Israeli company H2Pro claims its highly efficient water-splitting technology will deliver green hydrogen at less than US$1 per kilogram before 2030. That's a big deal; it would represent a 60-80 percent drop in green H2 prices, down to a level where it's cheaper per unit of energy than current retail gasoline prices in the United States. The Hydrogen Council's current projections don't expect that kind of price drop until 2050, and even then it's a best-case scenario.
Assuming distribution can be ramped up pronto, and assuming a carbon price of US$100 per ton of CO2 equivalent, it could immediately make hydrogen cost-competitive across a range of applications, from buses, trucks, trains and cars to replacing coal in steel production and natural gas in ammonia production and refinery use. Even without a carbon tax, it'd still be a terrific option to replace diesel in road and rail transport.
Some serious players are getting on board as H2Pro moves from the test bench into production – Bill Gates's Breakthrough Ventures, Hong Kong billionaire Li Ka-Shing, Hyundai motor company, Sumimoto Corporation – although the recent fundraising round total of US$22 million looks more like a toe dipped in the bath than a plunge into the water, a rather cautious approach given the company's claims. The devil's in the detail with these things, so let's have a closer look.
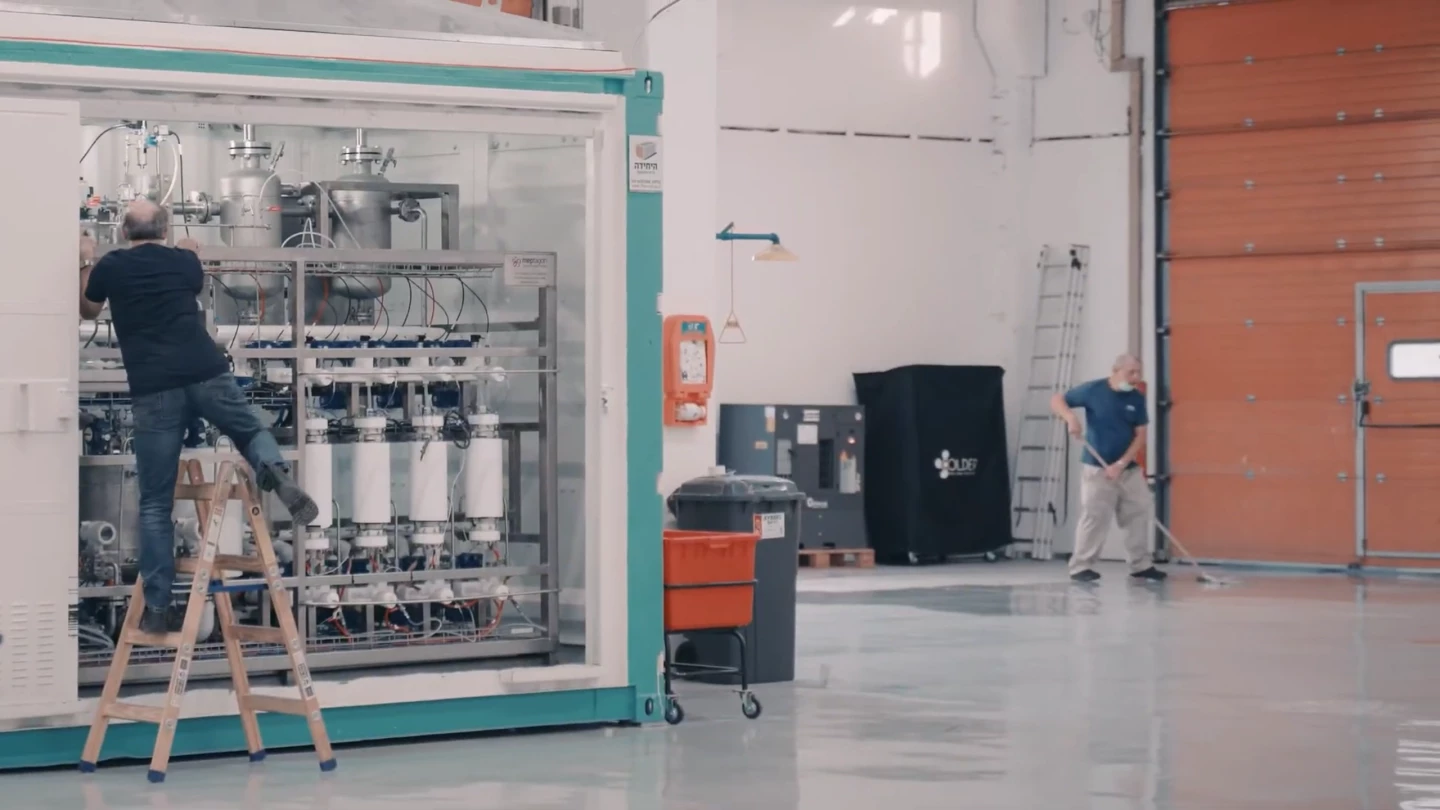
What exactly is the promise here?
In a promotional video, H2Pro says its E-TAC water splitting process is "the first technology to deliver energy efficiency of 95 percent ... compared to 70 percent of water electrolysis." The E-TAC devices, it says, are "inexpensive ... scalable, safer, and operate at higher pressure ... By 2023, we will deliver hydrogen at under US$2 per kilogram, and later this decade, at under US$1." A press release further clarifies: "coupled with anticipated reductions in the cost of renewable energy, H2Pro's technology will enable $1/kg green hydrogen at scale – making it the world's lowest cost green hydrogen."
The cheapest green hydrogen on the planet: that would be massive. Currently, it's already possible to produce "gray" or dirty hydrogen for US$1-1.80 per kilogram through steam reforming using natural gas – a process that emits CO2. H2Pro, on the other hand, is a water-splitting technology, so its emissions impact will depend on what energy source is used to produce it. Getting to US$1/kg with green energy would make this nothing less than a revolutionary technology in the long uphill climb towards zero global emissions.
The other part of the equation is also significant. A kilogram of hydrogen stores somewhere between 33 and 39 kWh of energy, depending on who you ask. In a paper published in Nature Science, H2Pro claims its E-TAC process produced gaseous hydrogen at an efficiency rate of 39.9 kWh per kilogram, where today's electrolyzers consume as much as 48 kWh per kilogram.
Now, this was a laboratory bench test producing tiny amounts of hydrogen, but that efficiency jump, and a promised full-system efficiency of 95 percent, is certainly something to celebrate. One of the key knocks on hydrogen as an energy storage medium is the many inefficiencies in its usage cycle; typically, you lose around 30 percent of your hard-won renewable input energy the minute you split your water. Reducing that to 5 percent would make green energy go significantly further, even if the fuel cells that extract energy back out of the hydrogen at the end use side are still quite inefficient.
How does the E-TAC process differ from traditional hydrolysis?
Effectively, by adding an extra step. Current-gen electrolysis produces hydrogen and oxygen at the same time, passing electricity through alkaline- or acid-enriched water to generate oxygen gas that's attracted to the anode and hydrogen has that's attracted to the cathode. This operation is performed in a chamber that's physically split with some sort of membrane, allowing each gas to be collected separately.
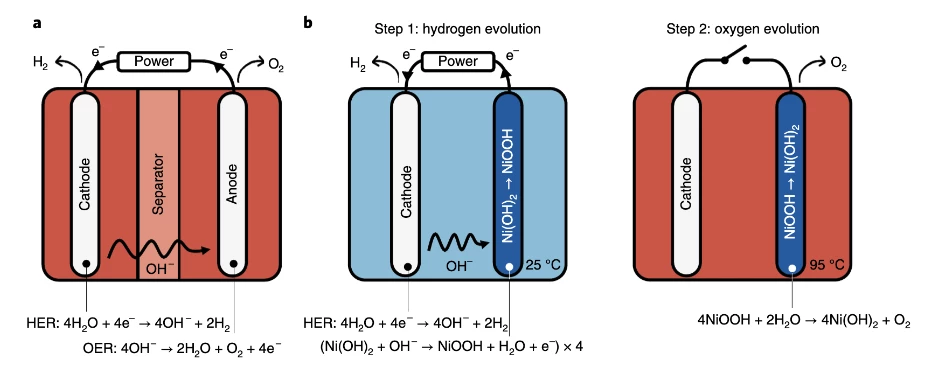
E-TAC, which stands for Electrochemical - Thermally-Activated Chemical water splitting, was originally developed at the Israel Institute of technology. The process generates hydrogen and oxygen in two separate processes. In the first (electrochemical) step, a current is passed through water at 25°C, evolving H2 which can be collected near the cathode, and hydroxide ions (OH-) that are attracted to the nickel hydroxide anode (Ni(OH)2). This oxidizes the anode, into nickel oxyhydroxide (NiOOH).
The second (thermally activated chamical) step disconnects the electrical circuit and heats up the water to 95°C, the optimal point at which that nickel oxyhydroxide anode reacts spontaneously with water to release the oxygen it gained in the first step, turning the anode back into nickel hydroxide and setting it up for another cycle. Additives to the water, including some cobalt, help ensure no unwanted oxygen is produced in the first step, and the all-important anodes are prepared by electrochemical impregnation of nickel foam substrates instead of being pasted or sintered, to maximize their surface area. This helps them handle higher current densities in the first step, and maximizes the regeneration rate in the second step.
The hydrogen and oxygen gases never mix, so the separation membrane – which H2Pro says is the most expensive and delicate part of a traditional electrolyzer – isn't needed at all, and the risk of explosive gas mixing is eliminated. The E-TAC system, unlike membrane systems, can support high-pressure production, up to 100 bar, meaning that you don't need to spend more money on compressors, and that plus the lack of membrane helps reduce capital, operational and maintenance costs.
It's also well-suited for use with renewable power sources like solar and wind, since it's capable at operating efficiently at partial loads; these renewables vary constantly in their output and rarely run at 100 percent capacity.
Where to from here?
H2Pro says the US$22 million investment round "will be used to support ongoing development of the technology and scale up H2Pro's manufacturing capabilities." In a production system, the E-TAC process could be set up in a multi-cell system, where the room-temperature stage 1 electrolyte and the hot stage 2 electrolyte are kept separate and "pushed around" through the various circuits by a third fluid at an intermediate temperature. In this way, you could have the first and second steps happening concurrently in separate, hermetically-sealed circuits.
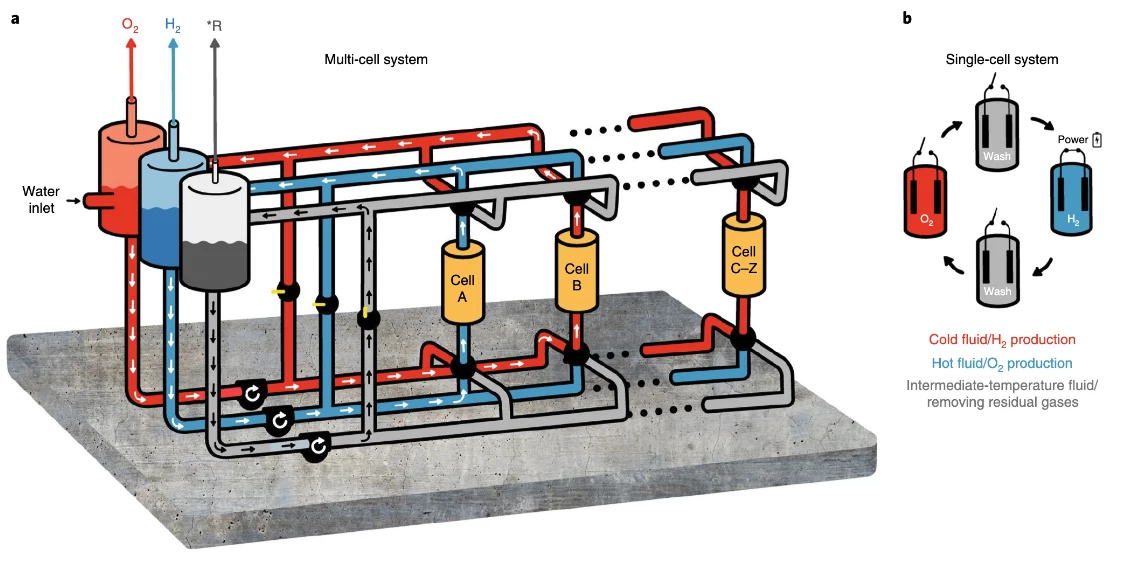
Smaller, slower implementations could use a single-cell system, in which the cell is "washed" between stages by a similar intermediate-temperature fluid. Either way, the electrodes will stay stationary and the fluids will move, and the electrolyte heat can be carefully managed for efficiency, taking advantage of the endothermic process in the first step and the exothermic process in the second step to minimize heat losses and thus energy costs.
The lab prototype, according to Bloomberg, can produce about 100 grams of hydrogen a day, with the researchers manually connecting and disconnecting the circuit between steps. The company expects to have a 1kg/day prototype in operation. It's an awfully long way from 1kg/day up to commercial-scale hydrogen generation, and the graveyards of capitalism are littered with companies whose tech broke records in the lab but couldn't cut it in the real world. US$22 million buys a lot of potato chips or jet skis, but this is "prove you can scale" money rather than "let's get a big one of these next to every wind farm" money.
So we'll temper our expectations. Still, if H2Pro can deliver a large-scale system making fuel cell-grade hydrogen from green energy at a buck a kilo by 2030, it will have achieved what most projections are estimating as a best-case goal for 2050, 20 years ahead of schedule. The fast-growing green hydrogen sector would explode – a word most folk would probably like to keep well clear of any hydrogen discussions – and this company would stand poised to make a huge contribution to the colossal task of decarbonizing the modern world.
The video below adds little, but will give you a sense of where the company's at.
Source: H2Pro