A self-propagating series of explosions, contained between the blades of a high-speed rotor, promises a leap in power and efficiency during hypersonic flight – provided this radical new engine can be built strong enough to withstand its own power.
Since the dawn of flight, people have been chasing the fastest of go-fast propulsion systems – and it's worth taking a look back over some of that history to put this latest invention in context. Skip ahead if you want to dive straight into the new ram-rotor detonation engine!
First came the failed flappy wings of da Vinci's ornithopters, inspired directly by birds. Soon after came propellers, which got the Wright Brothers off the ground using constant thrust from spinning blades that could be connected to an engine. Propellers remained the state of the art right up until WW2.
In 1939, the first jet-powered aircraft, the Heinkel He 178, took to the skies, switching things up by using its own expelled exhaust gases to create thrust. In 1941, the first turbojet flew in the Gloster E.28/39, adding a turbine-driven compressor to force more air into the combustion chamber for additional power and efficiency.
In 1949 we saw the first aircraft, the Leduc 0.10, to fly entirely powered by a ramjet, which also directed compressed air into the engine – but this time compressed entirely by the aircraft's own high-speed forward motion, and an intake shape designed to slow that air way down. The infamous Lockheed D-21 drone of the mid-1960s was essentially a ramjet with wings and thus, incapable of taking off under its own power. It had to be launched from the back of a Lockheed M-21 (not to be confused with the SR-71) once it was traveling at supersonic speeds, allowing the ramjet to function properly.
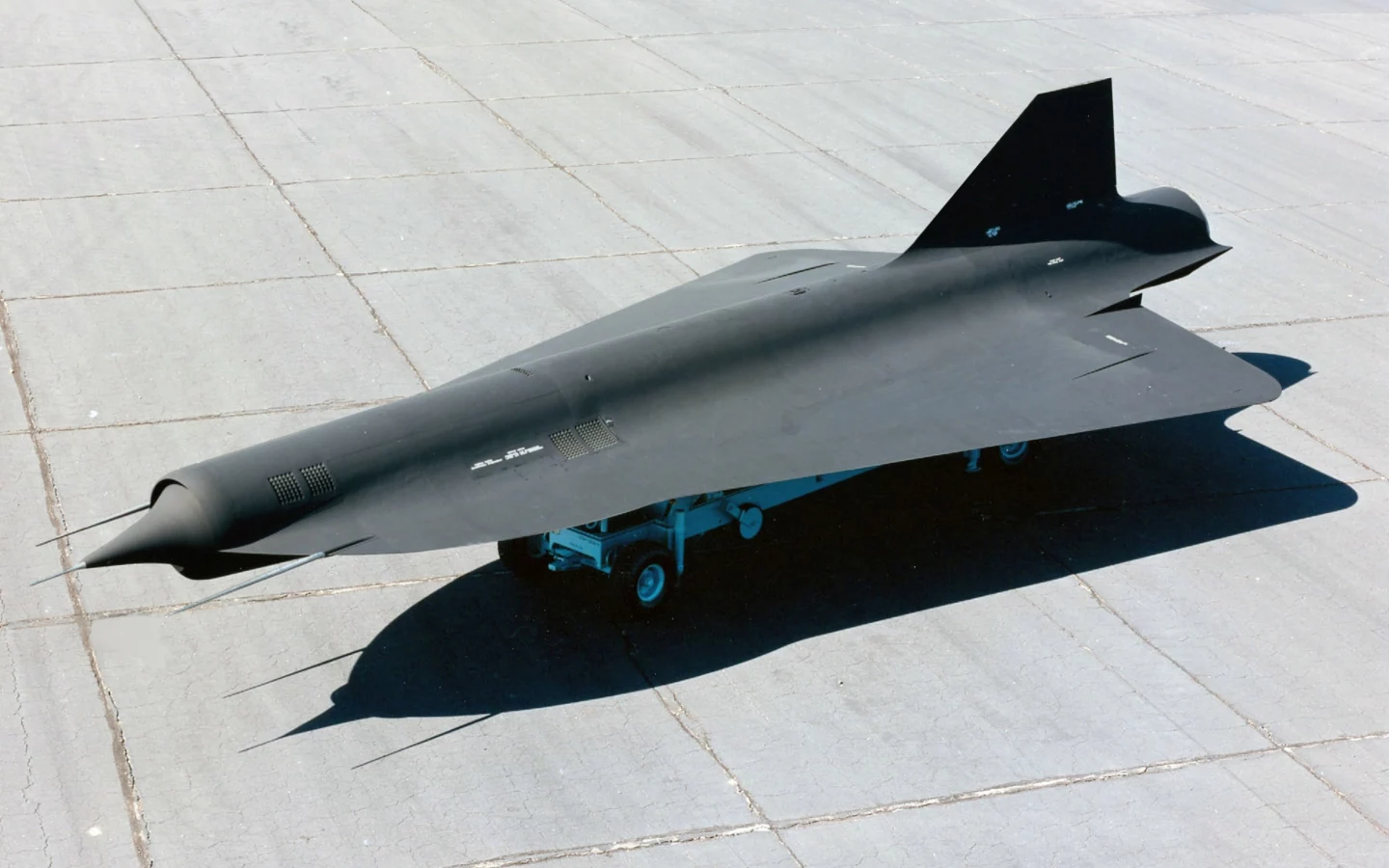
The 1950s was a highly innovative time for aerospace, and plenty of what we still use in go-fast flight today was born in this era. We saw the first production turbofan engine by Rolls-Royce, called the Conway, in 1954. Turbofans divert some airflow around the core of a turbojet engine, speeding it up with a large fan, and then mix this bypass air with the jet exhaust.
You can adjust the ratio of these two flows; a high bypass ratio is great when you want an engine that's quiet and efficient, a low ratio works when you're prioritizing speed and agility. Nearly every commercial passenger airliner today uses high-bypass turbofan engines.
In 1958, the scramjet, or supersonic combustion ramjet, was conceptualized – which would ignite fuel in a combustion chamber while air flowed through continuously at supersonic speeds, eliminating the ramjet's draggy need to slow that airflow down below the speed of sound. But this design wasn't successfully put to the test until 2001 in NASA's X-43A – whereupon it hit an impressive hypersonic speed of Mach 6.8 (5,217 mph or 8,396 km/h) – then three years later, Mach 9.6 (7,366 mph or 11,854 km/h).
Rotating detonation engines
In 2020, we saw the first of an "impossible" new breed of rotating detonation engines (RDEs) fire up on a test bench. These machines leave the slow, controllable world of combustion behind, and instead literally attempt to harness the intense, chaotic energy released in actual explosions.
This is not the nice, predictable oxidation of an air-fuel mix by flame, it's literally hitting explosive fuel molecules hard enough with a shockwave to break apart their chemical bonds, causing them to detonate and release another shockwave. The genius of the RDE is in sending the energy of that shockwave around a ring-shaped channel, and timing the release of more explosive fuel to create a self-sustaining pattern of explosions.
The benefit: a theoretical efficiency boost up to 25% over regular combustion engines. One drawback: they work much less efficiently at atmospheric pressures, so they're much happier at supersonic or hypersonic speeds where intake air can easily be compressed to keep conditions ideal for detonation.
2024: Enter the ram-rotor detonation engine (RRDE) concept
Dr. Haocheng Wen and Prof. Bing Wang of Tsinghua University in Beijing, China, have conceptualized a revolutionary new type of engine they say could improve the efficiency of rotating detonation engines across a wide range of airspeeds.
Essentially, it's a rotating detonation engine in which the detonation wave is stabilized within a high-speed rotor. A precisely shaped flow channel within the rotor compresses the air-fuel mixture to the ideal conditions for detonation, whatever the intake speed, and the detonation wave is held in place by balancing the relative velocities of intake airflow and the expanding gases and shockwave leaving the exhaust.
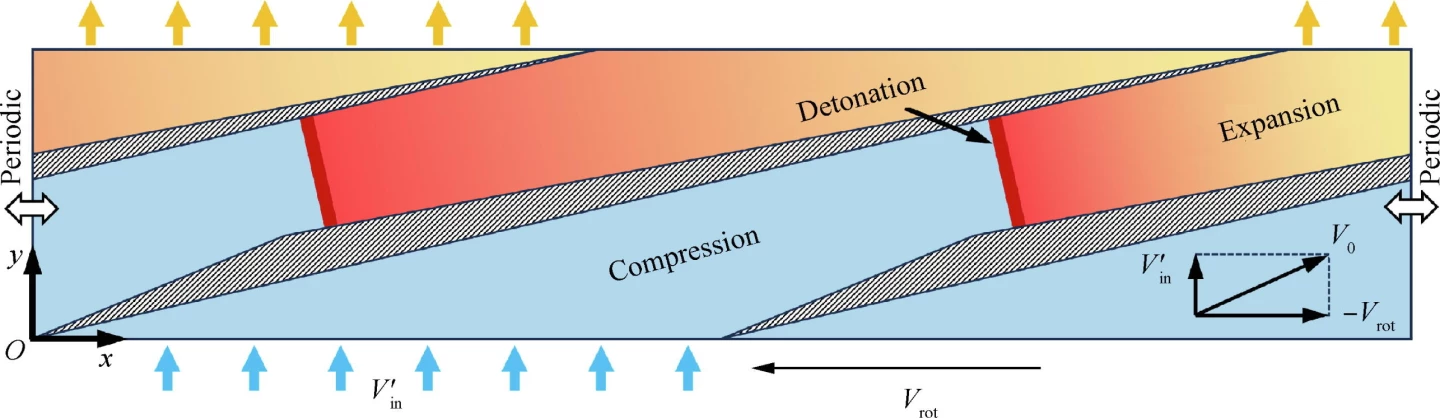
So the ram-rotor controls reactant compression, the detonation point, and burned gas expansion within that single rotor. And it uses a continuous supersonic rotating detonation wave as its primary means of propulsion, which is inherently more efficient than traditional deflagration methods. The RRDE achieves higher thermodynamic efficiency by capitalizing on the extreme pressures and temperatures of detonation in a way no traditional ramjet engine can.
So far, the RRDE exists only as a design, and has proven itself only in theoretical and simulated lab tests. Theoretical tests say that this beast of an engine should be capable of hypersonic flight over Mach 5+ (3,836 mph / 6,174 km/h), at considerably higher efficiency than other detonation engines – and the air-compressing ram-rotor should also be able to generate the right conditions for detonation at speeds substantially slower than regular RDEs.
This doesn't mean a ram-rotor detonation engine-powered aircraft will necessarily be able to take off under its own power, but it does herald a significant step in detonation engine technology.
Of course, challenges remain. Driving that ram rotor requires energy, and that's going to impact efficiency. Sustaining a detonation wave is hard enough in a static ring channel, so keeping one stable in a high-speed rotor won't be a walk in the park. And of course, the rotor blades will need to be light enough to spin quickly and efficiently, but strong enough to handle hypersonic intake airflows ... As well as constant explosive detonations between the blades. Yikes.
We hope it's a lot quicker to go from the drawing board to a test aircraft than some previous advances, but the recent acceleration in hypersonic research, particularly out of China, would suggest it'll have a chance to prove itself before long.
Source: Chinese Journal of Aeronautics