The Porsche 918 Spyder hybrid supercar has been called the "genetic blueprint for the Porsche sports car of the future," but the technical innovations aren't restricted to the car's two electric power systems and V8 engine punching 887 bhp. The company has also put a lot of innovation into its Porsche 918 Spyder factory in Stuttgart-Zuffenhausen. The 4,000 sq m (43,000 sq ft) facility where the 918 is hand built employs 100 people and uses a new take on the assembly line.
Production of the 918 began at Zuffenhausen in 2013. Based on a watchmaker's cleanroom, the factory consists of 18 stations making up four production stages, where the monocoque, the engines, the leather finish, and the body shell are assembled. The L-shaped layout, where almost all of the assembly is carried out, appears surprisingly well lit and open and not at all like the popular idea of a car assembly line.
It's also a bit slower than the usual assembly line. Producing each car takes about 100 hours, which includes continuous testing during assembly before the car is taken by a lift to a testing area on the floor below for a final check out. Using the "one technician, one engine" principle, it takes 40 hours to make each engine for the 918. Even the leather sun visor cover takes 200 hand stitches and 40 minutes of work. Assembly would take even longer, except that Porsche has introduced a high degree of standardization and plug-and-play components.
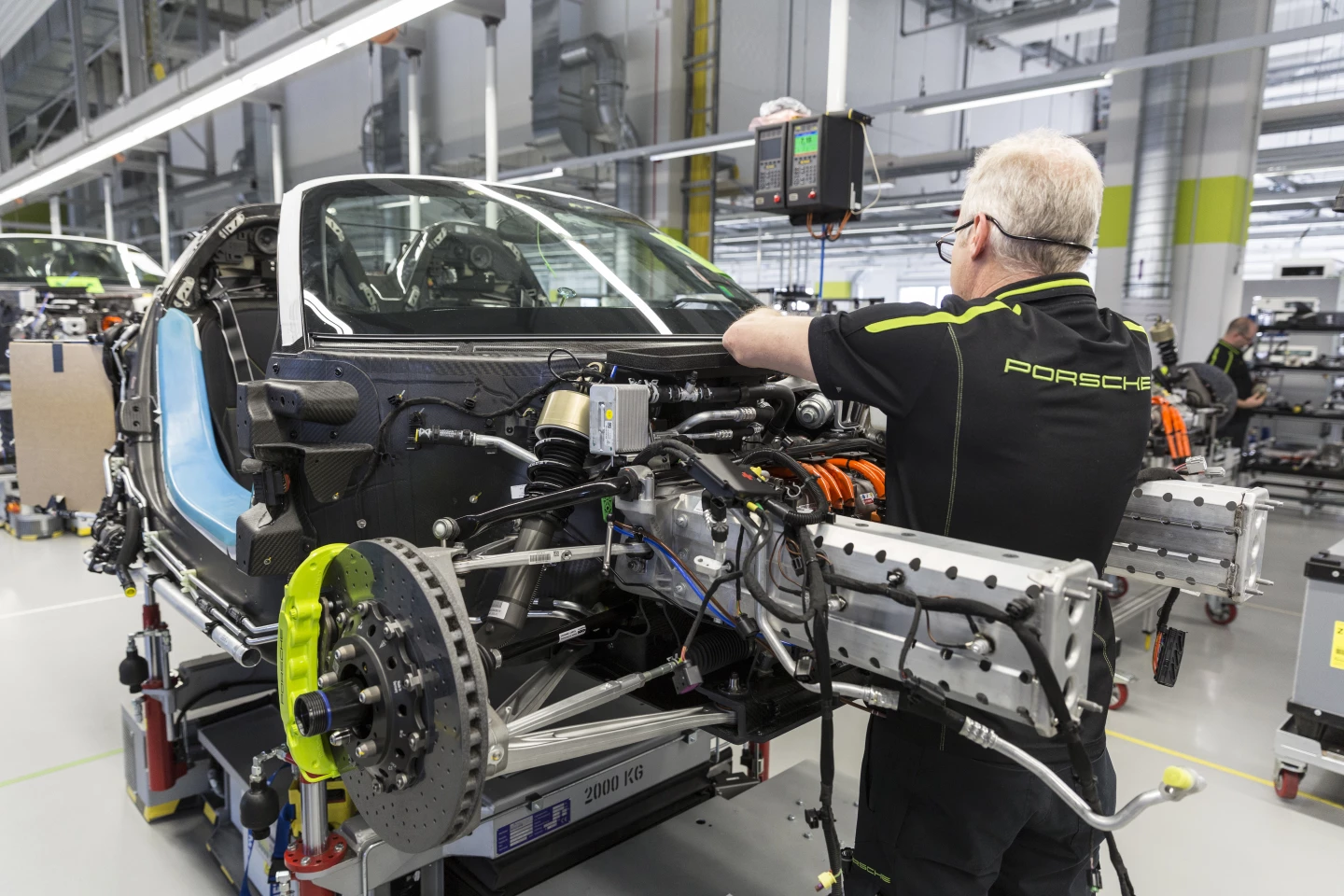
Porsche says that the reason behind this leisurely pace is the promotion of high precision, high quality workmanship. The line uses the Porsche herringbone model, where the work stations are supplied by pre-assembly areas to the left of the line. The cars are carried on electric-powered platforms and when assembled leave in electric mode, so the assembly is strangely quiet.
One innovation that makes this possible is the scissors lift platform that holds the cars during assembly, starting with the interior and working outwards. These battery-operated platforms move from station to station and adjust ergonomically for heavy tasks, such as fitting large batteries or when fitting the body shell. Assembly of the Porsche 918 Spyder is based on the two-seater monocoque passenger cabin, and the scissor lift platforms allows the monocoque to be lifted, tilted, and rotated to provide the best angle for adding components with a minimum of struggle, such as when fitting the wiring harness.
Porsche says that this is especially important during the drivetrain assembly because it allows the connection of the electric motor and gearbox assembly to be positioned and bolted onto the monocoque with relative ease despite their weight.
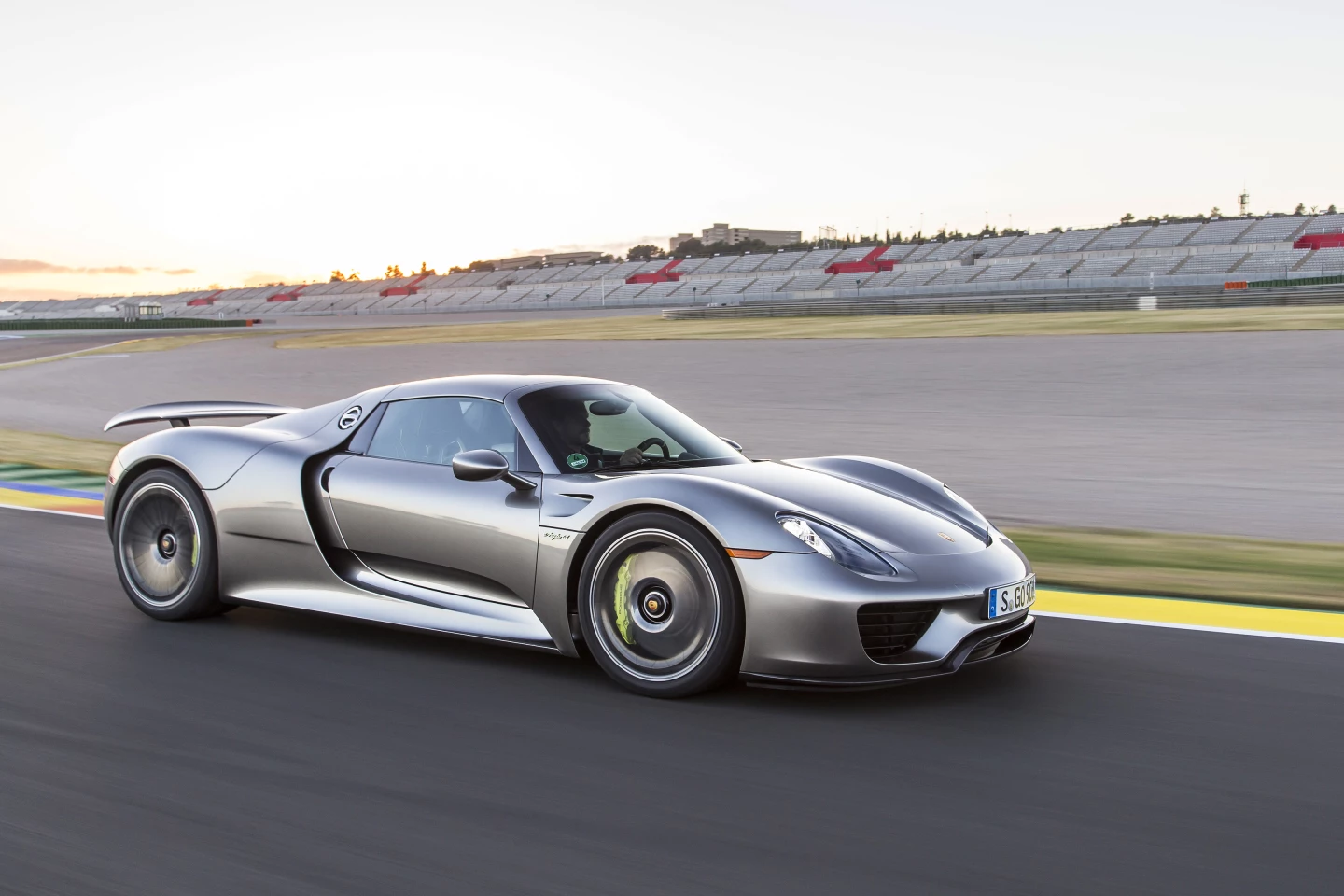
Another innovation is the Bluetooth-controlled cordless screwdrivers. These are cordless and wireless and virtually silent, which cuts down on factory noise and makes it easier to reach where needed. In addition, the screwdrivers are connected to a database that records the torque applied to all safety-specific screws, so they can be checked and corrected later if needs be. Porsche says that the new factory is exclusively cordless for all tools and platforms as a way maintain the floor's open plan, increase work flexibility, and reduce component damage.
According to the company, the Zuffenhausen location has an historic link to the 911 series, but it has many practical benefits. For one thing, it allows the 918 line to link with the 911 series' production "pearl chain," so the 918 line can draw on other facilities' experience and equipment during final assembly. In addition, the Zuffenhausen area provides the 918 line with an experienced labor pool that would otherwise be difficult to recruit.
Production of the 918 Spyder will continue until the middle of this year.
Source: Porsche