Japanese scientists have developed a new type of plastic that’s strong at room temperature, but can be easily broken down on demand into its base components. In seawater, it starts to break down into food for marine life, and just to top it off, it can self-heal and remember past shapes.
Plastic is everywhere in our modern world, for better or worse. Its toughness makes it an extremely useful material for everything from household items to vehicle parts, but that same toughness makes it hard to break down for recycling or disposal.
In the new study, scientists at the University of Tokyo developed a new plastic material that can be broken down more easily, either in recycling plants or in nature. It’s based on a class of plastic called an epoxy resin vitrimer, which are strong at room temperature but can be reshaped and molded with a bit of added heat. Normally, vitrimers are brittle, but the team improved the recipe by adding a molecule called polyrotaxane.
The end result is a new plastic they call VPR, which boasted a huge range of advantages over similar materials. After being scratched with a scalpel, it was able to completely patch itself back up after being heated to 150 °C (302 °F) for just 60 seconds. When it was molded into the shape of a crane, then flattened, it could fold itself back into the crane shape by being heated up. It did all of this much faster than others of its type.
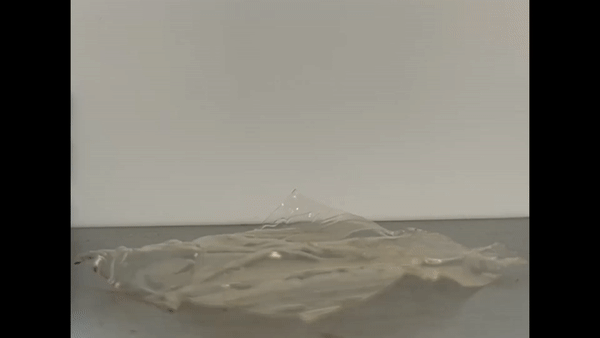
VPR can also break down easier – but only once it’s no longer needed. Applying heat along with a specific solvent will bust apart its molecular bonds and leave only the raw components, ready to be made into something new. Even if it’s discarded into the environment it still poses less of a problem than other plastics, which the team demonstrated by submerging it in seawater for 30 days. In that time, it biodegraded by 25% and released molecules that are essentially food for marine life, the team says.
“VPR is over five times as resistant to breaking as a typical epoxy resin vitrimer,” said Shota Ando, lead author of the study. “It also repairs itself 15 times as fast, can recover its original memorized shape twice as fast, and can be chemically recycled 10 times as fast as the typical vitrimer. It even biodegrades safely in a marine environment, which is new for this material.”
The team says the material could find use in a variety of applications that other plastics are already used for.
“Just to give some examples, infrastructure materials for roads and bridges are often composed of epoxy resins mixed with compounds such as concrete and carbon,” said Ando. “By using VPR, these would be easier to maintain as they would be stronger and healable using heat. Unlike conventional epoxy resins, this new material is hard but stretchable, so it could also be expected to strongly bond materials of different hardness and elongation, such as is needed for vehicle manufacture.”
The research was published in the journal ACS Materials Letters.
Source: University of Tokyo