Researchers at Purdue University in the U.S. have developed a new method of harvesting vast amounts of energy from waste heat. Using glass fibers dipped in a solution containing nanocrystals of lead telluride, the team led by Dr. Yue Wu is engineering a highly flexible thermoelectric system that generates electricity by gathering heat from water pipes and engine components.
Harvesting the energy of waste heat is by no means a new idea - we've seen it implemented in aircraft sensors, camping cookware, even rubber boots.
The new Purdue system seeks to avoid many of the limitations that has hindered similar attempts in the past: it is less bulky, uses less toxic material, and could potentially be applied on a mass scale.
Using glass fibers coated by nanocrystals, Wu's team has engineered a promising new thermoelectric system that is best suited for use with power plants and car exhausts. It is scalable, eco-friendly, has comparatively low production costs and lends itself well to being mass-produced. When heated on one side, the electrons in a thermoelectric material migrate to the opposite, cooler side. This generates an electrical current which can then be channeled into the main grid. The net result is higher energy efficiency, less emissions, and a shrinking electric bill.
Although researchers have already created high-performance materials of this kind, these tend to be quite brittle and unable to conform to the bends along the pipes with which they are intended to operate. They are also manufactured using large quantities of materials which are either toxic or hard to come by.
Wu's solution was to dip glass fibers in a solution containing nanocrystals of lead telluride and then expose the fibers to heat, fusing the crystals together. The flexible fibers can easily follow the bends of water pipes and, by minimizing the use of expensive tellurium to a mere 300-nanometer-thick coating, the production costs fall dramatically.
The concept was demonstrated using a system containing tubes of differing diameters nested inside a larger tube. Hot water flows through a central tube and cooler water flows through an outer tube, with a layer of thermoelectric material between the two.
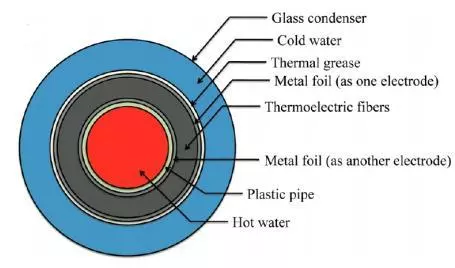
The researchers believe the system has applications in power plants, car engines and residential heating. These are areas where energy waste through heat is a big issue - for example research from the Lawrence Livermore National Lab shows that between 2008 and 2010, 57.3 to 57.8 percent of the total energy generated in the United States was rejected into the environment, the majority of which was dispersed as heat, with the main culprits being power plants and the automotive industry.
"If we could get just 10 percent back that would allow us to reduce energy consumption and power plant emissions considerably," Dr. Wu commented.
So how much energy can be harvested using the Purdue system?
"For those familiar with the thermodynamics of heat engines, the efficiency of a thermoelectric device made from our nanocrystal-coated fibers would be ~11 percent of the Carnot efficiency," Dr. Wu told Gizmag. "Considering some recent tests on a Chevy Suburban, a vehicle equipped with a thermoelectric device that uses our fibers would see a ~3.6 percent improvement in mpg due to the thermoelectric generator supplying 250-440 W of power. We have not looked into precise numbers regarding co-generation of electricity during residential heating."
There are still degradation issues that need to be ironed out however. "We suspect the cracking of the coated film on the glass fibers upon bending is the cause of the degradation, and we are working on the issue," says Dr. Wu. "The future steps will include improving the coating quality, exploring better coating 'ink', developing power generation modules based on flexible fibers and testing their efficiency."
And the future might even bring some quite unexpected applications. Besides generating electricity when exposed to heat, in fact, the material can also work in reverse, absorbing heat whenever an electrical current is applied. This means that the fibers might one day be woven into clothing, or used in solid-state cooling devices.
The findings were detailed in a research paper appearing last month in the journal Nano Letters. The work is being funded by the National Science Foundation and the U.S. Department of Energy.
Researchers at Purdue University in the U.S. have developed a new method of harvesting vast amounts of energy from waste heat. Using glass fibers dipped in a solution containing nanocrystals of lead telluride, the team led by Dr. Yue Wu is engineering a highly flexible thermoelectric system that generates electricity by gathering heat from water pipes and engine components.
Harvesting the energy of waste heat is by no means a new idea - we've seen it implemented in aircraft sensors, camping cookware, even rubber boots.
The new Purdue system seeks to avoid many of the limitations that has hindered similar attempts in the past: it is less bulky, uses less toxic material, and could potentially be applied on a mass scale.
Using glass fibers coated by nanocrystals, Wu's team has engineered a promising new thermoelectric system that is best suited for use with power plants and car exhausts. It is scalable, eco-friendly, has comparatively low production costs and lends itself well to being mass-produced. When heated on one side, the electrons in a thermoelectric material migrate to the opposite, cooler side. This generates an electrical current which can then be channeled into the main grid. The net result is higher energy efficiency, less emissions, and a shrinking electric bill.
Although researchers have already created high-performance materials of this kind, these tend to be quite brittle and unable to conform to the bends along the pipes with which they are intended to operate. They are also manufactured using large quantities of materials which are either toxic or hard to come by.
Wu's solution was to dip glass fibers in a solution containing nanocrystals of lead telluride and then expose the fibers to heat, fusing the crystals together. The flexible fibers can easily follow the bends of water pipes and, by minimizing the use of expensive tellurium to a mere 300-nanometer-thick coating, the production costs fall dramatically.
The concept was demonstrated using a system containing tubes of differing diameters nested inside a larger tube. Hot water flows through a central tube and cooler water flows through an outer tube, with a layer of thermoelectric material between the two.
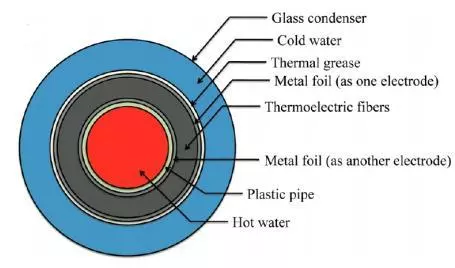
The researchers believe the system has applications in power plants, car engines and residential heating. These are areas where energy waste through heat is a big issue - for example research from the Lawrence Livermore National Lab shows that between 2008 and 2010, 57.3 to 57.8 percent of the total energy generated in the United States was rejected into the environment, the majority of which was dispersed as heat, with the main culprits being power plants and the automotive industry.
"If we could get just 10 percent back that would allow us to reduce energy consumption and power plant emissions considerably," Dr. Wu commented.
So how much energy can be harvested using the Purdue system?
"For those familiar with the thermodynamics of heat engines, the efficiency of a thermoelectric device made from our nanocrystal-coated fibers would be ~11 percent of the Carnot efficiency," Dr. Wu told Gizmag. "Considering some recent tests on a Chevy Suburban, a vehicle equipped with a thermoelectric device that uses our fibers would see a ~3.6 percent improvement in mpg due to the thermoelectric generator supplying 250-440 W of power. We have not looked into precise numbers regarding co-generation of electricity during residential heating."
There are still degradation issues that need to be ironed out however. "We suspect the cracking of the coated film on the glass fibers upon bending is the cause of the degradation, and we are working on the issue," says Dr. Wu. "The future steps will include improving the coating quality, exploring better coating 'ink', developing power generation modules based on flexible fibers and testing their efficiency."
And the future might even bring some quite unexpected applications. Besides generating electricity when exposed to heat, in fact, the material can also work in reverse, absorbing heat whenever an electrical current is applied. This means that the fibers might one day be woven into clothing, or used in solid-state cooling devices.
The findings were detailed in a research paper appearing last month in the journal Nano Letters. The work is being funded by the National Science Foundation and the U.S. Department of Energy.