NASA's Marshall Space Flight Center is developing a trio of new additive and milling technologies to create a 3D-printed rocket nozzle that is simpler in design than comparable ones, yet is able to withstand extreme temperatures and pressures. Made by a new process called Laser Wire Direct Closeout (LWDC), a prototype nozzle was fired successfully for more than 1,040 accumulated seconds.
Rocket nozzles have a very simple, but important function of expanding and accelerating the combustion gases or other propellants from a rocket. In very simple solid rocket motors, this nozzle might be a plug of milled metal, but in larger, more advanced liquid fueled rockets, they are very complicated constructs that circulate cold fuel around the nozzle to protect it against the extremely hot, high-pressure gases from the combustion chamber.
The problem is that these nozzles need to be fabricated out of many parts, which makes building prototypes slow and expensive. 3D printing can simplify this by allowing engineers to produce a nozzle with many fewer parts that can be quickly and cheaply produced – allowing for rapid prototyping.
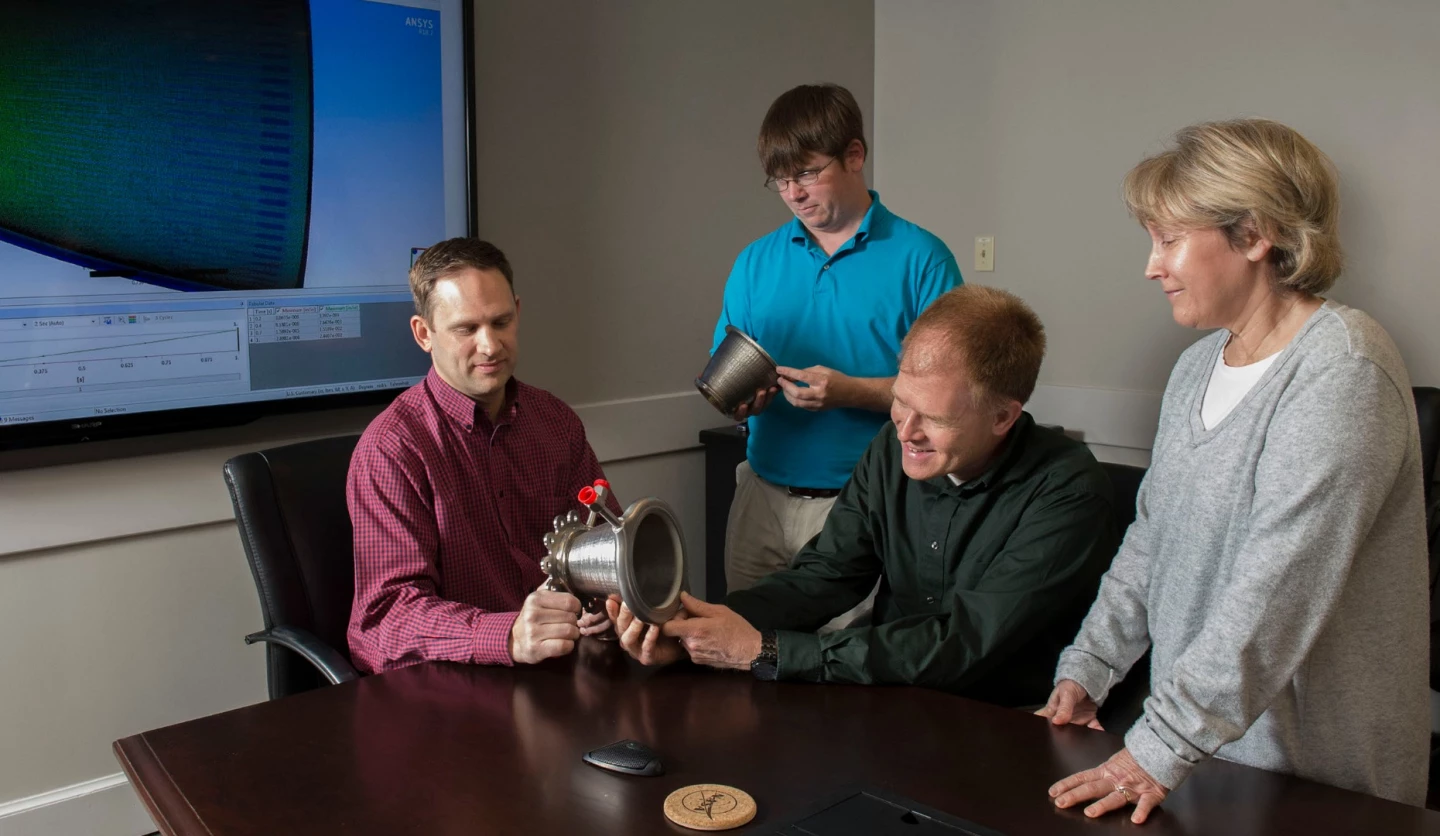
The NASA-developed LWDC is an advance on more conventional powder-based metal printing methods. In the latter, metal alloy powder is spread in layers, which is melted into the desired pattern using lasers or electron beams. LWDC is more freeform, using directed energy beams to melt metal wires and directly depositing the molten metal in a manner similar to that used in plastic 3D printing. According to the space agency, LWDC can reduce fabrication time from months to weeks.
NASA is using LWDC in conjunction with an abrasive water jet milling process and an arc-based deposition technology. The three new technologies were used to precisely close out the coolant channels inside the nozzle to form a support jacket and to fabricate the liner to contain the water jet milled channels.
"Our motivation behind this technology was to develop a robust process that eliminates several steps in the traditional manufacturing process," says Paul Gradl, a senior propulsion engineer in Marshall's Engine Components Development & Technology Branch. "The manufacturing process is further complicated by the fact that the hot wall of the nozzle is only the thickness of a few sheets of paper and must withstand high temperatures and strains during operation."
NASA says that the technology, which was developed through the agency's Small Business Innovation Research program in partnership with Keystone Synergistic of Port St. Lucie, Florida, will be licensed for commercial applications as a way to stimulate small businesses.
The video below shows a test firing of a 3D-printed nozzle.
Source: NASA