Among the more than 8,000 lb (3,600 kg) of cargo that blasted off from Cape Canaveral on the 30th of January, bound for the International Space Station, were two firsts: the world’s first metal 3D printer designed especially for use in orbit and the first miniaturized surgical robot to be sent to the station.First metal 3D printer for space: Making life easier for astronauts
Developed by Airbus for the European Space Agency (ESA), the first metal 3D printer designed for use in space will soon be tested in the Columbus laboratory module aboard the International Space Station (ISS).
In addition to the plastic 3D printers already aboard the ISS, which astronauts use to replace or repair plastic parts, the metal printer is envisioned to manufacture items and parts that need to be made of something stronger.
“The metal 3D printer will bring new on-orbit manufacturing capabilities, including the possibility to produce load-bearing structural parts that are more resilient than a plastic equivalent,” said Gwenaëlle Aridon, Airbus Space Assembly lead engineer. “Astronauts will be able to directly manufacture tools such as wrenches or mounting interfaces that could connect several parts together. The flexibility and rapid availability of 3D printing will greatly improve astronauts’ autonomy.”
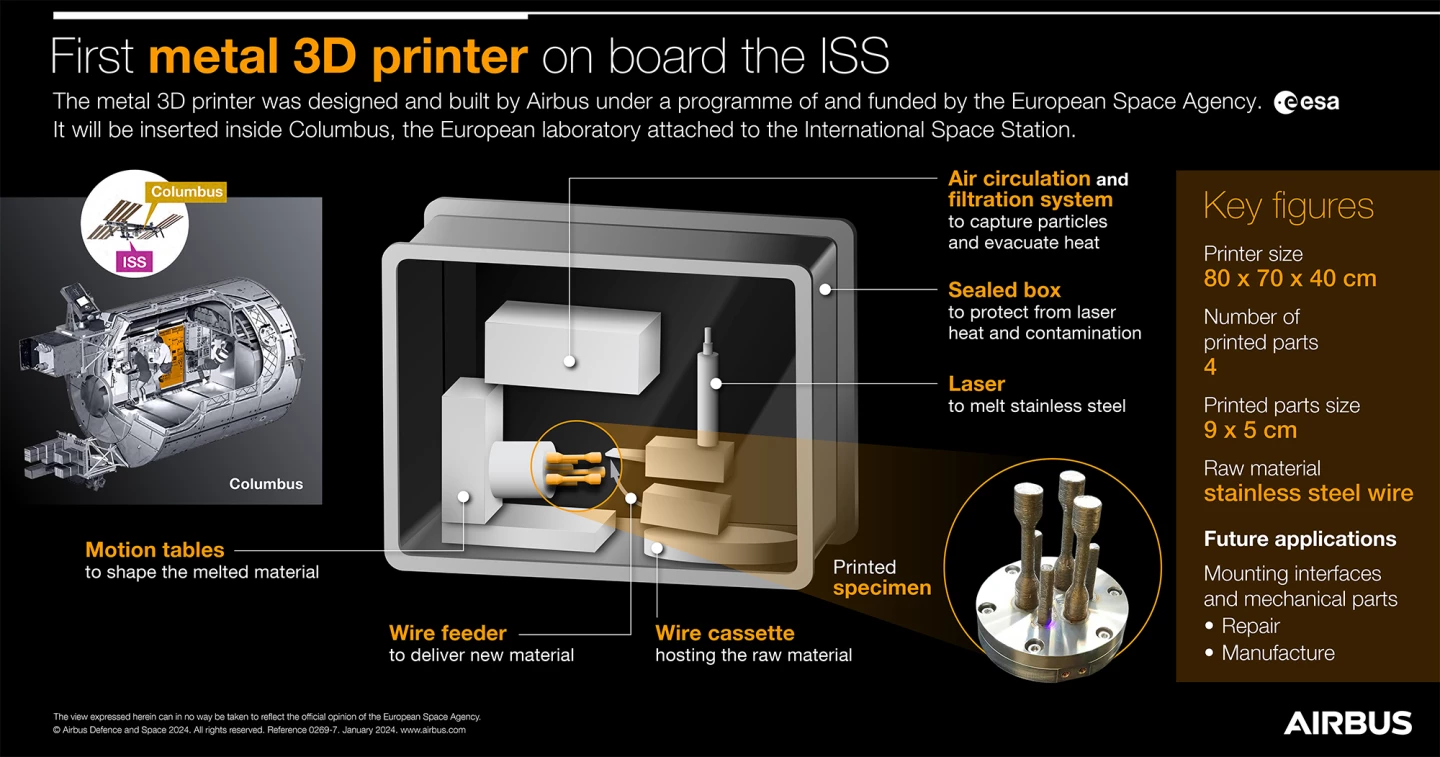
Its creators had to overcome several hurdles in getting the metal printer into space, which will sit inside a sealed metal box, similar to a safe.
“The first challenge with this technology demonstrator was size,” said Sébastien Girault, a metal 3D printer system engineer at Airbus. On Earth, current metal 3D printers are installed in a minimum 10-square-meter [108-sq-ft] laboratory. To create the prototype for the ISS, we had to shrink the printer to the size of a washing machine.”
Then there’s the issue of safety and protecting the ISS from the printer’s laser and the heat it generates. Compared to the melting point of plastic, which is around 200 °C (392 °F), the melting point of metal alloys compatible with the printing process can exceed 1,200 °C or 2,192 °F. And, whether using plastic or metal, emitted fumes need to be captured and filtered inside the machine so they don’t contaminate the air.
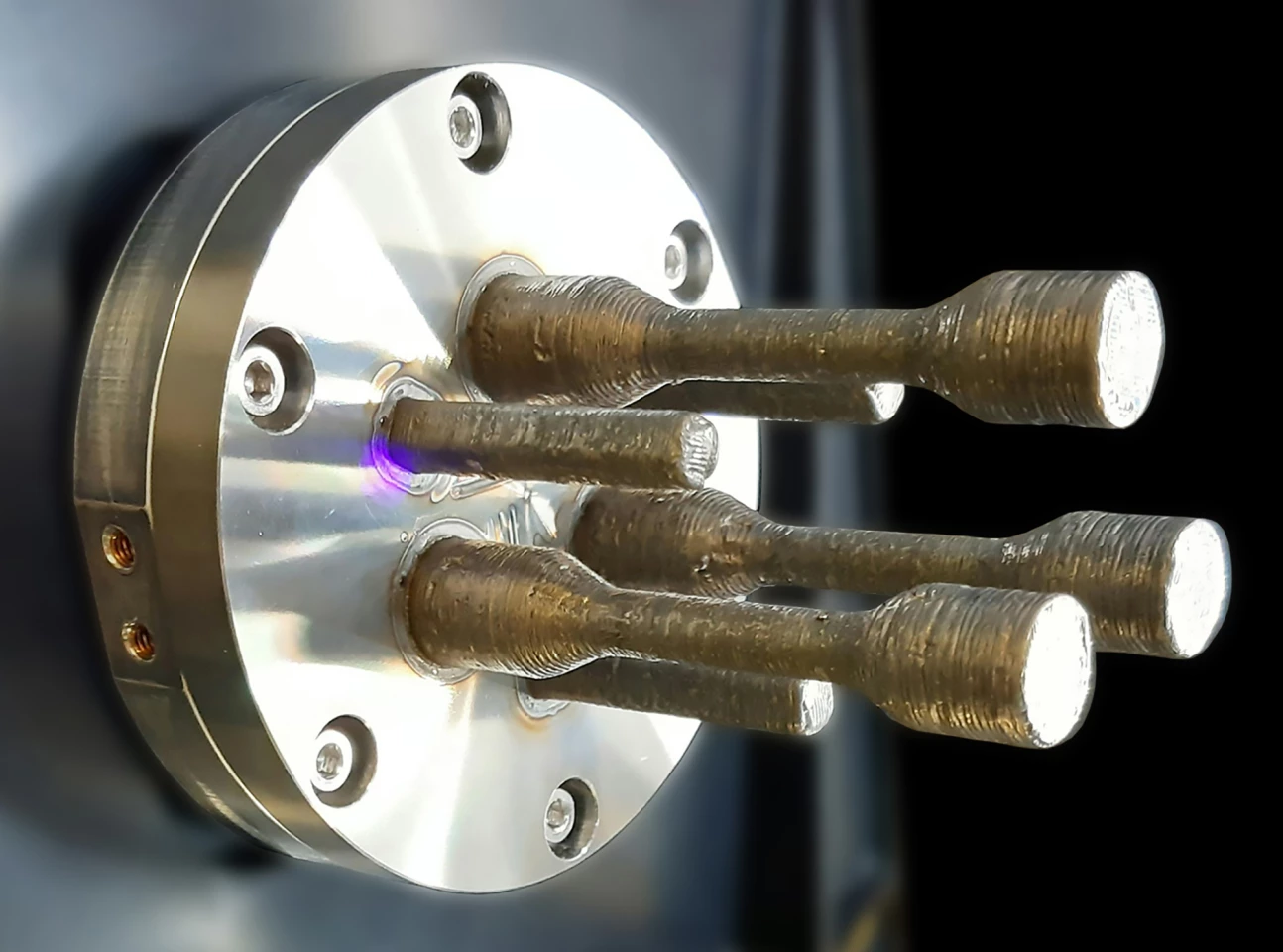
“Safety and contamination are key drivers for us not only for the ISS, but for future use on the Moon,” Aridon said.
Metal 3D printing on the space station will help scientists understand whether printing in orbit affects quality, placing us one step closer to preparing the technologies necessary for establishing a sustained presence on the Moon.
“Increasing the level of maturity and automation of additive manufacturing in space could be a game changer for supporting life beyond Earth,” said Aridon. “Thinking beyond the ISS, the applications could be amazing. Imagine a metal printer using transformed regolith [moondust] or recycled materials to build a lunar base!”
The ISS’ first surgical robot: Improving access to health in space and on Earth
The space-faring version of the ‘miniaturized in vivo robotic assistant’, or spaceMIRA, bound for the ISS will help identify the next steps in creating surgical technologies suitable for long-distance space travel. But it also has important implications down here on Earth.
“While space travel is exciting to think about, there is also an immediate need on Earth to help patients get the care they need,” said Shane Farritor, Professor of Engineering at the University of Nebraska-Lincoln and chief technology officer for Virtual Incision, a startup company he co-founded to bring MIRA to the commercial market.
Farritor is referring to the immediate need to ensure access to surgeons, particularly in rural and remote areas, including military battlefields, where there may be no doctors on hand.
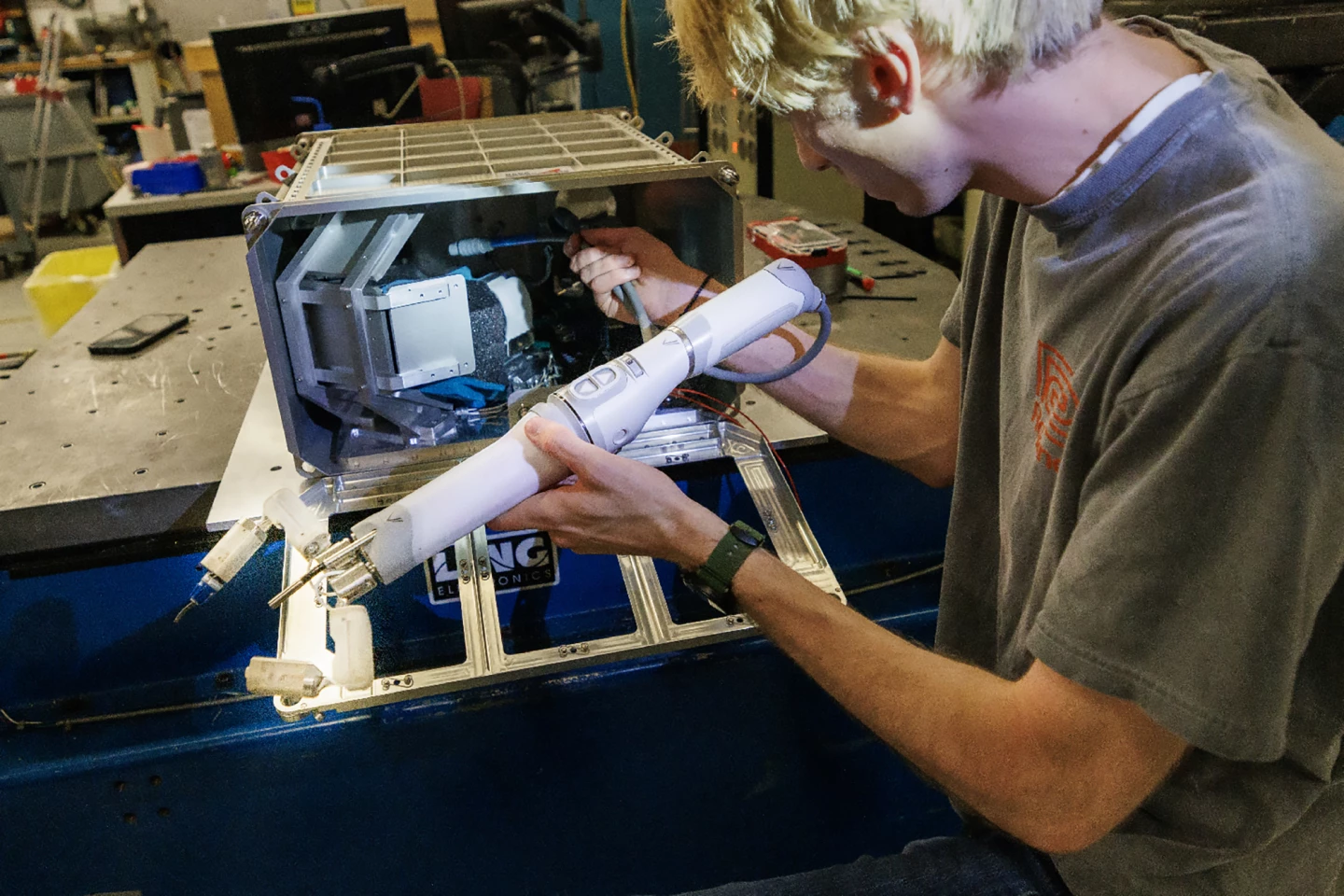
“Remote surgery has the potential to address these issues so patients can get the health care they need,” he said.
In the coming weeks, spaceMIRA will be guided remotely by a surgeon in Lincoln, Nebraska, and will use both of its ‘hands’ to perform a simulated surgical procedure. Working from within a locker the size of a microwave oven, the robot’s left arm will grasp while the right will cut, much like a human surgeon performing a tissue dissection in an operating room.
“The two-handed approach is critical in surgical procedures because local tension is key to determining the ideal locations to resect and to cut in the desired way,” Farritor said.
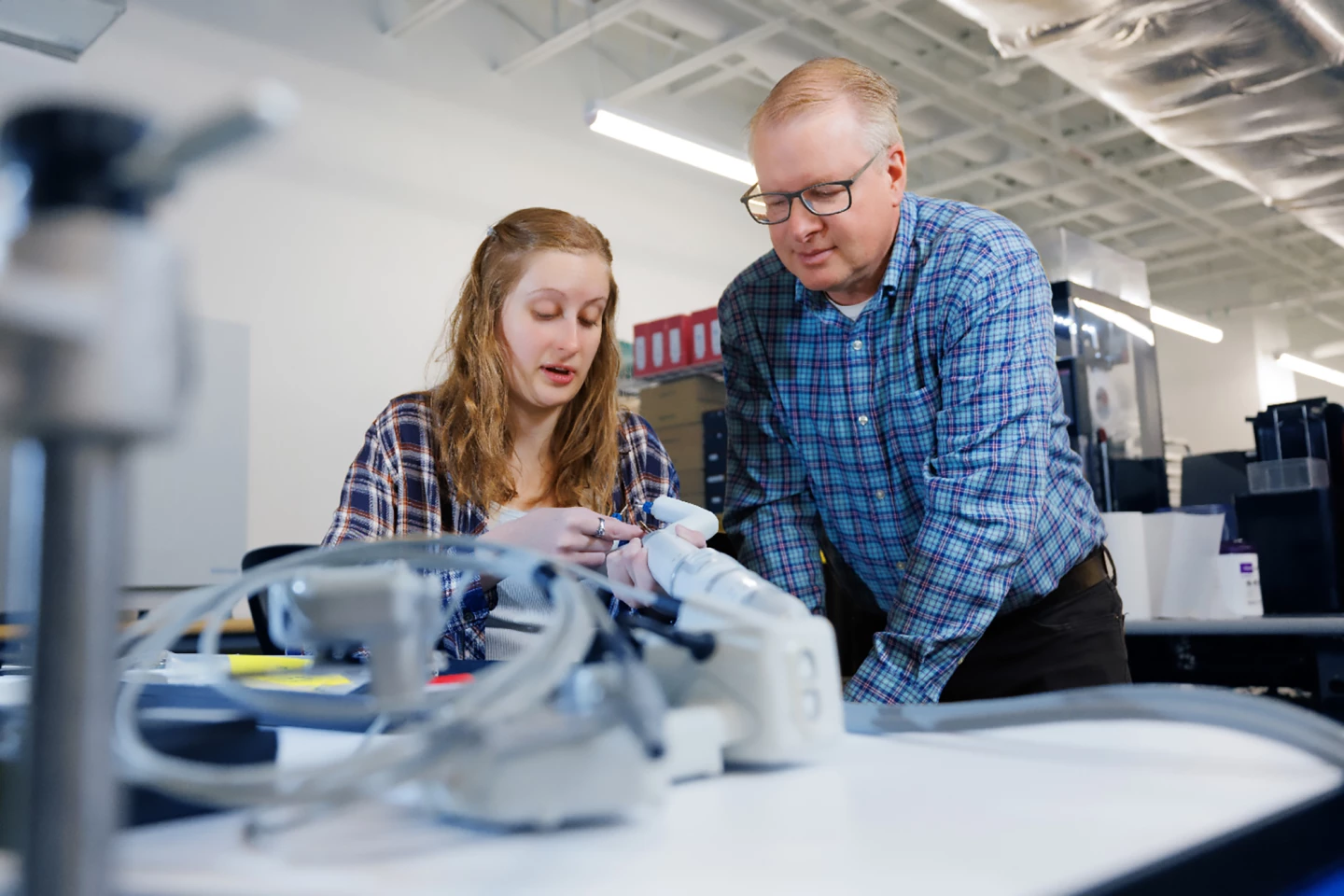
spaceMIRA was originally designed to perform surgery-like tasks autonomously, so the element of remote ground control adds an extra layer of difficulty. Of all the potential issues the robot faces, latency – the delay in a signal traveling from the Earth to the ISS and back – is the biggest. The signal needs to travel around 250 miles (402 km) one way, after all.
“There’s lots of obstacles,” said Farritor. “As we’ve learned recently, it can be hard to get the Zoom conference room to work right – let alone this.”
Farritor and his team will receive data about the robot’s performance during testing. spaceMIRA will return to Earth in a few months. The Northrop Grumman Cygnus spacecraft carrying spaceMIRA and the metal 3D printer is expected to arrive at the ISS on February 1st.
Sources: Airbus, University of Nebraska-Lincoln