A Finnish research project has created a batch of single-cell protein using just electricity, water, carbon dioxide and microbes, in a small portable lab. While we're hesitant to call it "food" in its current state, the stuff is edible and nutritious enough to be used for cooking or livestock feed, and the team hopes that the system can eventually be used to grow food in areas where it's needed the most.
Agriculture isn't the most efficient of processes, requiring huge swathes of land, plenty of resources and an enormous environmental toll. And that's just to grow the food, let alone transporting it around the world. To help alleviate some of those issues and free up farmland for other purposes, the Food From Electricity study was launched in August last year, as a joint project between Lappeenranta University of Technology (LUT) and the VTT Technical Research Centre of Finland.
As the name suggests, the team is developing a way to create food from electricity – with the help of a few other resources, of course. The centerpiece of the system is a bioreactor, which contains water, microbes, and nutrients like nitrogen, sulfur and phosphorus. Carbon dioxide and an electrical current are pumped into the mix to kick things off.
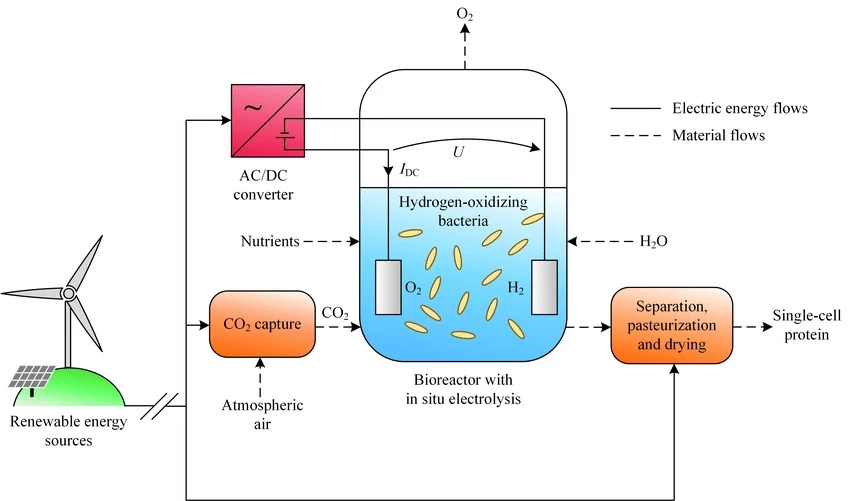
The electric current triggers electrolysis of the water, which produces hydrogen. Fed by the nutrients, the microbes then add oxygen to that hydrogen, and the end result of the chemical reaction is then separated and dried out into a powdery, edible, nutritious compound.
"In the long term, protein created with electricity is meant to be used in cooking and products as it is," says Juha-Pekka Pitkänen, Principal Scientist at VTT. "The mixture is very nutritious, with more than 50 per cent protein and 25 percent carbohydrates. The rest is fats and nucleic acids. The consistency of the final product can be modified by changing the organisms used in the production."
Currently, it takes about two weeks to produce one gram of protein, and the equipment to do so is about the size of a coffee cup. By scaling up the system, the researchers say their process should eventually be almost 10 times more energy efficient than photosynthesis, which is used to grow similar crops. And there are plenty of other environmental benefits as well.
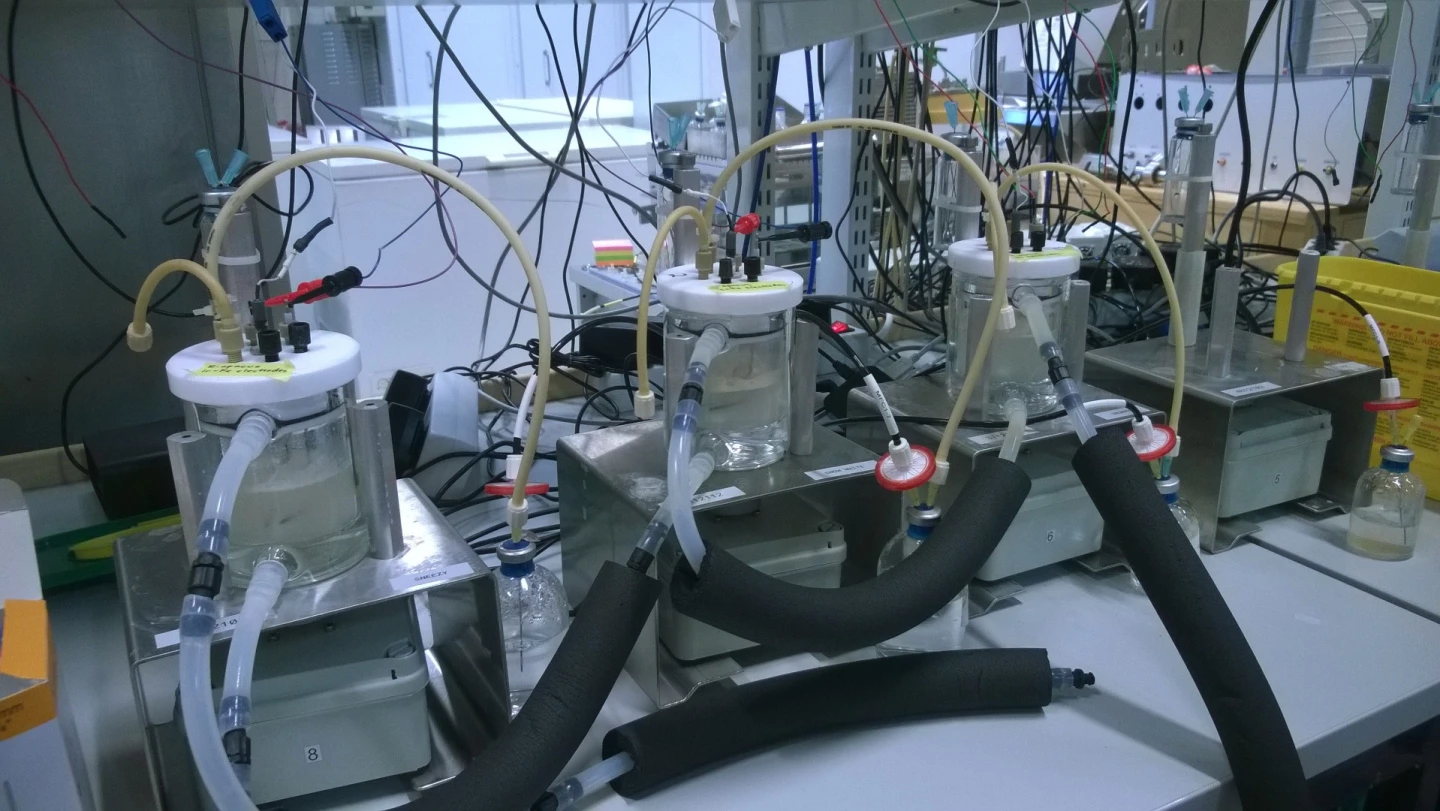
"Compared to traditional agriculture, the production method currently under development does not require a location with the conditions for agriculture, such as the right temperature, humidity or a certain soil type," says Jero Ahola, a Professor at LUT. "This allows us to use a completely automatized process to produce the animal feed required in a shipping container facility built on the farm. The method requires no pest-control substances. Only the required amount of fertilizer-like nutrients is used in the closed process. This allows us to avoid any environmental impacts, such as runoffs into water systems or the formation of powerful greenhouse gases."
The study will continue for another three years, and in that time the team plans to fine-tune the reactor, improve efficiency and develop the system for commercialization.