Everyone knows that the application of heat is necessary to boil water, but thanks to new research, much less heat may soon be required. A novel surface treatment allows water to reach a boiling point more easily, thus requiring less energy to do so.
As water in a pot or other container approaches the boiling point, numerous bubbles form along the bottom of that container. The greater the number of bubbles, the more efficient the boiling process, but only up to a point.
If the bubbles crowd one another to the extent that they coalesce into one continuous vapor film along the bottom, that film will slow the transfer of heat from the container's surface to the liquid water. As a result, it will take more time and energy to bring the water to a full boil.
Led by postdoctoral student Youngsup Song and Prof. Evelyn Wang, a team at MIT set out to maximize bubble formation while avoiding film formation. In order to do so, they created a treatment that can be applied to the bottom inner surface of containers used in the boiling of water. The treatment works in three ways.
First of all, it places an array of microscale dents in the surface. Measuring 10 micrometers wide and spaced about 2 mm apart, these dents serve as formation/anchoring points for the bubbles, keeping them held in place so they can't spread into one another.
Secondly, the surfaces of the dents are covered in nanoscale ridges. These structures increase the heated surface area, boosting the rate at which the liquid water evaporates into bubble-forming vapor.
Finally, each dent sits within the top its own individual tiny pillar. The pillars have a wicking effect, drawing water up to the dent where it continuously forms a layer of liquid between the boiling surface and the bubble. This increases boiling efficiency by ensuring that the surface is always heating liquid water, as opposed to passing heat through the vapor in the bubble.
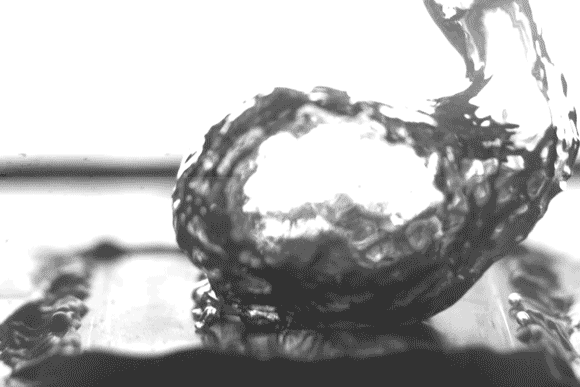
More research still needs to be conducted, as the current version of the technology has only been tested in small-scale setups. It is hoped that once developed further, however, the surface treatment could be used in applications such as the steam-powered generation of electricity, or the cooling of electronics. And yes, it might even decrease the amount of time that it takes to make a cup of tea.
A paper on the study was recently published in the journal Advanced Materials.
Source: MIT