There is a lot engineers can learn from Japanese paper folding art forms, from cheap batteries made from paper and water to tiny robots that are activated by heat. While origami gets a lot of the attention, a variation of this called kirigami also has plenty to offer. A team of scientists has taken this technique down to the nanoscale for the first time, a breakthrough they say opens up new possibilities in applications ranging from robotics to aerospace.
Kirigami is much like origami, except not only is the paper folded to create different shapes, it is also carefully cut in selected places to achieve the finished product. Recently, we’ve seen engineers take inspiration from this art form to develop novel solar cells that twist to track the Sun, robotic snakes that propel themselves and programmable balloons that inflate into crazy shapes.
These types of structures are achieved through very precisely placed geometric cuts that give very thin films of material unique sets of properties, but only at the macroscale, or what can be seen with the human eye, so far. Scientists at Northwestern University have now succeeded in applying this technique to structures measured in the nanoscale. For reference, a human hair is around 100,000 nanometers wide.
The team started with ultrathin films and made carefully placed kirigami cuts throughout them. Residual stresses in these films then create structural instabilities, which in turn cause shifts in and around the cuts to turn the 2D material into an engineered 3D structure. The cuts can be varied to make materials that bend and twist and to create unusual 3D shapes, both symmetric and asymmetric.
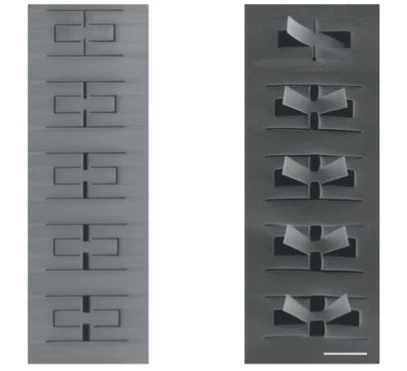
According to the researchers, these shapes could find use in all kinds of areas, from tiny robotic grippers, to spatial light modulators for optical applications, to controlling the flow of airplane wings. From here, the team plans to continue exploring the potential of kirigami engineering techniques, including the possibility of incorporating actuators for deployment or control of the finished product.
“By combining nanomanufacturing, in situ microscopy experimentation, and computational modeling, we unraveled the rich behavior of kirigami structures and identified conditions for their use in practical applications,” says Horacio Espinosa, who led the research.
The study was published in the journal Advanced Materials, while the video below offers a quick look at the technique in action.
Source: Northwestern University