The idea of owning your own plane is the stuff of daydreams. It’s incredibly appealing, but despite some (relative) drops in pricing in recent years, it remains incredibly expensive. If you build your own plane from a kit, it’s a bit cheaper than buying one, but the odds are that you’ll never complete the job because kitplanes are notoriously difficult to build. However, that may be changing. MakerPlane is a project that aims to create an open source aircraft designed by contributors and built with digital manufacturing processes. You can’t download the plans into your 3D printer and fly away that afternoon, but it does hold the promise of making amateur aviation a lot more accessible.
MakerPlane plans to do for the aviation industry what Firefox and Linux did for computers. By adopting open source design and digital manufacturing, MakerPlane's founder John Nicol hopes to overcome the frustration and disappointment that most kit plane builders encounter. Over 60 percent of all kitplanes started end up collecting dust and those that are finished must overcome the challenges of complicated plans, the need for special tools and thousands of hours of labor with little or no manufacturer support.
Nicol believes that a more community-oriented design approach will overcome many of these obstacles. Israel-based aeronautical engineer Jeffrey Meyer is leading the MakerPlane charge to develop a safe, inexpensive kitplane that can be built at home or at a “makerspace” through the efforts of people volunteering their efforts and ideas. MakerPlane intends to make the plans and avionics software for the plane available for free, but will sell parts and support services to fund the project.
The basic design of MakerPlane 1.0, the prototype, has been settled on. It will be a two-seater light sports plane with a maximum takeoff weight of 600 kilograms (1,320 lbs) with a maximum speed of 120 knots (138 mph, 222 kph) and a ballistic parachute as a safety feature. “Basic” is the operative word here because one aspect of the MakerPlane project is to make the aircraft modular with many different options available as to wings, landing gear, engine and so on.
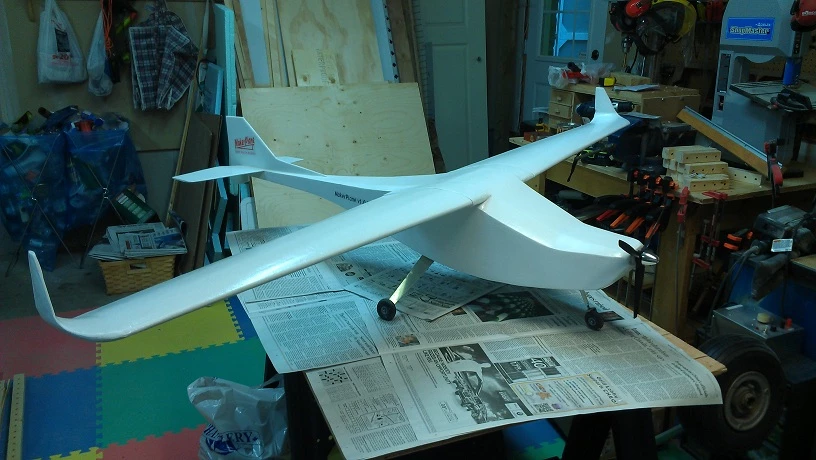
The other side of the MakerPlane project is that the aircraft will forego traditional building techniques in favor of digital fabrication. MakerPlane 1.0 will be built using computer-controlled (CNC) routers with 3D printers to help fabricate some of the parts. MakerPlane will also supply builders with the electronic files needed to program the machinery.
“The time savings are immense," says Nicol. "A wing rib can be cut out on a CNC machine in a matter of two or three minutes, instead of the current two or three hours using traditional methods. Our build process will include simple step by step build and assembly instructions, videos and animations. We are hoping to minimize text as much as possible.”
So far, MakerPlane 1.0 is still in the design stage, but the aim is to have the design complete within a year and for the prototype to fly at the 2014 AirVenture air show in Oshkosh, Wisconsin.
Source: MakerPlane via DVICE