Ordinarily, airliners have to run their jet engines in order to taxi along the runway – this uses a lot of fuel, plus it generates a lot of carbon emissions. A new in-ground electrical towing system, however, offers what could be a much more efficient and eco-friendly alternative.
Known as the Aircraft Towing System (ATS), the technology is currently being developed by Oklahoma-based firm ATS World Wide.
The system incorporates long trench-like channels that are installed length-wise down the middle of existing taxiways and aprons (or built into new ones) and then covered with two steel plates, one on each side. There's a 1.5-inch (38-mm) gap between those plates, creating a slot which runs the entire length of each channel. That gap is covered with a split rubber gasket, in order to keep foreign objects from falling through.
Contained within each channel is a motorized monorail device called a pullcar, which is powered by electrical rails running along the sides of the channel. Via the slot between the plates, the top of the pullcar is attached to another device called the tow dolly, which sits exposed on the surface of the runway.
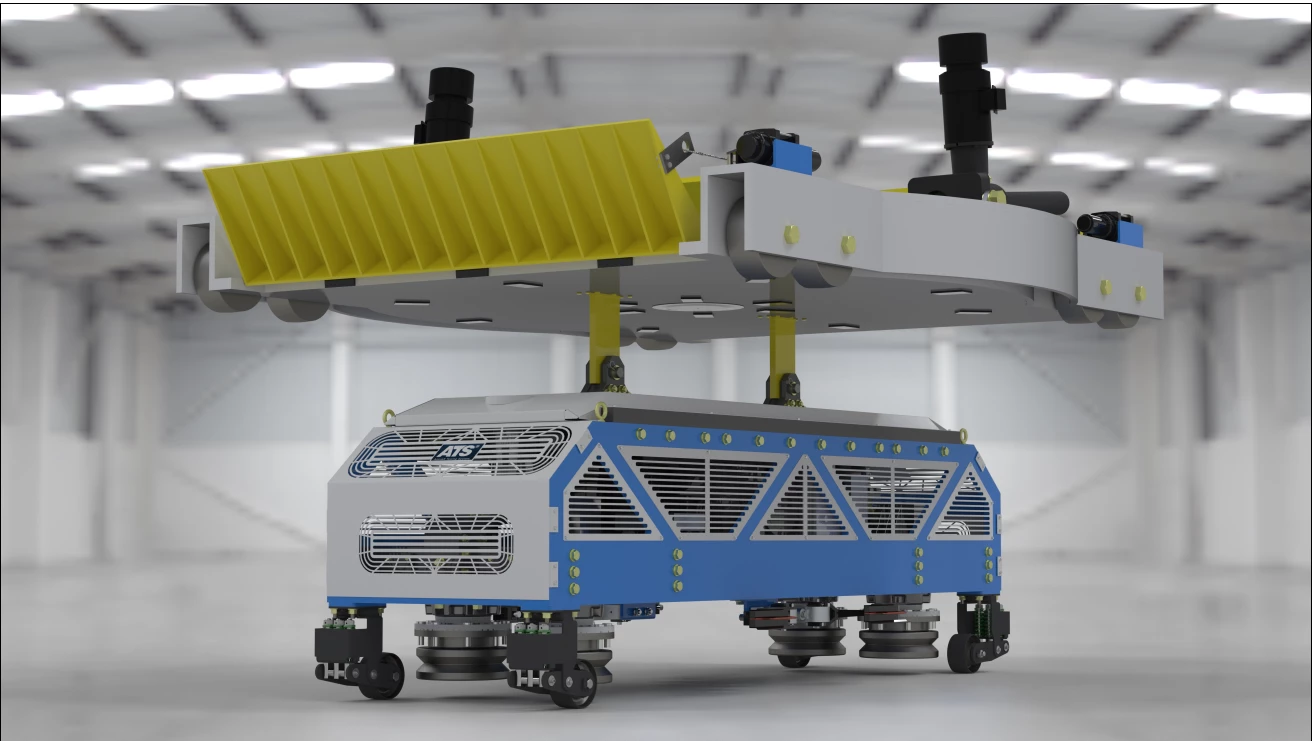
Most of the time, each pullcar/dolly unit sits out of the way. Once an airliner has landed or is ready to depart, though, the unit moves up to the aircraft's front wheels. The pilot then runs the plane's engines just long enough to move the wheels onto the dolly.
Chocks on the dolly subsequently rise up to hold the wheel in place, and the pullcar kicks in to push or pull the aircraft along the tarmac as needed. Once the plane has been towed to where it needs to be, the engines are run once again to move the wheels back off the dolly. In cold climates, heating elements in the channels are used to keep the slots from icing over or getting clogged with snow.
The whole system is automated, so pilots don't need to steer their aircraft along the tarmac, nor do control tower staff need to remotely control the pullcars. This should minimize the chances of planes colliding with one another on the ground, or simply getting in one another's way. In fact, researchers at Oklahoma State University have reportedly calculated that use of the system could increase aircraft throughput at airports by up to 30 percent.
That said, ATS can be manually overridden if necessary. Because the wheel chocks on the dolly are ramped, the wheels can run up and over them if the plane's engines are used.
"Right now when an aircraft comes in, it's typically handed off between four different people between the time it touches the ground and it gets to the gate," ATS World Wide CEO Vince Howie tells us. "And 80 percent of the time, the pilot's driving the aircraft on his own, without any directions. We're going to take that system, and totally automate and optimize it."
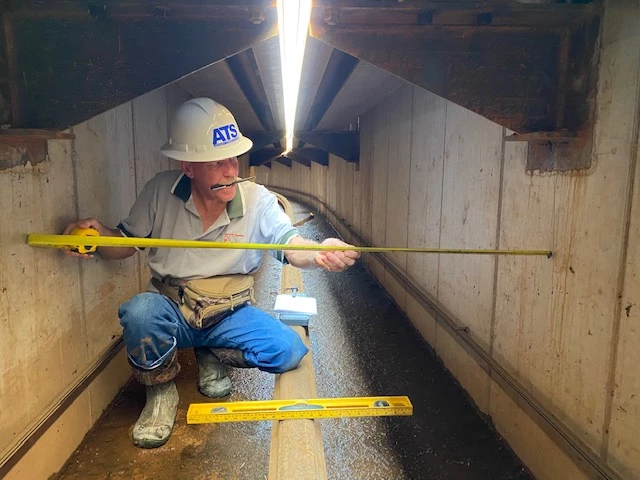
Because the system is modular, airports that are on a budget could initially opt for just the pushback sections, which are used to push or pull planes out from the departure gate and onto the runway. Currently, fuel-burning, human-driven pushback tractors are utilized for this task. ATS is presently finishing up a 358-ft (109-m) prototype pushback channel at Oklahoma's Ardmore Municipal Airport, which we're told should be operational within three to four weeks.
It should be noted that the system does face some competition, mainly in the form of airliners with motorized front wheels, and an unmanned electric towing tractor known as the TaxiBot. The former requires modifications to be made to aircraft, however, plus it makes them heavier and thus less fuel-efficient when flying. The latter, on the other hand, needs to have its batteries recharged once every several hours, and may obstruct runway traffic on its way back from taking planes out for takeoff.
Since a complete ATS setup would cost about US$150 million, airports would definitely require a means of recouping those costs. Howie suggests that such airports could charge a landing fee to airlines, which would be equivalent to about 50 percent of the cost of the fuel each aircraft would save by using the system. Additionally, the airports could sell their carbon credits to other companies. All told, he believes that operators should see a return on their investment within just two years.
"Eighty percent of the commercial fleets are 737s or A320s," says Howie. "They burn about nine gallons (34 L) of fuel per minute during taxi. The average taxi time in the US is between 16 and 27 minutes. At large airports, you'll have over 800,000 movements per year. So if you take that nine gallons of fuel, times 16 minutes, times 800,000, times whatever the price of fuel is of the day, it turns into real money really quickly."
You can see an animated demo of ATS in action, in the following video.
Company website: ATS