Chopping down trees and processing the wood isn’t the most efficient or environmentally friendly way to make furniture or building materials. Scientists at MIT have now made breakthroughs in a process that could one day let us 3D print and grow wood directly into the shape of furniture and other objects.
Wood may be a renewable resource, but we’re using it up much faster than we’re replenishing it. Deforestation is having a drastic impact on wildlife and exacerbating the effects of climate change. Since our appetite for wooden products isn’t likely to change, our methods for obtaining it will have to.
In recent years, researchers have turned to growing wood in the lab. Not trees – just the wood itself, not unlike the ongoing work into cultivating animal cells for lab-grown meat, rather than raising live animals and slaughtering them. And now, a team of MIT scientists has demonstrated a new technique that can grow wood-like plant material in the lab, allowing for easy tuning of properties like weight and strength as needed.
“The idea is that you can grow these plant materials in exactly the shape that you need, so you don’t need to do any subtractive manufacturing after the fact, which reduces the amount of energy and waste,” says Ashley Beckwith, lead author of the study. “There is a lot of potential to expand this and grow three-dimensional structures.”
First, the team isolated cells from the leaves of plants known as Zinnia elegans. Then, these cells were cultured in a liquid medium for two days before being transferred to a thicker, gel-based medium. This stuff contained nutrients and two different plant hormones, the levels of which could be tweaked to tune the physical and mechanical properties of the material.
Next, the team 3D printed this cell-loaded gel into a specific shape, the same way you’d 3D print a plastic object. After three months of incubation in the dark, the material is dehydrated and the final result is a custom object made of wood-like plant matter. In one test, for example, the team shaped the material into a model of a tree.
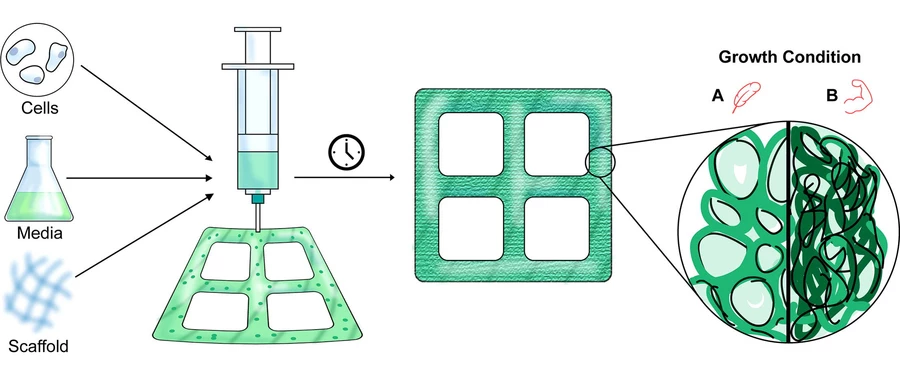
The team experimented with different levels of the hormones, and found that lower levels led to lower density material, with rounded, open cells. Higher levels, meanwhile, grew smaller, denser structures that were more stiff, thanks to the increased growth of the organic polymer lignin. This difference could be used to make products that are softer and lighter, or stronger and more rigid, as necessary.
Ultimately, the goal is to develop the technology to the point that wooden objects can be essentially 3D printed and grown, rather than cut, shaped and joined from larger pieces of wood obtained from cutting down trees. The process might start with small wooden objects like dowels or decorative pieces, before eventually moving up to furniture or planks for construction.
The next steps, the team says, is to work out how to apply the method to other plants. Zinnia doesn’t produce wood, but adapting the process to work with something like pine could be a major breakthrough.
The research was published in the journal Materials Today.
Source: MIT