Liquid cooling is one of the most effective ways to keep computers from overheating. While the natural first choice might be a liquid that runs cold, Microsoft has now done the exact opposite, demonstrating a system to cool its cloud servers by dunking the computers into a tank full of boiling liquid.
Electronics produce heat as they work, which can lead to failure if it gets out of hand. In data centers that can become a huge problem, requiring around-the-clock air conditioning that in turn makes these facilities massive guzzlers of energy. To counter that, companies have started building data centers in the Arctic circle, under the sea, or beneath Norwegian fjords.
Now Microsoft has shown off a clever new technique, which it calls a two-phase liquid immersion cooling system. The electronics are actually immersed in a vat of liquid, which wicks away the heat they produce while running. This liquid has a low boiling point of just 50 °C (122 °F), so it doesn’t take long for it to bubble away. As it evaporates, the vapor hits a cooled condenser in the lid of the tank and rains back down, creating a closed loop.
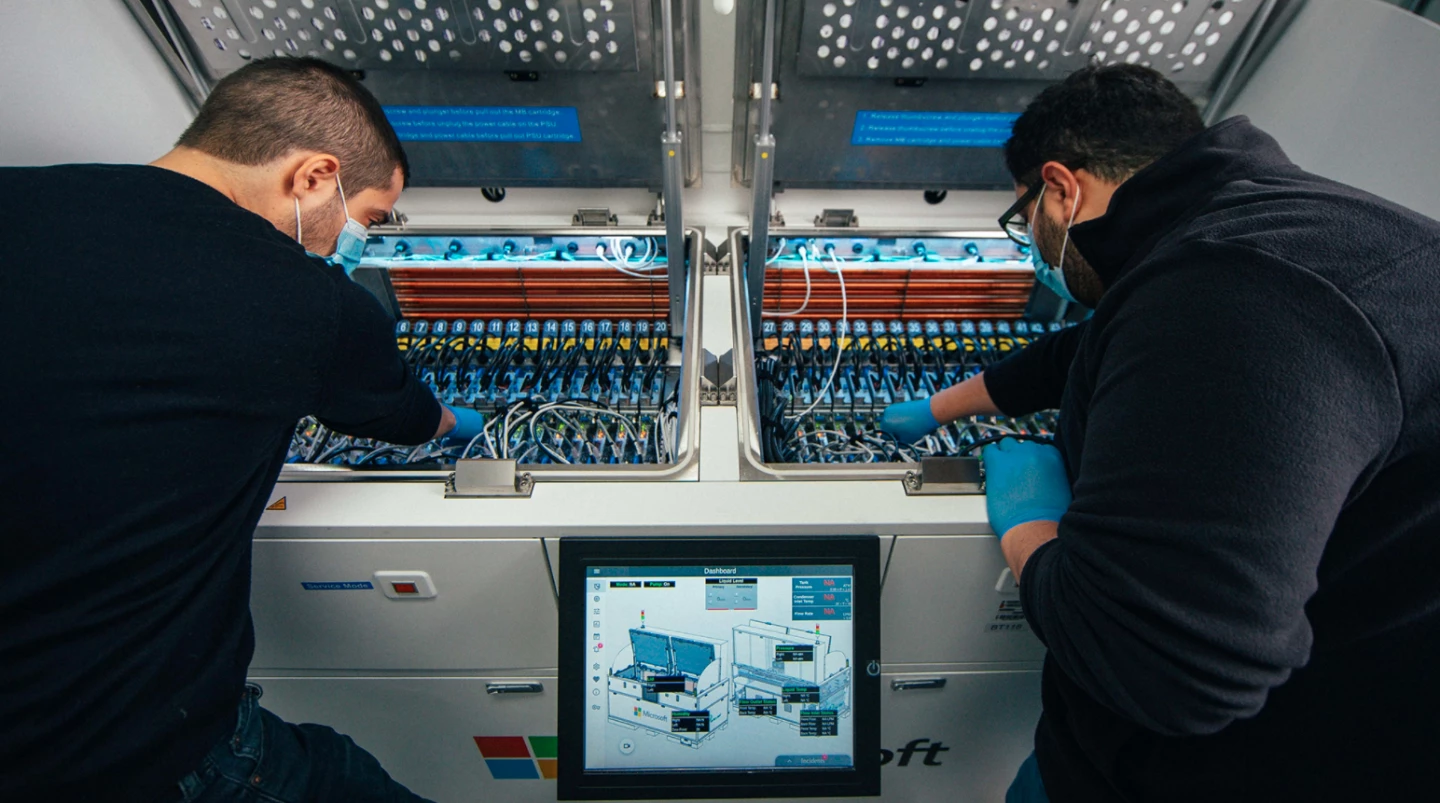
The liquid itself is a strange concoction specially designed for this task to have a low boiling point. It’s also “dielectric,” meaning it acts like an insulator so it won’t short out the electronics while they’re running.
Microsoft says that this technique has a few advantages. It should reduce failure rates of individual components and allow them to be overclocked without risk of overheating. And with that risk removed, the chips could also be crammed in more densely to improve latency and performance.
For now, the company is running one test in a data center in Redmond, Washington, where it will monitor the results over the next few months. If it all goes well, Microsoft says it might end up in more of its facilities.
Source: Microsoft