The production of traditional Portland cement is a major source of greenhouse gas emissions, as the ingredients have to be heated to very high temperatures. Such is not the case with a new biocement, however, which also incorporates waste materials.
Developed at Singapore's Nanyang Technological University, the biocement is made of two main substances – industrial carbide sludge, which is a byproduct from the production of acetylene gas, and urea, which is derived from the urine of mammals such as humans, cows or pigs.
The sludge is initially treated with an acid, causing it to produce soluble calcium. The urea is then added to that calcium, forming what is known as a cementation solution. Special bacteria are subsequently added to that solution, where they break down the urea to form carbonate ions.
Next, in a process called "microbially induced calcite precipitation," those carbonate ions react with the soluble calcium ions to form hard, solid calcium carbonate. When the mixture is combined with sand or soil as that reaction is taking place, the calcium carbonate bonds the sand/soil particles together and fills the spaces between them.
The result is a solid block of material that's resistant to water seepage, and that is the same color as the original sand or soil. What's more, the whole production process takes place at room temperature.
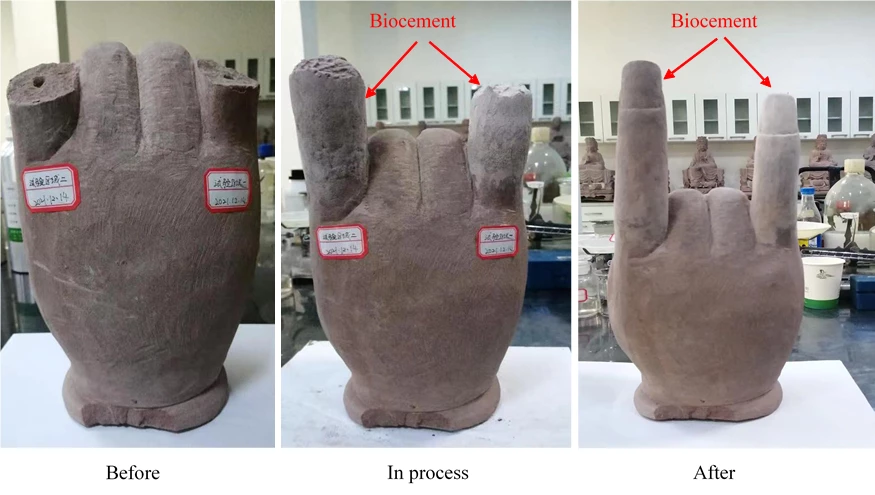
Possible applications for the biocement include strengthening the ground at construction sites, reducing the erosion of beaches (by forming a hard crust on top of the sand) and building freshwater reservoirs. The material has even already been used to fill cracks and rebuild sections of damaged stone monuments.
A paper on the research, which is being led by Prof. Chu Jian and Dr. Yang Yang, was recently published in the Journal of Environmental Chemical Engineering.
Source: Nanyang Technological University