Featured in comic books since 1963, Dr. Octopus, or "Doc Ock" is an enemy of Spiderman with four extra robotic arms attached to his back that assist him in his nefarious plans. That vision of humans with extra limbs – minus the supervillain part – is taking shape at MIT with researchers adding "supernumerary robotic arms" to assist with tasks that ordinary two-armed humans would find difficult.
There are many tasks around the house or factory that you have probably said to yourself, “if I only an extra arm, this would be a lot easier." Tasks like hanging a ceiling fan, installing an overhead light fixture, or even just holding open a box would be easier if there was an extra arm to help out. Now engineers are envisioning two robotic arms as helping hands.
The project is being run at MIT’s d'Arbeloff Laboratory for Information Systems and Technology and headed by Federico Parietti and Baldin Llorens-Bonilla, both in the Mechanical Engineering Department. Federico has been working on lower limbs, bracing strategies, and stability, while Baldin contributed to the robot shoulder arms, along with coordination and task planning.
The concept was demonstrated with installing ceiling panels in an airplane, a task that must be duplicated dozens of times in the construction of an airliner. A single person installing a large panel overhead must struggle between holding the panel to the ceiling, inserting screws into holes, and using a powered screwdriver to attach the panel. The juggling and dropping of screws would drive any of us to frustration and profanity.
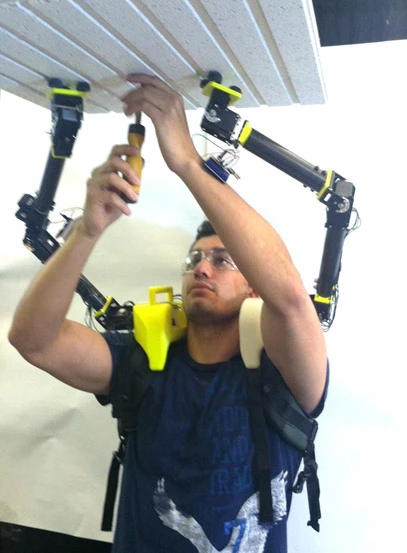
The Supernumerary Robot Limbs (SRL) team looked at this task, and added two lightweight robot arms to a frame attached to a backpack. The arms are attached directly over the spine so that the body can carry the extra weight without strain. This alone would be noteworthy, except that the user now has no way to command the robot arms to move – a conventional joystick or gamepad would take up hands already busy with panels.
So the amazing part of this research is having the arms decide for themselves when and where to help. Sensors on the human’s wrists and on the robot mount determine where the human is on the task, and assigns the robot arms to help.
The robot arms assist the user by pushing up the panel against the ceiling, allowing the human operator to put in screws to attach the panel. As the panel is able to support itself, first one arm goes down, and then the other as the robot senses that the force required to maintain the pose has diminished.
The arms are programmed by the "teach by demonstration" method. A second human first demonstrates to the robot how to help by moving the robot arms manually with the the robot remembering this lesson so it is then able to make the moves on its own.
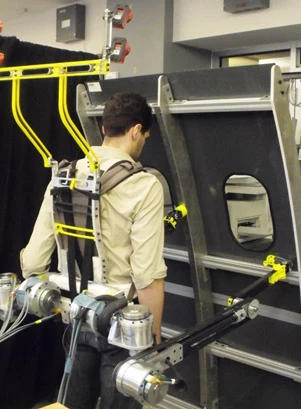
Another application studied by the group is using arms attached to the wearer’s waist that can automatically add stability. Imagine a construction worker trying to drill a hole in a beam while working on a new skyscraper a hundred meters in the air, standing on another beam a few centimeters or inches wide. The supernumerary arms attached to the waist would grab the beams for support and act as stabilizers, attaching the worker to the structure at two points, just like having two extra arms to hold on with.
Each of the robot’s limbs can sense the applied torque, and modify its movements accordingly. Besides just passively holding panels in position, the robot arms can also assist with more precision tasks, like guiding a drill to a particular spot. The research team spent a lot of time developing specific techniques for computing where the robot arms can best assist, and deciding where the robot arms can best be attached for support.
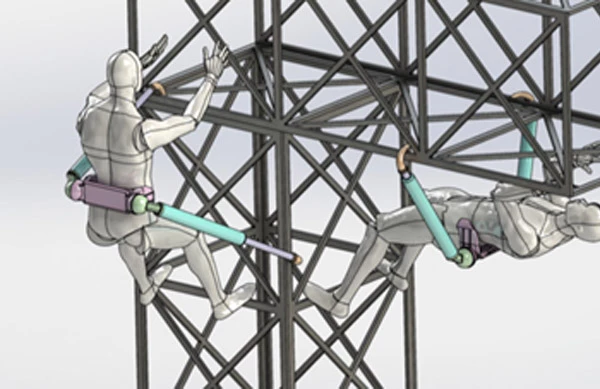
The project is being supported in part by Boeing, hence the interest in aircraft assembly, but the team sees a range of potential applications for the technology. These include assisting senior citizens, construction workers, and other assembly operators where extra arms might come in (pardon the phrase) handy.
"We want our design to be as light and ergonomic as possible without compromising the robot’s power and capabilities," says Baldin.
The current design is the third generation of robot arms developed, with the shoulder arms weighing about 11-12 lbs. (5-5.4 kg). The team is planning further development of the concept to reduce weight, increase strength, and improve coordination by "developing better control algorithms and increasing the sensing capabilities of the robot."
The video below shows the robotic limbs being demonstrated installing ceiling panels in an airplane.
Sources: MIT d’Arebeloff Laboratory for Information Systems and Technology, Federico Parietti, Baldin Llorens-Bonilla