According to some estimates, the generation of the heat used to produce traditional portland cement is responsible for 5% to 8% of all human-made CO2 emissions. A new substance known as C-Crete, however, is claimed to be a much greener – yet still practical – alternative.
C-Crete is being developed by a California-based startup of the same name, which was founded by MIT Civil and Environmental Engineering grad Rouzbeh Savary.
Although the product's exact ingredients are a closely guarded trade secret for now, it is said to contain "patent-pending materials" that bind with unspecified mineral feedstocks and industrial byproducts which clients can obtain locally. Importantly, no heat is required in its production.
When C-Crete is combined with water and an aggravate such as sand or gravel, the end result is cement-free concrete. Third-party testing has reportedly shown that C-Crete meets performance requirements for portland cement, such as strength and flowability.
And as an added bonus, once the substance has cured, it absorbs atmospheric carbon dioxide. That trapped and mineralized CO2 is claimed to actually increase the strength of the concrete over time.
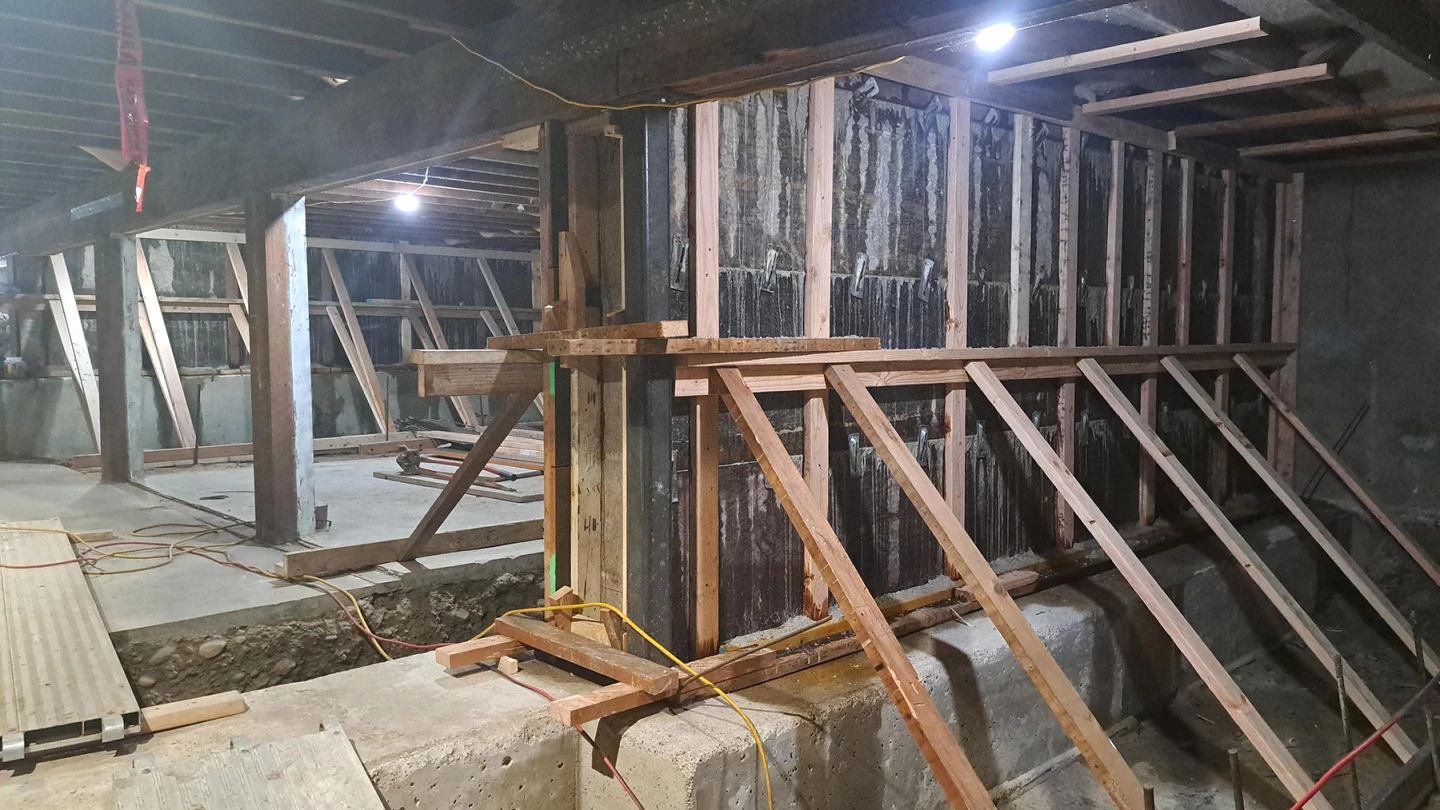
Importantly, C-Crete is utilized just like portland cement, using the same equipment and the same mix ratios. Savary believes this fact will be key to its widespread adoption by the mass market.
"Because the industry is so used to portland cement, and also because of the liabilities involved in construction projects, if a new product is complicated to use or behaves differently, contractors and workers won’t switch," he says.
"It had better be a drop-in technology that bears minimal to no changes in the current behavior of concrete, from its dry mix components to its liquid and hardened stages. We wanted to make C-Crete as easy and as close as possible to conventional practices."
C-Crete is currently being produced in relatively small quantities at a dedicated facility, although it is hoped that production rates will soar once commercial partners get on board. The material has already been utilized in the restoration of a historic building in Seattle.