Thinking big is apparently no challenge for architects Michael Hansmeyer and Benjamin Dillenburger. They've created a 3D printed room using algorithms to design its intricate cathedral-like interior. Assembled from 64 massive separate sandstone parts printed out with a huge 3D printer, the room contains 260 million surfaces printed at a resolution of a tenth of a millimeter. The 11-ton room took a month to print but only a day to assemble. The fabrication methods the duo used to print the room will, they believe, open the door to printing architecture, freeing architects to create new unimaginable buildings and also restore old ones.
Hansmeyer and Dillenburger, both computational architects at the Swiss Federal Institute of Technology's architecture department in Zurich, wrote algorithms to completely design the complex geometry of the 16 square meter (170 sq ft) room . Dubbed "Digital Grotesque," their modern take on a medieval grotto was made with a new type of 3D printed sandstone, infused with a hardening resin to increase its structural stability. To print out the sandstone parts that made the room, the duo used a massive Voxeljet 3D printer, about the size of a large room. "It can print a single piece that weighs 12 tons, yet at a layer resolution of 0.13 millimeters," says Hansmeyer. "This combination of scale and resolution seemed unreal to us at first."
The scale of machines, high material costs and the structural weakness of 3D printed materials is the reason why architects have up to now used 3D printing technology only to make prototypes or small scale models. The sand-printing technology the duo employed finds use in industrial applications, but with the addition of their innovative methods, it can now be used to create huge prefabricated sandstone bricks strong enough to build with.
"The limiting factor for the project was no longer the size of the printable space, but instead the logistics of how to transport and assemble such large elements," Hansmeyer tells us. "Otherwise, it would have been impossible to build the entire project out of just 64 printed pieces."
The weight of each of the 64 printed elements was reduced by making them hollow and using an internal structural grid to give them stability. Additional constructional details to help the bricks align with each other and to make the room to solid as a whole were directly integrated into the bricks and printed too."We added truncated cones to allow for stable stacking and ensure alignment, and we created horizontal shafts through the elements to facilitate transport," Hansmeyer told us. "There was no need to use a different material or a different system."
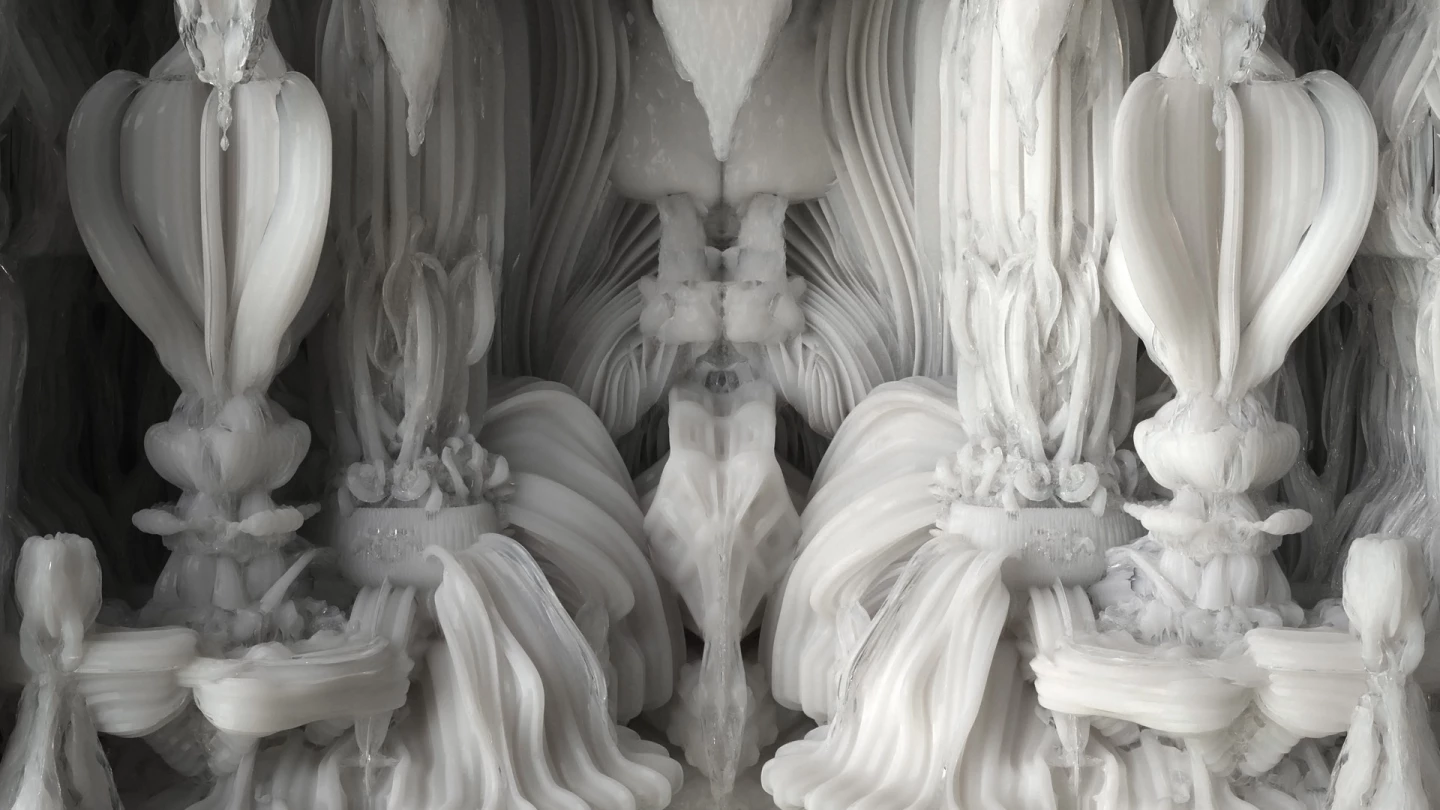
"No cost for ornament. No cost for individuality..."
Before he printed the room, Hansmeyer fabricated a series of columns out of plastic. As 3D printing technology hadn’t matured to its current level, these columns were materialized as layered models. Each column is made of 2,700 laser-cut slices, 1 mm thick, assembled on top of each other. The 3.2-m (10-ft) high room is their first architectural high-resolution 3D print using the sandstone printing process. Both the 3D printed columns and room are incredibly detailed containing millions of surfaces. "Architectural details can reach the threshold of human perception," says the Digital Grotesque website.
They're impossible to draw or construct by hand, which meets Hansmeyer's goal of creating entirely new structures that defy imagination using customized algorithms. "What kind of forms could we design if we could free ourselves from our experience, from our education," Hansmeyer asked the audience in his TED talk last year. "What would these unseen forms look like?"
Abstracting natural cell division processes, the algorithms they created fold the surfaces of a single cube repeatedly to create intricate buildable forms. It takes the computer about 35 seconds to create a structure with 16 million surfaces, evolving both the overall form and the microscopic detail. Since it wasn't possible for existing CAD software to process the grotto's geometry containing 260 million surfaces, specialized algorithms were developed to convert it into printable data that was streamed layer by layer to the 3D printer.
Hansmeyer believes that the additive manufacturing process will open up a new role for architects as designers of processes to create structures, instead of designing structures and think in terms of bits rather than bricks. The project Hansmeyer says held quite a few surprises.
"One of the most astounding things is that it costs exactly as much to 3D print a plain box as it does to print the most elaborate form conceivable," says Hansmeyer. "Not only are the costs identical, but the amount of time required is the same as well. And it doesn't cost more to print a different form each time i.e. there are no advantages to standardization. The implications of this are huge. There is no longer a cost for complexity. No cost for ornament. No cost for individuality."
The duo’s vision is to now 3D print an entire house. Digital Grotesque is currently on display at the FRAC Centre in Orléans, France.
Check out a video on Digital Grotesque below.
Source: Digital Grotesque via Beautifuldecay