Festo’s BionicKangaroo is yet another impressive addition to the company’s already mind-blowing bionic zoo that includes, among other things, bionic seagulls, dragonflies, flying penguins, elephant trunks and a whole selection of robotic marine critters. Just like its animal cousin, the robo-marsupial developed by Fasto’s Bionic Learning Network is able to store energy from the landing phase of a jump and reuse it efficiently on subsequent jumps. The technology developed for the BionicKangaroo may hold the key to more energy-efficient machines based on both pneumatic and electric drive technologies.
The BionicKangaroo features pneumatic actuators that provide the jumping power and at the same time act as shock absorbers on landing. The necessary compressed air is supplied either from a small compressor or from a high pressure storage device on board. Electric motors are used for maintaining balance and controlling the kangaroo’s position with high accuracy, e.g. optimizing the tail and hip movements. All electric components rely on energy from rechargeable lithium polymer batteries.
The light-weight construction, (it has a total weight of 7 kg (15 lb)), combined with stable and powerful jump mechanics constantly kept in check by an embedded control system, enable this 1 m (3.2 ft) tall robot to jump 0.8 m (2.6 ft) horizontally and 0.4 m (1.3 ft) vertically. But unlike real kangaroos, the largest species of which can jump up to around 12 m (39 ft) thanks to a pronounced Achilles tendon, the robotic imitation uses an elastic spring element made of rubber.
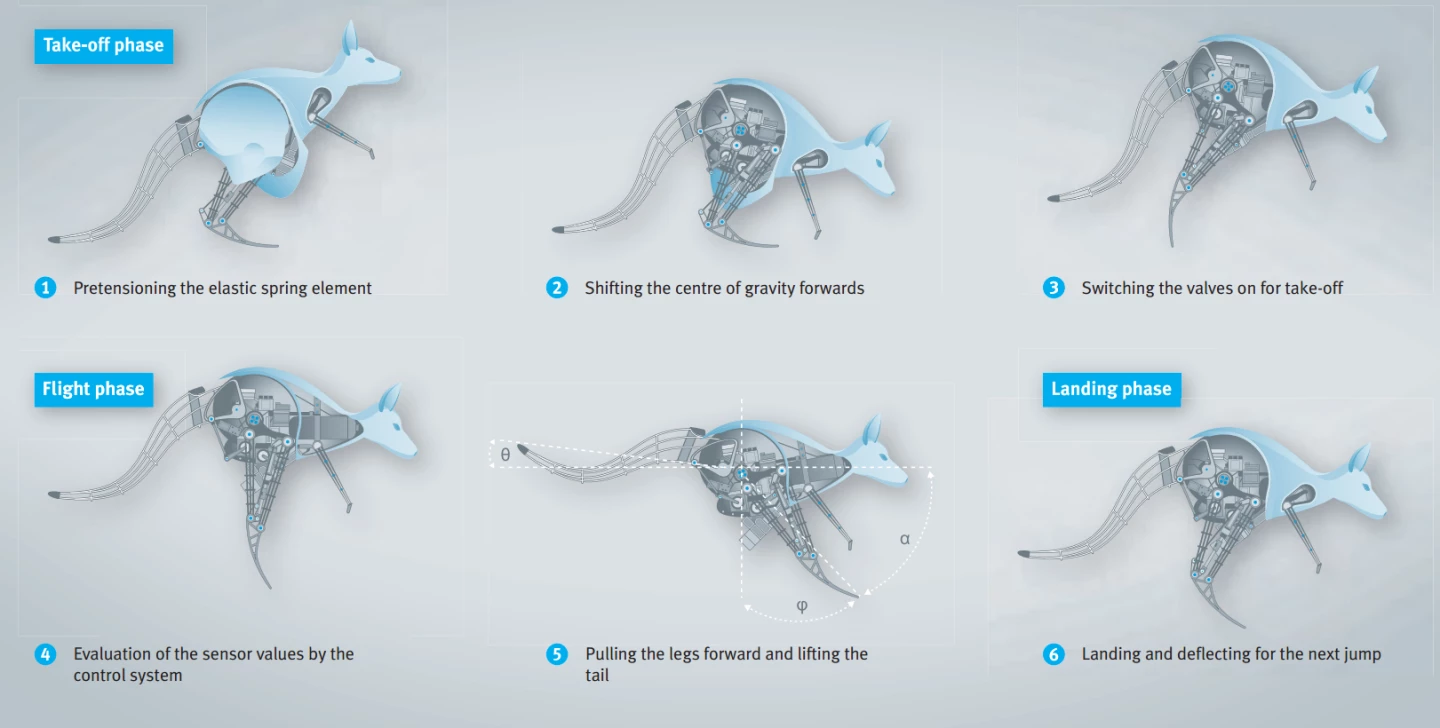
The function of this artificial tendon is to cushion the jump and absorb the kinetic energy upon landing. Before the first jump, the rubber tendon is pneumatically tensioned and the kangaroo starts tilting forward as it shifts its center of gravity. Once an optimal tilt angle is achieved, the tendon is released and the kangaroo jumps up, thrusting its legs forwards and lifting its tail. At this stage it is the control system’s job to make sure the legs cover as much ground as possible and that the tail movement is just right to compensate for the torque created at the hip area, keeping the top section of the robotic animal oriented more or less horizontally throughout the jump.
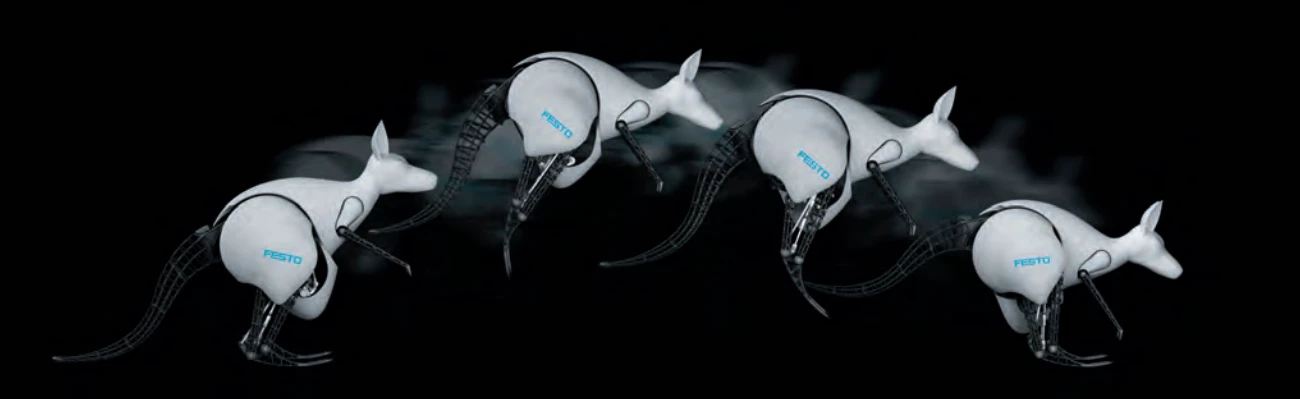
The real magic, however, happens on hitting the ground when the tendon is again tensioned and kinetic energy is converted into potential energy that can be stored in the system and used for the next jump. By that time, the tail is back in its original position. By channeling the energy directly into the next jump and aiding each hop in exactly the right moment by switching the valves, the BionicKangaroo is able to take several jumps in a row without expanding much energy. Stopping is achieved by absorbing as much energy as possible and tensioning the tendon.
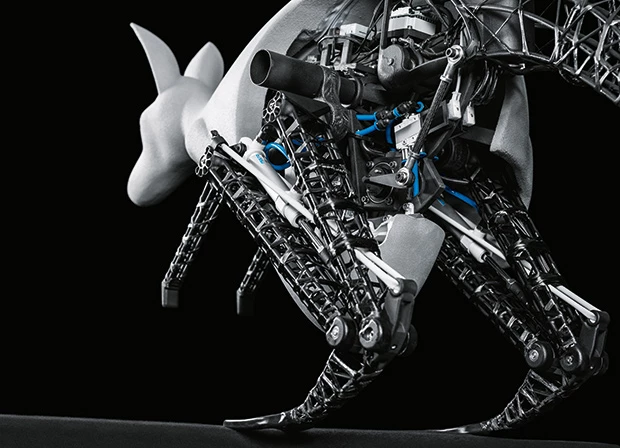
Festo's Bionic Learning Network has a very clear purpose, and that's learning from nature in order to advance the field of industrial automation. It seems building amazing robotic animals is something of a spectacular side effect. For example, the solutions developed for Festo's bionic seagull have recently found their way into a wind energy harvesting system. The main focus of the two-year-long BionicKangaroo project has been to learn how to create more energy-efficient and flexible systems that dynamically combine pneumatics and electrics and are capable of capturing, storing and reusing energy.
All the same, it is difficult not to hope for a commercially available BionicKangaroo. Who knows, maybe a slightly larger version with a saddle could one day revolutionize urban mobility? While it remains unclear what future awaits the BionicKangaroo, we may get some clues when the robot is officially unveiled to the public at the Hannover Messe trade show later this week.
As shown on the video below, the BionicKangaroo can also reposition itself while on the ground after receiving gesture control commands via a MYO armband.
Source: Festo via IEEE Spectrum