Showing how far AI engineering has come, a new aerospike engine burning oxygen and kerosene capable of 1,100 lb (5,000 N) of thrust has successfully been hot-fired for 11 seconds. It was designed from front to back using an advanced Large Computational Engineering Model.
Designing and developing advanced aerospace engines is generally a complicated affair taking years of modeling, testing, revision, prototyping, rinsing and repeating. With their ability to discern patterns, carry out complex analysis, create virtual prototypes, and run models thousands of times, engineering AIs are altering the aerospace industry in some surprising ways – provided, of course, they are properly programmed and trained.
Otherwise, it's garbage in, garbage out, which has been the Golden Rule of computers since they ran on radio valves and electromechanical relays.
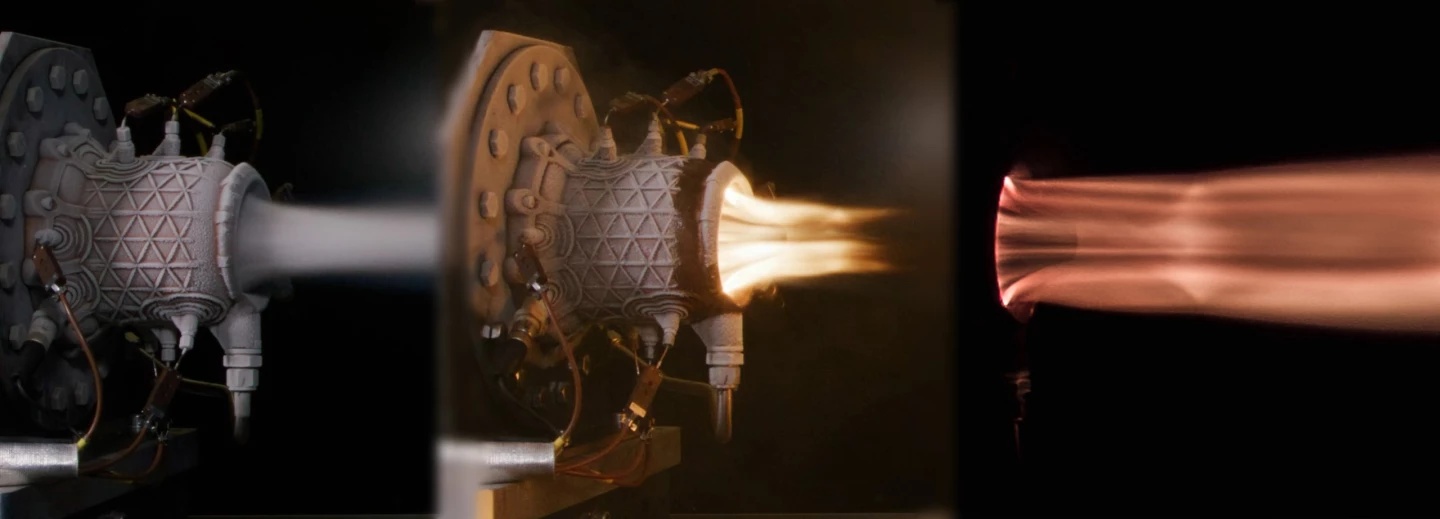
Dubai-based LEAP 71 is demonstrating what modern engineering AI can do by applying it to the problem of one of the more outré rocket engine designs – the aerospike.
Conventional rockets use the familiar bell to direct and expand the hot gases coming from the engine after passing through the Venturi nozzle. This design works very well, but it has one major disadvantage. The curve of the bell has to be custom designed to efficiently operate at a particular altitude, so a rocket that works very well on liftoff will work less well as it rises in the atmosphere and the air pressure decreases. This is why second- and third-stage rocket engines are different from those of the first stage.
Ideally, engineers want an engine that can adjust itself automatically to changes in air pressure. An aerospike does this by shaping the engine into a spike or plug with a curve like that of the inside of a rocket bell. As the combustion gases flow from the engine over the spike, the curve acts as one side of the bell and the surrounding air as the outside curve. As the air pressure changes, so does the shape of the virtual bell.
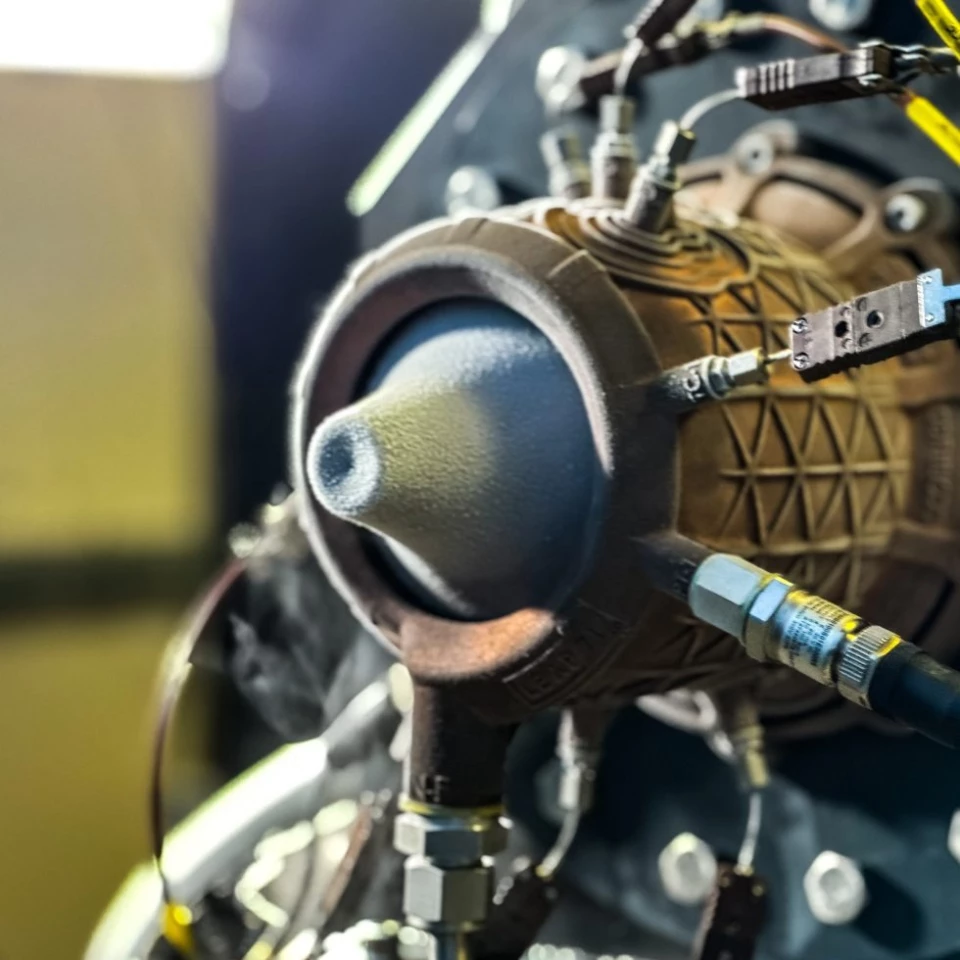
There have been a number of aerospike engines developed since the 1950s and one has actually gone airborne, but there's still a long way to go when it comes to turning a promising idea into a practical space engine.
LEAP 71's contribution to the effort is to apply its Noyron Large Computational Engineering Model to the problem. It's an AI programmed and trained by aerospace experts to take a given set of input parameters and use them to create a design that meets those parameters by inferring physical interactions of various factors, including thermal behaviors and projected performance.
The results of this are then fed back into the AI model to fine tune it as it presents computed performance parameters, the geometry of the engine, the parameters of the manufacturing process, and other details.
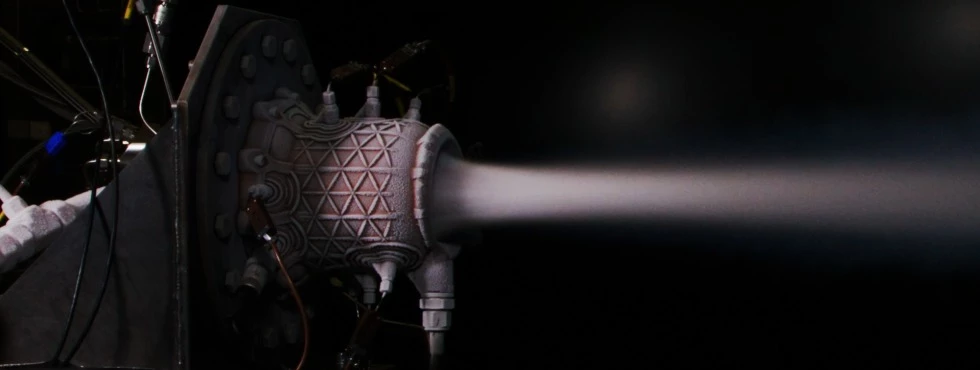
According to the company, Noyron was able to autonomously design the new aerospike in about three weeks. It was then fabricated as a solid block of copper using Selective Laser Melting industrial 3D printing technology before going to the test phase. On December 18th, 2024, it succeeded on the first test firing where it was subjected to gas temperatures of 3.500 °C (6,300 °F).
The exercise was part of a four-engines-in-four-days campaign by LEAP 71 at Airborne Engineering in Aylesbury, England.
"We were able to extend Noyron’s physics to deal with the unique complexity of this engine type," said Josefine Lissner, CEO and Co-Founder of LEAP 71. "The spike is cooled by intricate cooling channels flooded by cryogenic oxygen, whereas the outside of the chamber is cooled by the kerosene fuel. I am very encouraged by the results of this test, as virtually everything on the engine was novel and untested. It’s a great validation of our physics-driven approach to computational AI."
Source: LEAP 71