Researchers from North Carolina State University have developed a new technique for transforming two-dimensional print output into 3-D structures, using nothing but light. A pre-stressed polymer sheet is fed into a conventional inkjet printer, which applies black stripes to areas designed to be used as hinges. The desired pattern is then cut out and subjected to infrared light. The material contracts at the hinges, and the sheet collapses into a predefined 3D structure. Dr. Michael Dickey, who co-authored a paper describing the research, says the process could be used for packaging purposes and could be applied to high-volume manufacturing.
The idea is based on a remarkably simple principle. The printed-on black stripes absorb more energy that the remaining part of the polymer sheet, so the contraction manifests itself exactly where it's needed, which is at the hinges. What is more, the technique uses existing materials and is compatible with widely used commercial printing methods, such as roll-to-roll printing or screen printing. Three-dimensional objects, such as cubes or pyramids, can now be printed using techniques that are inherently two-dimensional.
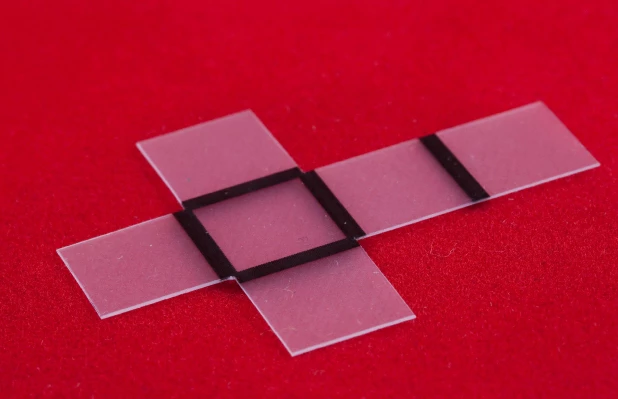
It is possible to vary the extent to which a hinge folds by changing the width of the black stripe. The wider the hinge, the further it folds, e.g. 90 degrees for a cube and 120 degrees for a pyramid. Also, wider hinges fold quicker, as the energy-absorbing area is larger. By patterning the lines on either side of the material, the researchers can decide which direction the hinges should fold, so the resulting structures can be pretty complex.
A computer model of the process shows that the surface temperature of the hinge must be higher than the glass transition temperature of the material used (i.e. the temperature at which the material changes its behavior and becomes flexible). Another important finding is that the heating needs to be targeted at the hinges, and not at the whole sheet, for the folding to take place.
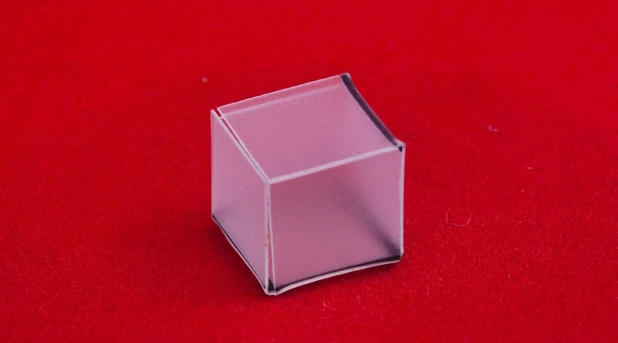
The work is described in a paper recently published in the journal Soft Matter. See the video below for a presentation of the process.
Source: North Carolina State University