Scientists experimenting with a cutting-edge ultrasound technique have come up with a groundbreaking and incredibly precise way to measure the elasticity of materials at a microscopic scale. Based on the tracking of sound waves as they bounce across individual crystals, the advance could have important implications in the development of next-generation materials, with potential applications in aerospace engineering and medical implants.
The significance of this breakthrough is tied to the incredibly complex arrangement of microscopic crystals that make up materials such as metal alloys, which can vary in size and shape and number in the millions. Traditionally, measuring the relationship between the stresses and strains, known as the elasticity matrix, of these materials has involved cutting them up or growing just a single crystal.
But these techniques can't be applied to every material known to science, such as the titanium alloys used in jet engines. Only a small percentage of materials have had their elasticity measured, which leaves many with their exact properties unknown.
“Many materials (such as metals) are made up of small crystals," said Paul Dryburgh, co-lead on the study, from the University of Nottingham. "The shape and stiffness of these crystals are essential to the material's performance. This means that if we tried to pull on the material, as we would a spring, the stretchiness depends on the size, shape, and orientation of each of these hundreds, thousands or even millions of crystals. This complex behavior makes it impossible to determine the inherent microscopic stiffness. This has been an issue for over 100 years, as we’ve lacked an adequate means to measure this property.”
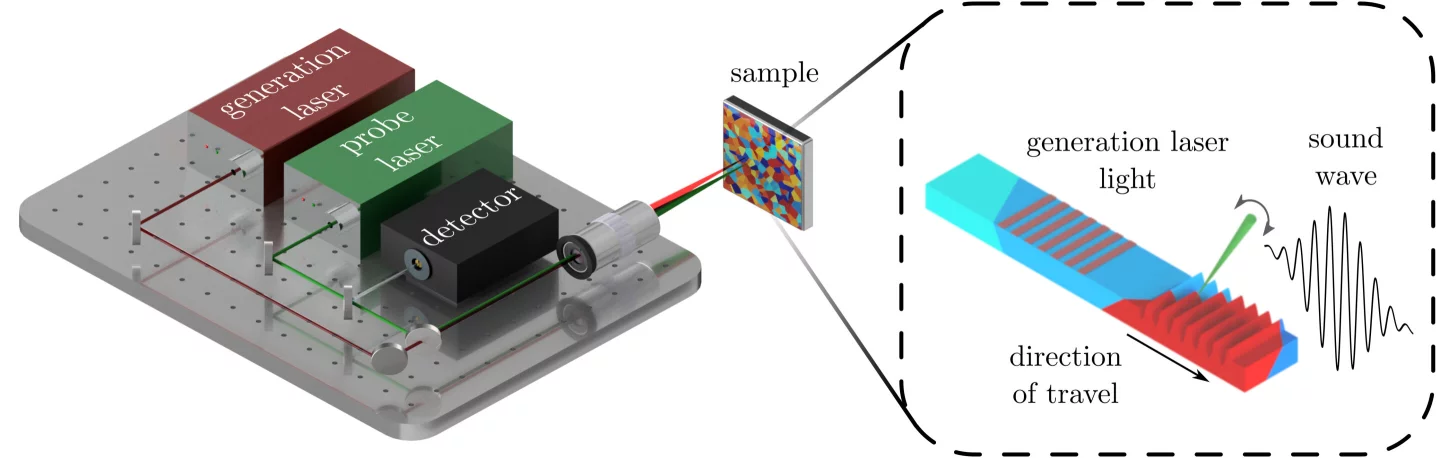
The scientists believe they have come up with a solution to this dilemma, by leveraging a technology known as laser ultrasound. Where traditional ultrasound sends high-frequency sound waves into a sample, such as human tissue, and measures the sounds that bounce back to create an image of the sample, laser ultrasound instead uses light to generate these sound waves.
In 2019 we saw MIT scientists use a form of laser ultrasound to generate images of the human body without any skin contact, impossible with conventional ultrasound. Now the University of Nottingham researchers have used it to open up some exciting possibilities in material science.
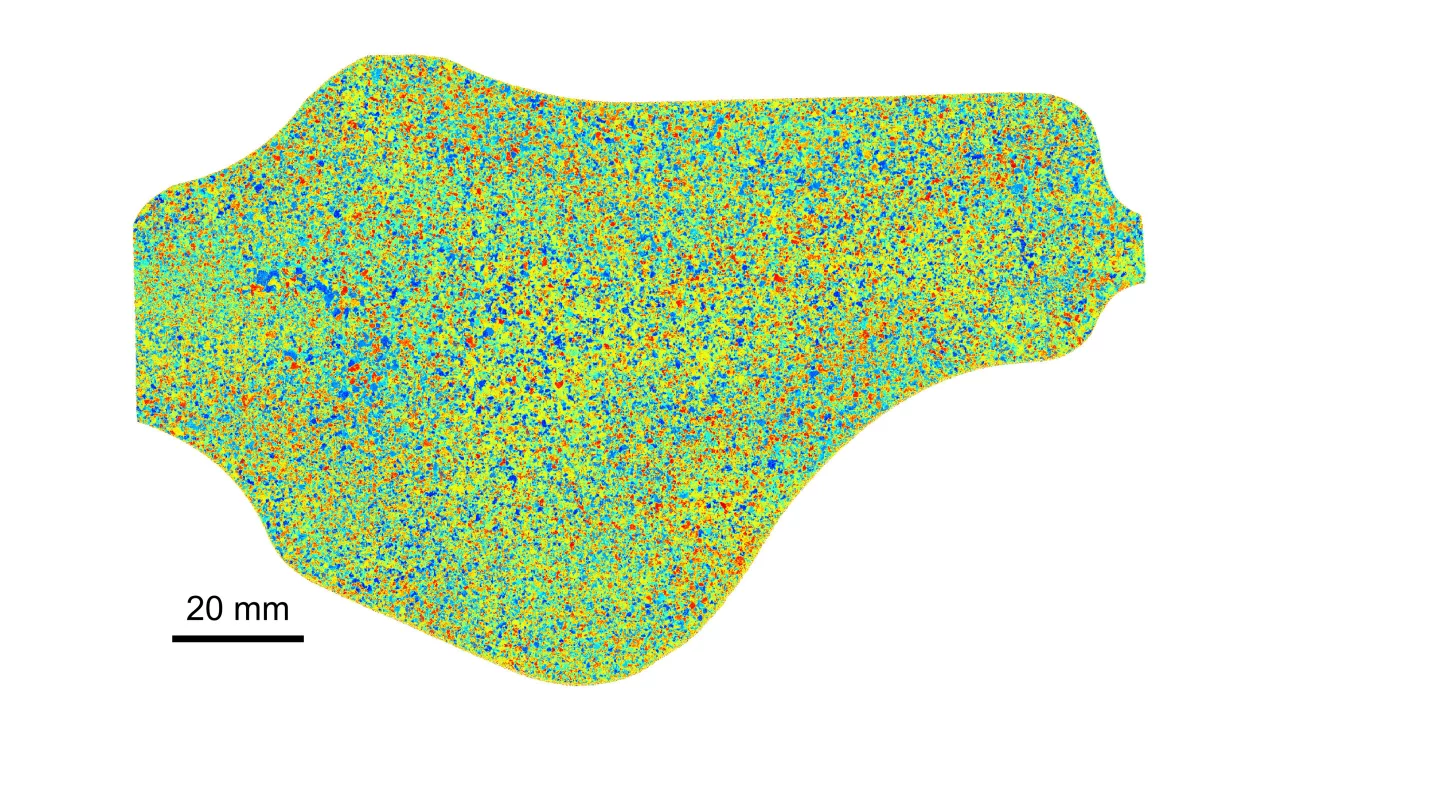
The team devised an experimental laser ultrasound device that can generate high-frequency waves in a tiny space of around 200 micrometers – about the width of two or three human hairs. The laser shoots a high-energy pulse of light at the sample material, which creates a sound wave that travels along its surface and is tracked with a built-in detector to reveal the orientation of single crystals, along with their elasticity. Equally impressive is the speed at which the technology, called SRAS++, can conduct these measurements.
"The development of SRAS++ is a notable breakthrough because it provides the first method to measure the elasticity matrix without knowing the distribution of crystals in the material," said Professor Matt Clark who co-led the research. "SRAS doesn’t require exacting preparation of a single crystal; it is fast (thousands of measurements can be made every second) and offers unparalleled measurement accuracy. The speed of the technique is such that we estimate that we could repeat all the historical elasticity measurements of the past 100 years within the next six months."
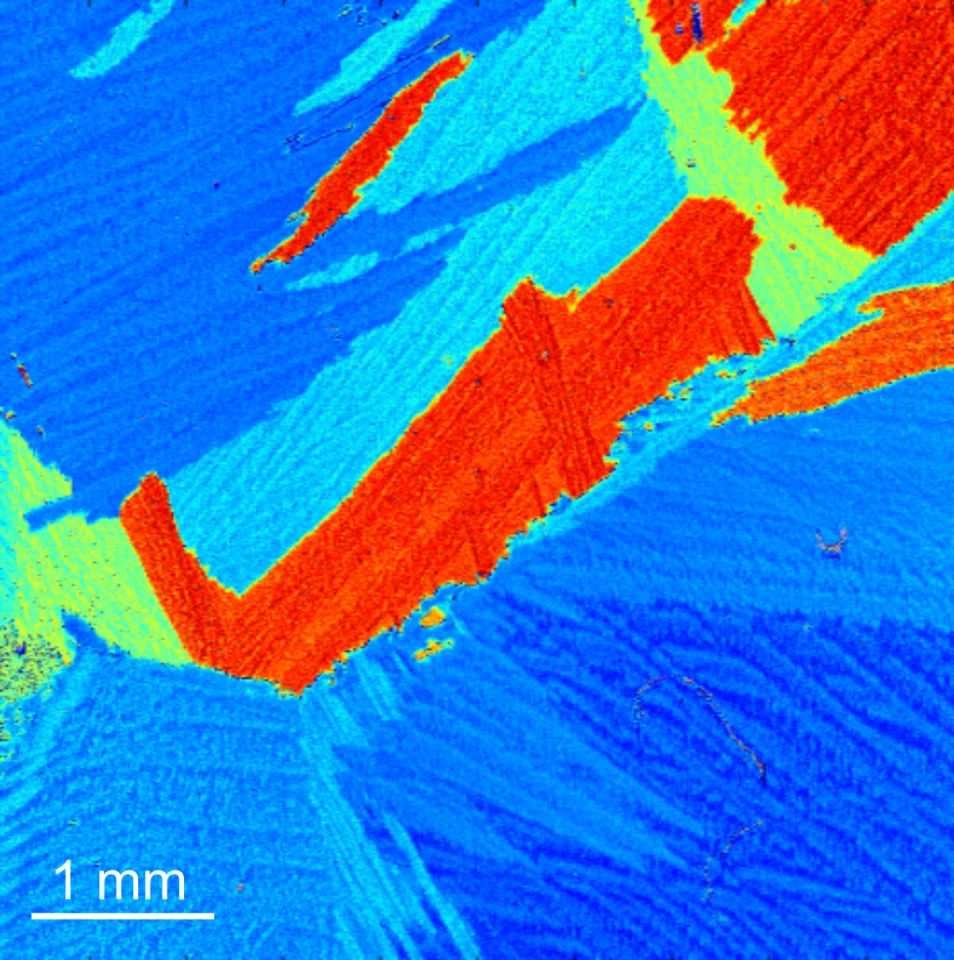
The team validated the device's accuracy through experiments on pure nickel, titanium and a nickel-CMSX-4 alloy, with the specimens chosen for their favorability among aerospace engineers. The scientists however imagine SRAS++ enabling the development of new designer alloys with tailored stiffness, which could not only find use in aircraft but in prosthetic devices with elasticity that matches the human body.
The research was published in the journal Acta Materialia.
Source: University of Nottingham