When a cotton gin is used to separate cotton fibers from their seeds, a lot of lint is produced as a waste product. Currently, much of that cotton lint is just burned or put in landfills. Thanks to recent research out of Australia, however, it may soon be converted into biodegradable plastic.
According to Deakin University's Dr. Maryam Naebe, approximately 29 million tonnes (32 million US tons) of cotton lint is produced annually, with about one third of that simply being discarded. Members of her team wanted to reduce that waste, while also offering cotton farmers an additional source of income, and producing a "sustainable alternative to harmful synthetic plastics."
This prompted them to develop a system in which inexpensive environmentally-friendly chemicals are used to dissolve lint fibers, along with other ginning trash such as seeds and stems. The resulting liquid organic polymer is then used to create a plastic film, samples of which are pictured below (surrounding a pile of cotton waste).
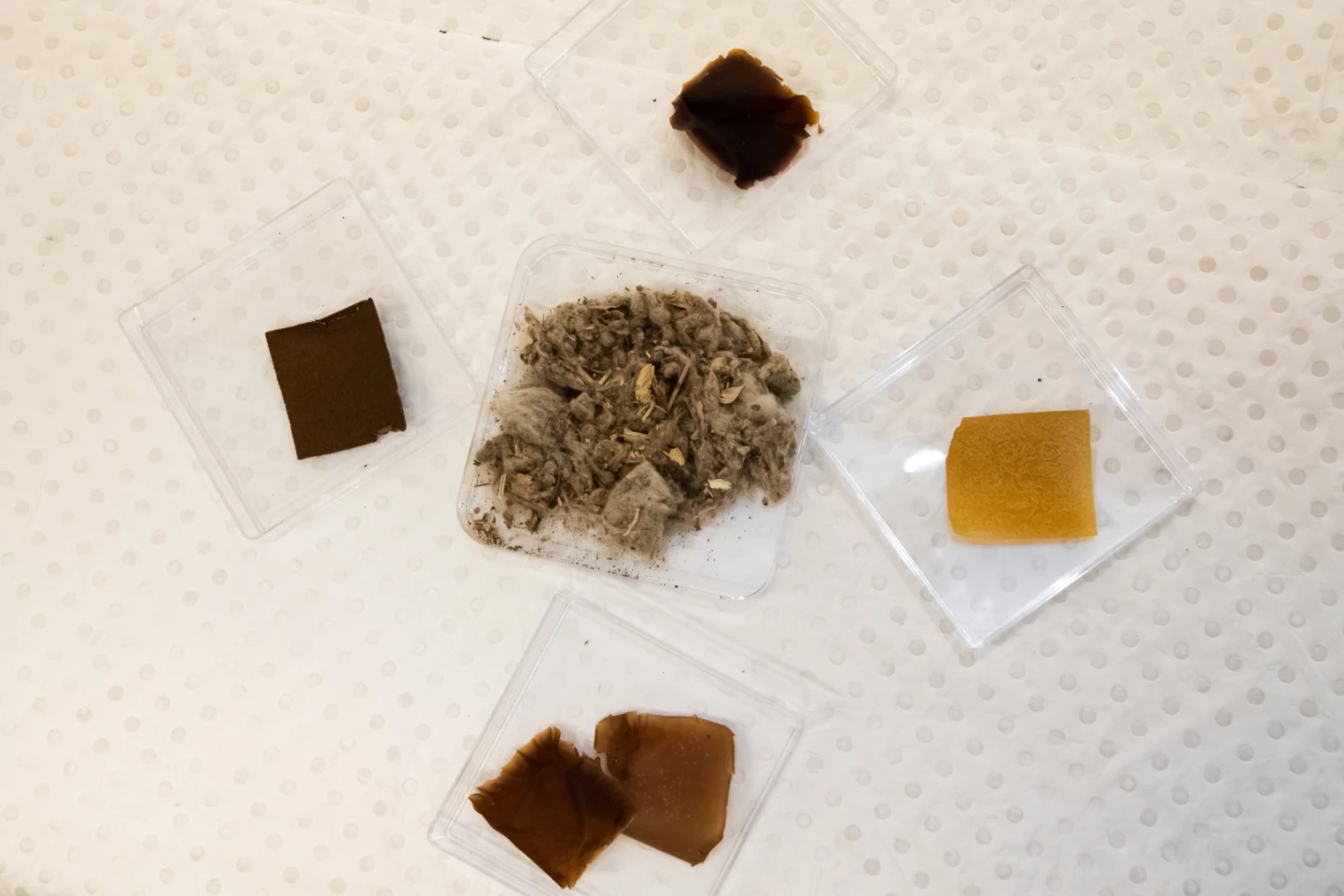
That material harmlessly biodegrades after being placed in the earth, and could conceivably be used within the cotton-farming industry, for applications such as bale wrap or packaging for seeds and fertilizer. It may even become one part of a full-cycle agricultural process.
"The bioplastic can biodegrade and turn into soil, which will then in turn be used to grow cotton, resulting in cotton gin trash during the ginning process, which can then be repurposed again into bioplastic," says Naebe.
And as an added benefit, the plastic film is reportedly less costly to manufacture than similar petroleum-based products.
The research is part of a project led by PhD candidate Abu Naser Md Ahsanul Haque and associate research fellow Dr. Rechana Remadevi. They are now looking into applying the same technology to organic waste and plant material such as lemongrass, hemp, almond shells, wheat straw, wood saw dust, and wood shavings.
Scientists from the National University of Singapore have also recently found a use for cotton waste, by converting it into an insulating and absorbent aerogel.
Source: Deakin University