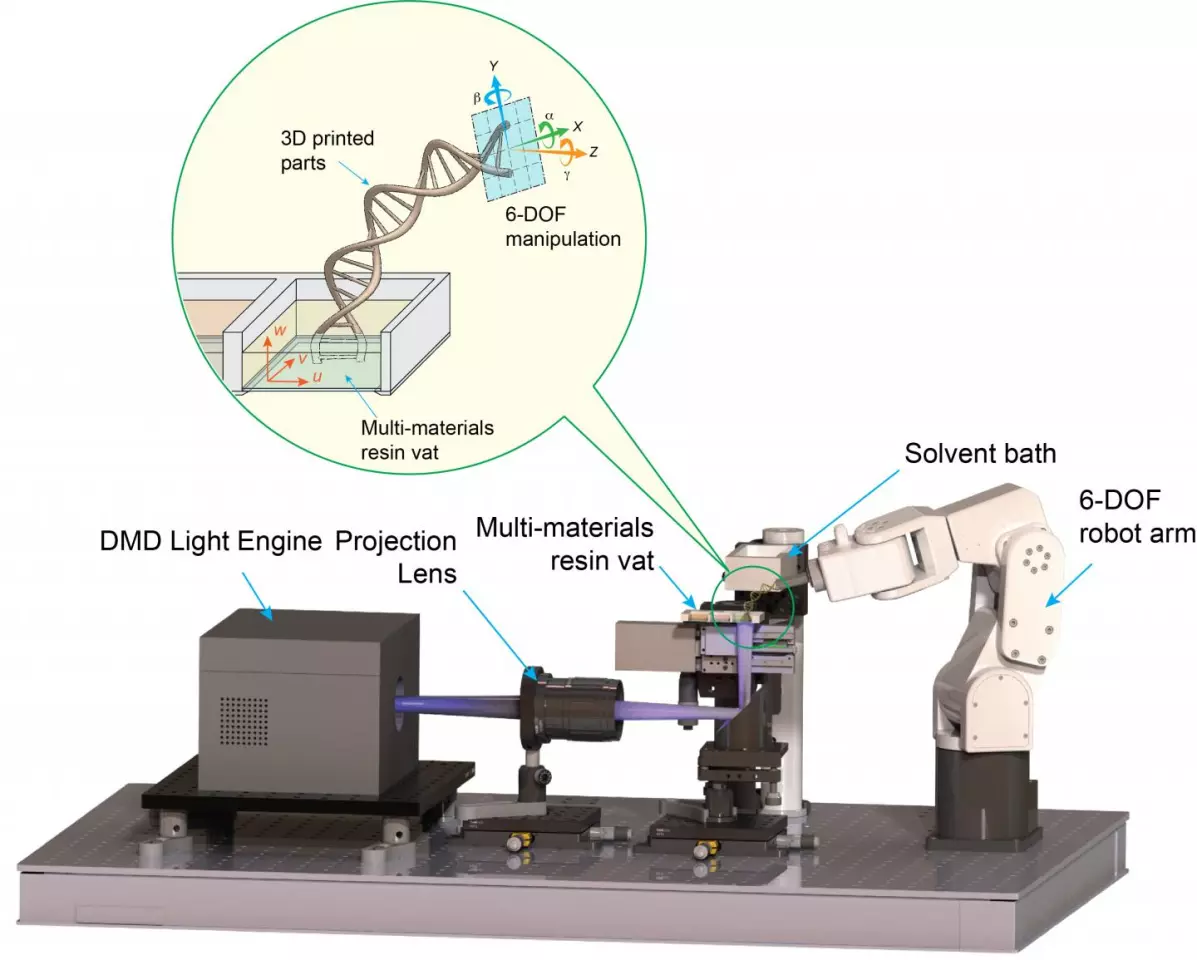
So far, the technique has been used to print items such as a customized vascular stent, a soft pneumatic gripper, a double helix, and a tiny twisted Eiffel Tower.
"The 3D printing process is no longer a way to merely make a replica of the designed model," says Sun. "Now we have a dynamic process that uses light to assemble all the layers but with a high degree of freedom to move each layer along the way."
A paper on the research was recently published in the journal Advanced Materials.
Source: Northwestern University