Oak Ridge National Laboratory (ORNL) is no stranger to impressive 3D printing feats, with a replica 1965 Shelby Cobra and a dwelling and vehicle which can power each other, already under its belt. Now a new plane wing trim-and-drill tool developed and 3D printed by ORNL has been certified by Guinness World Records as the largest solid 3D printed item.
Made from carbon fiber and ABS thermoplastic composite materials, the new tool measures 17.5 x 5.5 x 1.5 ft (5.3 x 1.7 x 0.5 m) and weighs around 1,650 lb (748 kg). To meet the requirements of the record, the item needed to be one solid piece of 10.6 cubic ft (0.3 cubic m), which a Guinness World Records judge confirmed at a ceremony.
"The recognition by Guinness World Records draws attention to the advances we're making in large-scale additive manufacturing composites research," says Vlastimil Kunc, leader of an ORNL team. "Using 3D printing, we could design the tool with less material and without compromising its function."
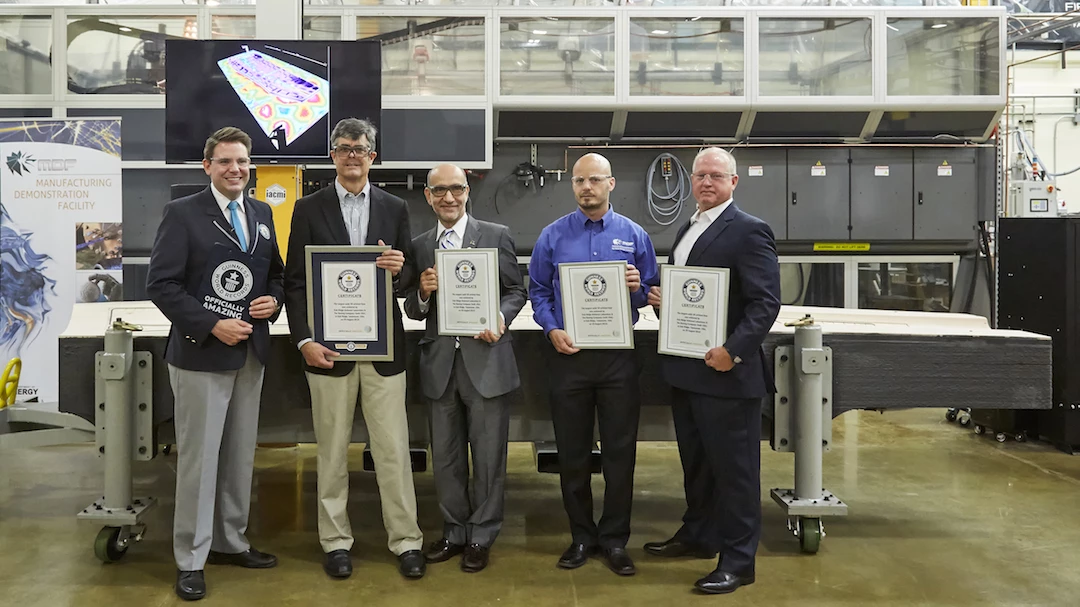
Of course, the tool wasn't designed just for world record glory: printable in just 30 hours, it's an impressive time and cost saver, considering the existing metal version currently takes about three months to manufacture.
"Additively manufactured tools, such as the 777X wing trim tool, will save energy, time, labor and production cost and are part of our overall strategy to apply 3D printing technology in key production areas," says Leo Christodoulou, Boeing's director of structures and materials.
As Christodoulou mentions, the trim-and-drill tool will be used in a new Boeing factory in St. Louis, put to work on the unique wings of the upcoming 777X airliners, which are due to begin production next year. The company will provide feedback to ORNL on how well the tool performs over time.
Source: Oak Ridge National Laboratory