Production of the cement used in concrete is a major source of greenhouse gas emissions, which is why some people have tried replacing it with fly ash. A new technique makes that fly ash more eco-friendly itself, resulting in concrete which is both greener and stronger.
When producing widely used Portland-style cement, calcium and other ingredients must be heated to very high temperatures. It has been estimated that the processes by which that heat is generated are responsible for 5% to 8% of all human-made CO2 emissions.
With this problem in mind, scientists have tried substituting fly ash for some of the cement used in concrete mixtures (the other ingredients being sand and/or gravel, and water).
Fly ash is a waste product left over from the burning of coal, and while it has qualities similar to those of cement, it also contains toxic heavy metals. If concrete incorporating that ash were to be used in roads or sidewalks, it's possible that those heavy metals may gradually leach out of it and into the surrounding environment.
Seeking to address that shortcoming, scientists at Rice University in Texas developed a process that begins with fly ash being mixed with electrically conductive carbon black powder.
Drawing on a technique known as flash Joule heating, that mixture is then placed between two copper or graphite electrodes (connected to a capacitor), which deliver a short electric pulse to the material. The application of that current causes the mixture to rapidly heat to a temperature of about 3,000 ºC (5,432 ºF), causing the heavy metals to evaporate into a steam which is captured in a vacuum chamber.
"By using this method, we can eliminate the heavy metals from coal fly ash with very high efficiency," said postdoctoral research associate Bing Deng, co-lead author of the study. "For different heavy metals like arsenic, cadmium, cobalt, nickel and lead, the removal efficiency is up to 70% to 90% in just one second."
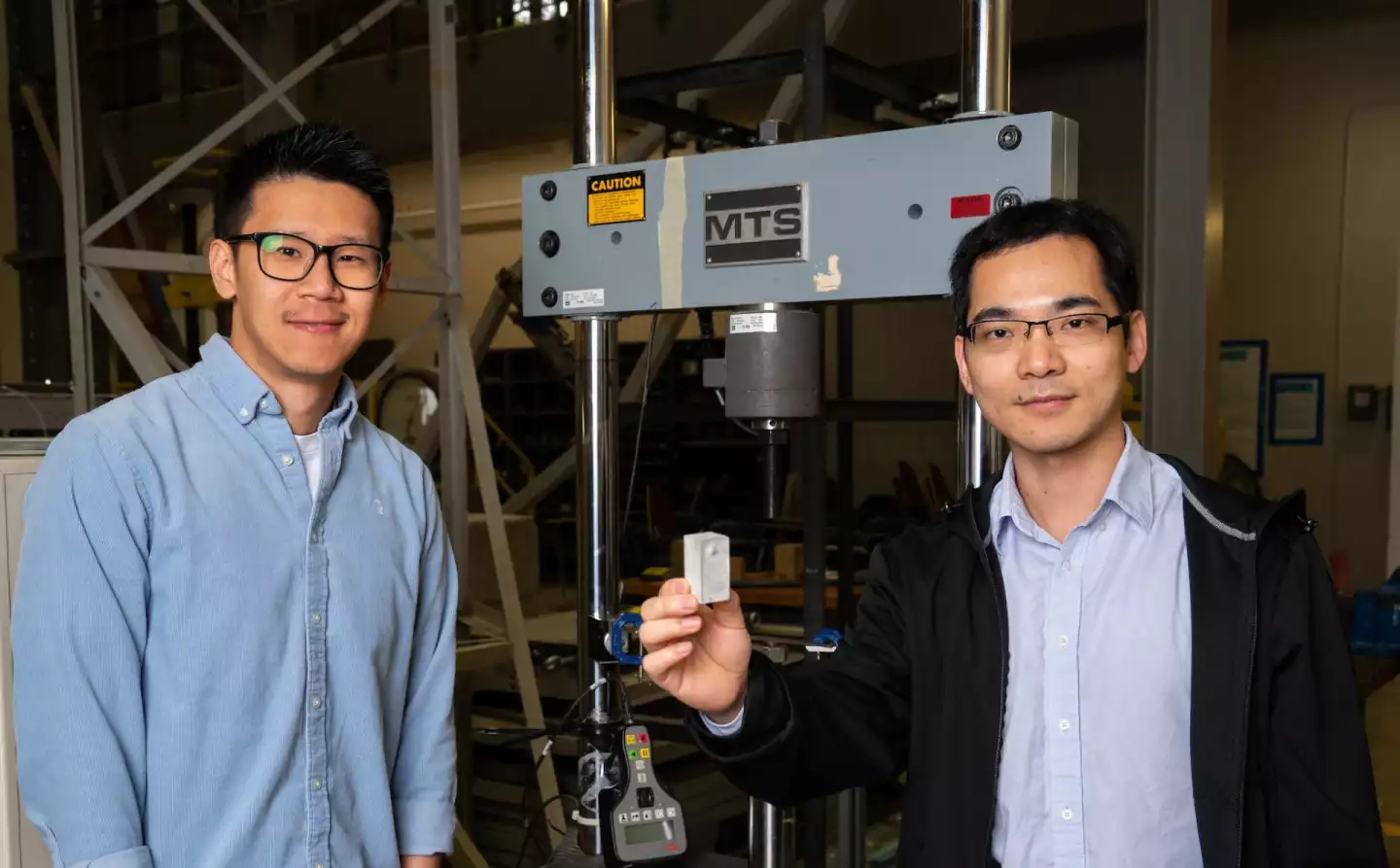
As an added benefit, concrete made with the purified fly ash is also stronger than that made with pure cement. More specifically, when the scientists replaced 30% of the cement in a concrete mixture with the ash, the resulting concrete was found to be 51% stronger and 28% more elastic than control samples.
"This is very meaningful for structural engineering and the construction industry because stronger structures can be built with less cement," said postdoctoral research associate Wei Meng, another co-lead author.
A paper on the research was recently published in the journal Communications Engineering.
Source: Rice University