For automobile manufacturers, the electric elephant in the room continues to be bulky and weighty battery packs. This week, Volvo unveiled an innovative potential solution to the problem that it has been working on for the past three and a half years with other European partners; replace steel body panels with carbon fiber composite panels infused with nano-batteries and super capacitors.
The conductive material used around the vehicle to charge and store energy can be recharged via the vehicle’s regenerative braking system or via the grid. When the system and motor requires a charge, the energized panels behave like any traditional battery pack and discharge accordingly. According to Volvo, the material charges and stores faster than a typical system.
Using a Volvo S80 as a test platform, the team replaced the vehicle’s trunk lid and plenum cross member over the engine bay with the new material. Volvo claims the composite trunk lid, which is stronger than the outgoing steel component, could not only power the vehicle's 12 volt system but the weight savings alone could increase an EV's overall range and performance as a result.
Under the hood, Volvo wanted to show that the plenum replacement bar is not only capable of replacing a 12 volt system but is also 50 percent lighter than the standard steel cross-member and torsionally stronger. The very much revolutionary concept, chock full of cost and engineering challenges, presents an interesting solution that could not only reduce overall weight but increase charge capacity relative to a vehicle’s surface area.
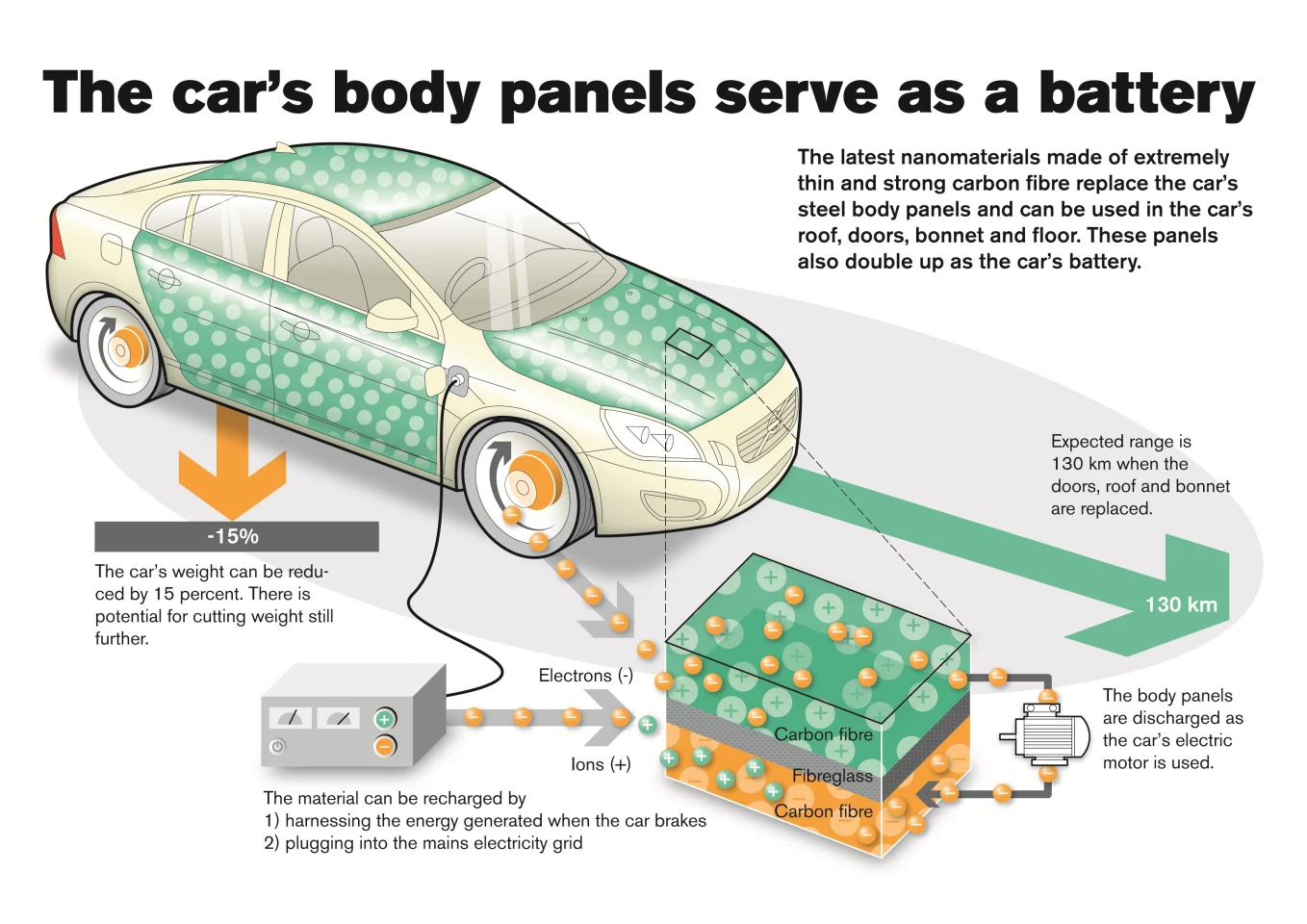
When it comes to weight savings, the battery pack in Tesla’s Model S for example, not only adds significant cost but also brings with it over 1,000 lb (453 kg), making the electric argument a difficult one for many. With Volvo’s concept, that huge chunk of weight would not only be lighter under this scenario, but would be spread out evenly over a vehicle’s body. In theory, vehicle handling and performance characteristics would thus improve as a result of this revised displacement idea.
But the idea of using body panels as battery packs does come with its share of particular concerns. Lamborghini, McLaren and Pagani charge a hyper-premium for their exotics as a result of extensive carbon fiber use, so for this idea to become reality and make it to mass production would require a significant reduction in the cost of carbon fiber.
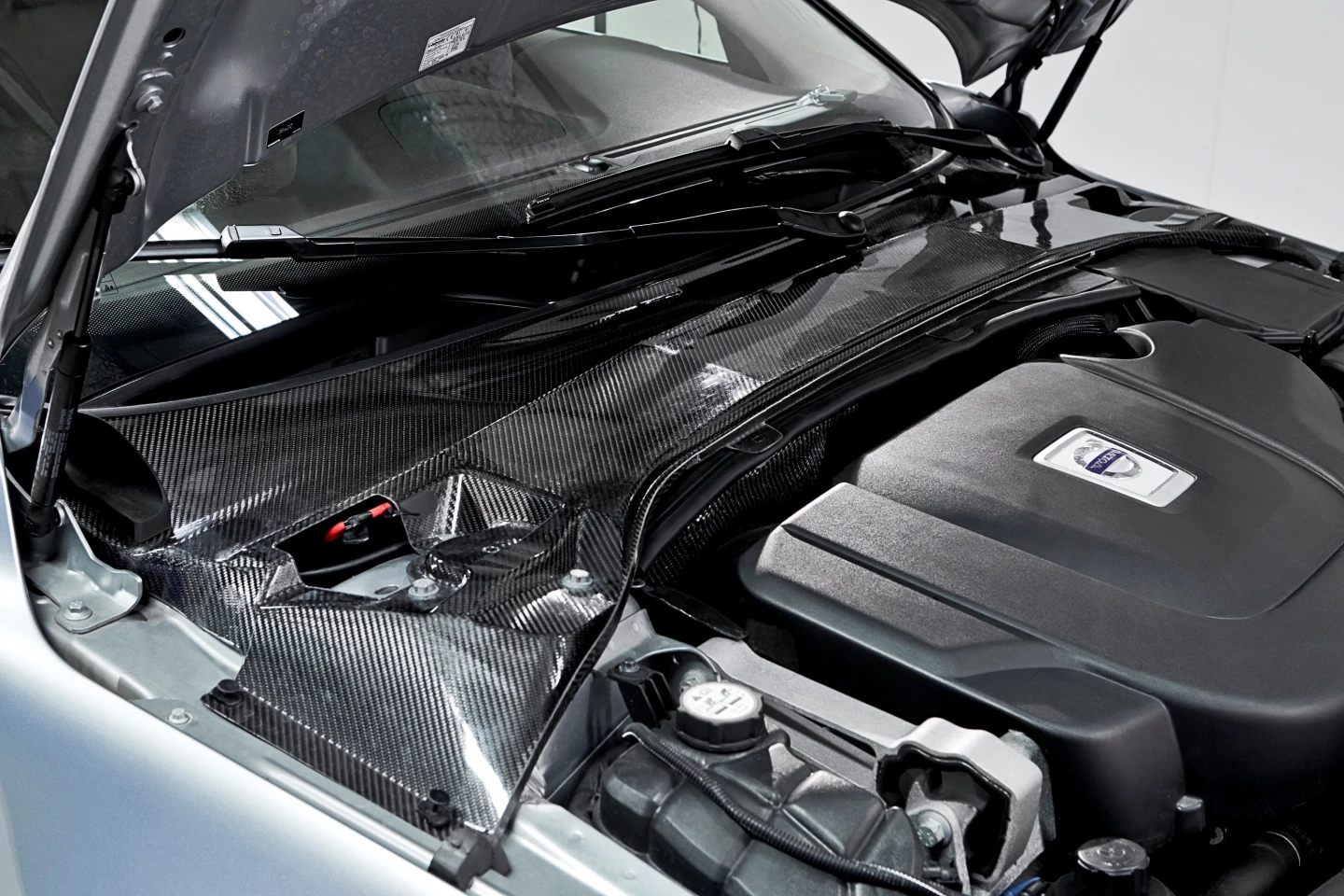
Then there’s the issue of broken panels or those damaged in an accident. In the event of an accident not only would body panels be extremely costly to replace but they could present unprecedented problems for emergency crews. Electrical surges coming from broken body panels could be potentially harmful were rescue persons unaware of the underlying electrical issues.
On a fossil fuel-powered note, cars using traditional 12 volt batteries, which weigh anywhere from 45 - 61 lb (20-28 kg), this technology could also prove beneficial by relocating that hefty chunk of lead from the nose of the car out across larger surface areas.
According to Volvo, weight savings of 15 percent or more could be achieved by replacing a vehicle’s traditional body and relevant electrical components with these new nano-infused carbon fiber panels. Volvo is also keen to point out the positive sustainability aspect that comes as a result of such weight reduction.
Source: Volvo