Ordinarily, the 3D printing of multi-colored, multi-textured objects is a relatively complex and inefficient process. That could soon change, however, thanks to a clever new technique in which a temperature-sensitive print media gets "ironed" after being extruded.
When most people think of a 3D-printed item, they probably picture an object that is all one color and texture. Such items are made by depositing successive layers of a single type of molten polymer that hardens as it cools.
In order to print a single object which is different colors or textures in different places, a multi-nozzle printer is typically used (although some alternatives are in the works). Its nozzles take turns throughout the printing process, each one depositing a different type of polymer to create a different part of the item.
A big drawback to this approach lies in the fact that as multi-nozzle 3D printers switch back and forth between nozzles, they end up wasting more print media than their single-nozzle counterparts. Additionally, there's no way of gradually transitioning between the different polymers within the printed object – the borders between the polymers are very abrupt, which isn't always desirable.
One proposed alternative involves using a single nozzle to deposit a single special polymer, which takes on different colors or textures depending on the temperature to which the nozzle heats it. The problem is, it takes a while for the nozzle to heat up or cool down, so the printing process will likewise be impractically lengthy.
That's where "speed-modulated ironing" comes in.
Developed by scientists from MIT and the Netherlands' Delft University of Technology, the process utilizes an unmodified two-nozzle 3D printer, along with a single polymer print media that contains a heat-sensitive active ingredient.
The first nozzle melts and deposits the polymer at a constant temperature, just like it normally would. The second nozzle doesn't deposit anything, and it also stays at a constant temperature, but it moves back and forth across the surface of the deposited polymer at varying speeds. The longer it lingers in one area, the hotter that area gets, and the greater the active ingredient's response.
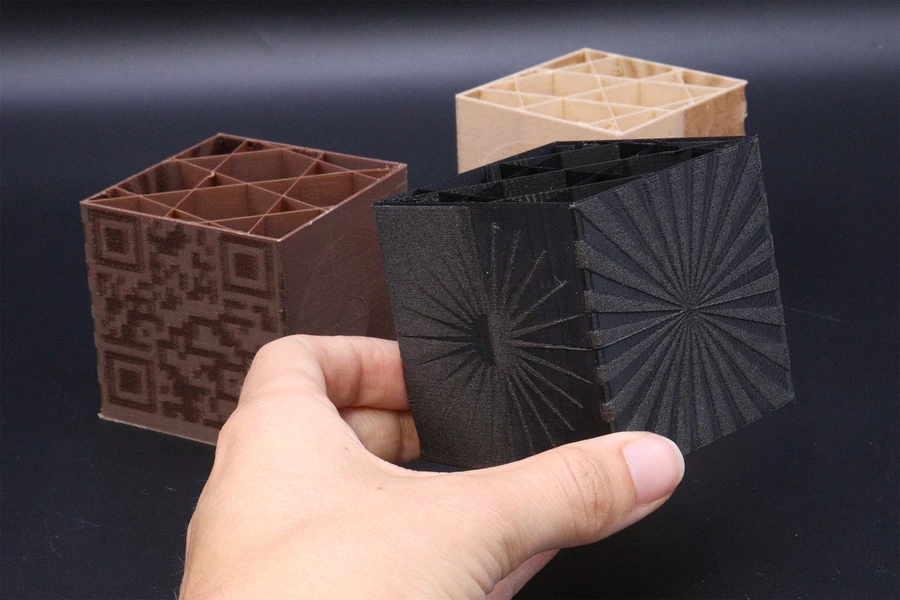
The technology has already been tested with three types of print media.
One contained particles that foamed when heated, causing the printed polymer to vary between appearing opaque or translucent, and feeling rough or smooth. Among other things, this material was used to print water bottles with opaque graphics set against a translucent background, along with bicycle handlebar grips that were smooth in some areas and rough in others.
The other two media contained wood and cork fibers, both of which caused the polymer to take on a darker color as they charred when heated.
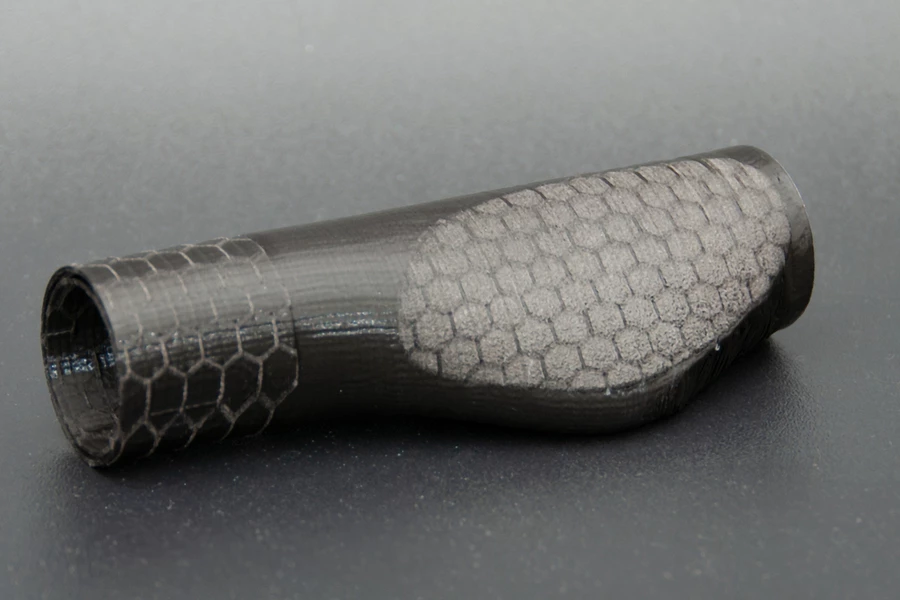
The scientists have already created computer models that determine how fast the second nozzle should move throughout the print process, in order to get the desired effects using a specific print media. They're now looking into using the technology to vary a single printed object's acoustic and mechanical properties.
A paper on the research – which was led by MIT's Prof. Stefanie Mueller and Delft's Asst. Prof. Zjenja Doubrovski – is available to read online. The speed-modulated ironing process is demonstrated in the following video.
Source: MIT