An international team of scientists based at the University of Texas, Dallas (UTD), has developed a new type of artificial muscle created from carbon “nanotubes” – tiny hollow cylinders constructed from the same graphite layers found in the core of a standard pencil. Despite measuring 10,000 times less than the diameter of a human hair, the new muscles can lift more than 100,000 times their own weight, which amounts to approximately 85 times the power of a natural muscle of equivalent size.
The new muscles are manufactured by taking a twisted yarn of the miniscule carbon cylinders, then introducing a volume-changing “guest,” in this case the paraffin wax used in candles.
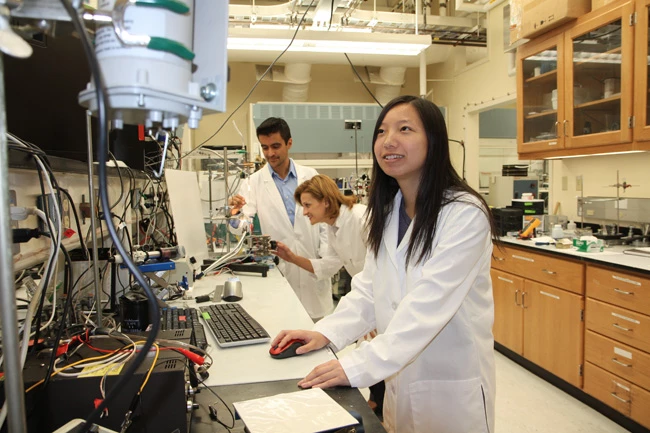
The wax-coated yarn is then heated either electrically, or with a flash of light, and this causes the wax to expand, with the yarn volume increasing, and the length of the material contracting as a result. This muscle contraction, or actuation, can occur in just 25 thousandths of a second. Taking into account times for both actuation and reversal of the actuation, the UTD researchers demonstrated a contractile power density of 4.2 kW/kg, four times the power-to-weight ratio of a typical internal combustion engine.
However, while the new technology has many applications, it is not expected to be used in the human body, for now at least. This contrasts with the somewhat similar research into artificial muscles for nanobots we reported on last year.
“The artificial muscles that we’ve developed can provide large, ultrafast contractions to lift weights that are 200 times heavier than possible for a natural muscle of the same size,” explained Dr. Ray Baughman, team leader, Robert A. Welch Professor of Chemistry and director of the Alan G. MacDiarmid NanoTech Institute at UT Dallas. “While we are excited about near-term applications possibilities, these artificial muscles are presently unsuitable for directly replacing muscles in the human body.”
Dr. Baughman further explains that because of the simplicity of their construction and high-performance, the new artificial yarn muscles may be implemented in a variety of areas, such as catheters for minimally invasive surgery, microvalves, toys, and robots. The muscles could also be employed in self-powered intelligent materials, such as a protective suit which reacts to changes in environmental temperature in order to offer the wearer appropriate levels of protection, for example.
In addition, testing shows that the wax-infused carbon tubes are able to withstand temperatures 1,000 C (1,832 Fahrenheit) above the melting point of steel, where no other current actuator can operate.
The next challenge for the UTD researchers is to upscale the single-yarn muscles, to larger and more complex systems which implement thousands of yarn muscles in parallel.
The research was detailed in a study published in the November 16 issue of the journal Science. In the video below, Dr. Baughman explains the research further.
Source: UTD