Additive metal manufacturing can be done in a number of ways, but the idea is generally the same: you run a big printer that deposits molten metal in layers onto a substrate that then fuse together into a solid shape. By printing from the ground up, you can create shapes that are impossible to make with traditional subtractive manufacturing, and while it's too slow and fiddly for mass manufacture, it's an incredibly fast and effective technique for small-run parts and rapid prototyping.
Many of today's metal-printing systems use lasers to heat and melt powdered metal feedstocks. Rosotics founder and CEO Christian LaRosa says there are a number of problems inherent in laser systems. Firstly, those powdered metal feedstocks are expensive and frequently hazardous – for example, powdered titanium is explosive. Secondly, the lasers are an inefficient means by which to translate power into heat. Large-scale laser-based systems can require special energy supply systems.
Thirdly, they can be dangerous – even a reflected beam of that kind of power can be enough to blind someone if it hits them directly in the eye. And fourthly, parts created by these methods typically need to be heat-treated afterwards, meaning that you can only print parts as big as the oven you can bake them in afterwards.
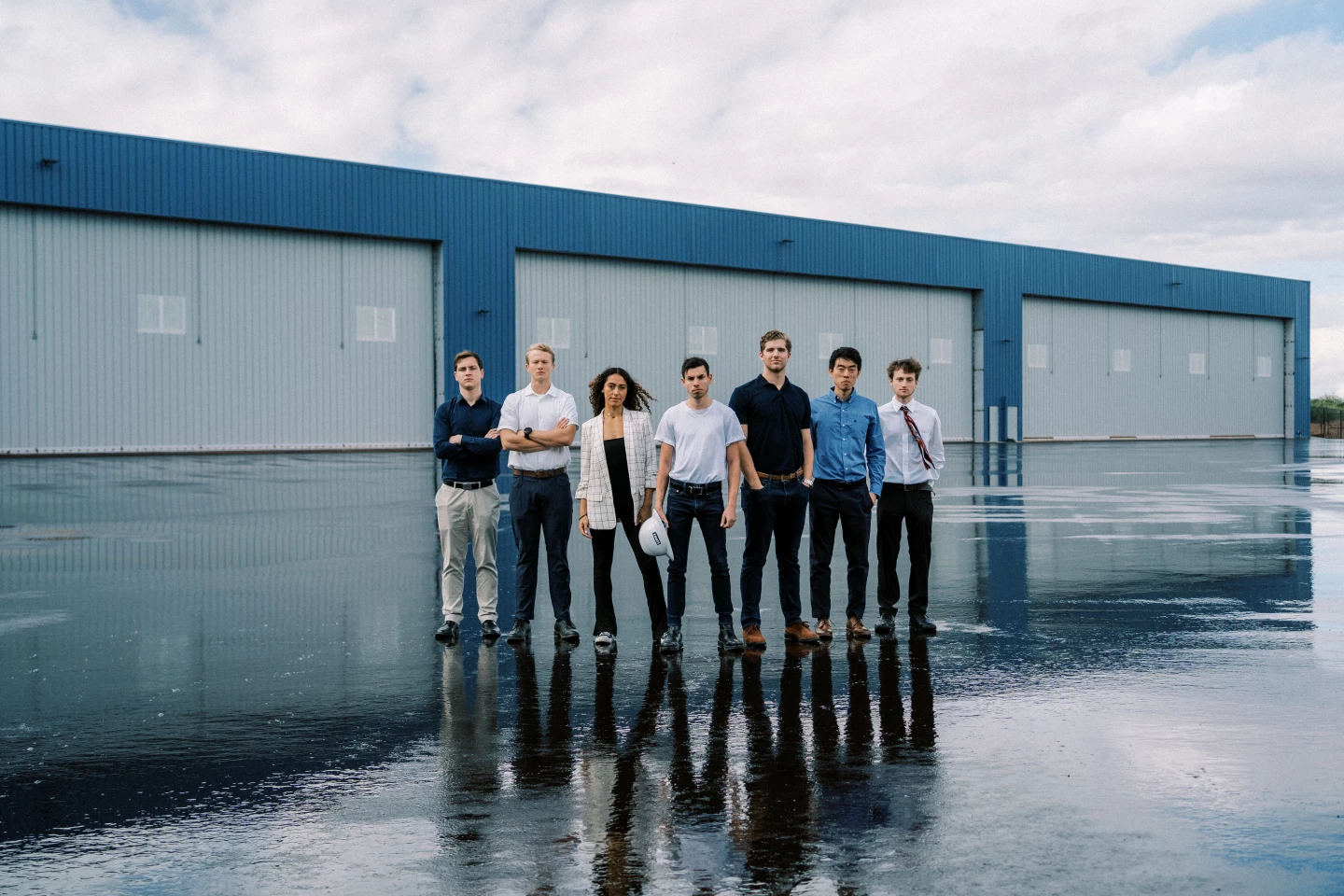
LaRosa says he's come up with an alternative that addresses all these issues, and opens the door for cheap, easy and fast printing of huge metal parts, big enough for structural use in aircraft and rockets. Rosotics has designed, built and tested a new type of metal 3D printing head, called the Mantis, that delivers heat to the metal highly efficiently, through induction.
"It's a very natural way of 3D printing a metal, in my opinion," LaRosa tells us over a video call. "You generate an electromagnetic field from a coil, and any ferromagnetic metal that passes through that field is heated inductively, by the eddy currents you're inducing in the metal. We remove the laser from the process; we simply feed wire through a nozzle, and inductively heat it as it's passing through. We call it Rapid Induction Printing, or RIP. It gets you to the same goal with far less energy loss."
How much more efficient is the process? "Efficiency in a laser based process is, in many ways, quite abysmal," says LaRosa. "It's an optical means of transferring heat. Moving to an induction process, you're ramping up the efficiency quite heavily. Compared to directed energy deposition, the laser-based wire-feed approach, we're looking at 30-50% more efficient on the total energy spent. Compared to others, it can be nearly an order of magnitude."
The feedstock doesn't have to be ferromagnetic, either. "Aluminum was a big target for us to hit, because it forms the basis for a lot of structural parts in aerospace, and it's not magnetic in the slightest," says LaRosa. "So we found unique ways to inductively heat that feedstock that utilize breakthrough approaches in metallurgical science. You can inductively heat a jacket of inductive material, or you can have the target feedstock traveling through an inductively heated channel that delivers heat through physical contact."
This opens the process up to a wide range of metals. The company has tested extensively with steel and aluminum thus far, but LaRosa says it should be able to handle most metals: "From what we've seen, the materials widely used in aerospace and the niches we're targeting, it can handle them pretty comprehensively," he says. "There are likely many materials that'll push the limits, but even then, we've got room to change the process and probably tackle those as well. Titanium is a pretty workable material, but there's a number of others we're examining. One of the most immediate ones is cupronickel, which has very good mechanical performance in certain uses. But overall, the process performs fairly well with any material that's commercially available in wire form."
The printer currently handles wires between 1-10 mm in diameter, but LaRosa says that can easily scale upwards if necessary, simply by widening the nozzles.
Rosotics has built a prototype – in considerable style. "There's a full scale printer prototype behind the wall on my side here," says LaRosa, "that prints to about 26 feet (8 m) in width, and about 20 feet (6.1 m) in height. That machine is running three heads, each pushing a little over 15 kg (33 lb) of metal an hour. As a system, it's putting down about 50 kg (110 lb) an hour. It's running off a 240-volt outlet like you'd find in any typical warehouse environment – if you were running a large-scale wire-based laser printer, you'd probably be looking at contacting the power company to get a bigger link to the grid. I think that speaks volumes; when you make the process more efficient, the entire picture simplifies.
"Our process works in open air, too," he continues, "so you don't have to contain your whole print volume in a vacuum chamber. And with other laser-based processes, you need to heat the entire structure uniformly, to reduce the residual stresses the process has induced. We don't have to do that kind of an operation post-print. That simplifies the operation even further. And when you get to large scale, there might be a handful of furnaces for heat treatment at that size in the entire United States."
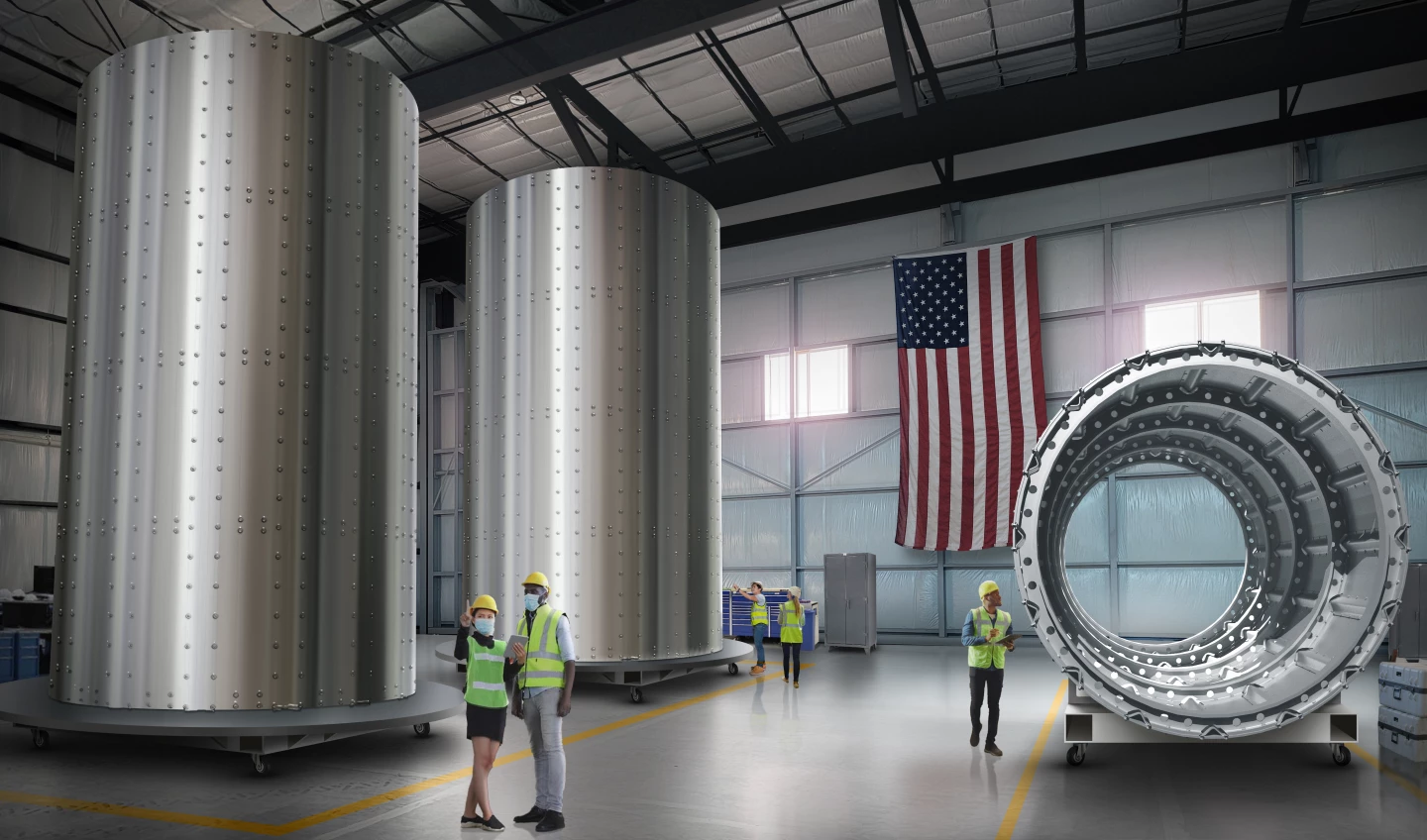
The RIP process is claimed to make the entire process much faster and cheaper, and open metal printing up to virtually limitless scale. "A lot of the reason we got started," says LaRosa, "is that 3D printing has revolutionized manufacturing and how parts are made – but it's limited by size. Heavy industry has been locked out from using 3D printing in the areas you really want to be applying it – really large parts made in small numbers. That's why we exist. I was a 20, 21-year old kid working in the design and production of rocket structures, and I was pained by the fact that we couldn't use 3D printing at that scale. I'm sure may others in aerospace have had the same feeling.
"I'm an engineer by education, by training and by practice," he says, "I'm a founder by necessity – the necessity to overcome this limitation in 3D printing. When it became apparent that this process could to that, I couldn't sleep at night until it existed. I wasn't entirely confident right off the bat, but as I started pitching it to people higher and higher up the chain, even in NASA's ecosystem, and found that the process would perform as expected, that was the point where I had to go full time and make this thing a reality. And every day now, I'm progressively more humbled, seeing the process – not just in simulation, but in reality, doing what we expect it to. We're really excited to get it onto the market for customers.
"Our system is very well suited for structural applications, say the structure of a rocket, or the structure of a tank," he continues. "Any kind of structural part that aerospace would demand, our system can do it. But it's designed to branch out to heavy industry at large. Energy, marine construction, we can serve these applications very well."
For anything that's larger than a refrigerator, this approach blows any alternative out of the water. It's just a no-brainer.
Founded in 2019, Rosotics closed a US$750,000 funding round last November.
"We're funded to the pre-seed level," says LaRosa, "to get the process proven and validated. We've got the platform and the prototype built, and we know with great confidence what the process can produce. And now we're getting ready for the gauntlet: the establishment of an assembly line and production, with its own challenges in terms of not just making the machines work, but efficiently building them repeatedly in large volumes. We seriously value vertical integration, and having a modular platform that can mutate over time to meet different applications. So we're developing an in-house capability for assembly and production.
"We have a number of customers that have signed," he continues, "but nothing that we can announce right here. Timeframe-wise, we estimate the system will be ready for full-scale deliveries later this year."
Rosotics today opened up its manufacturing service for qualified customers, starting in October this year. With a minimum deposit of US$95,000, customers will be able to run prints in steel or aluminum up to 30 ft (9.1 m) in diameter, and weighing up to several metric tons. The company has also announced its "highly advanced production campus" will be at Falcon Field Airport in Mesa, Arizona.
Notable in their absence at this stage are any sample prints, but it seems potential customers will soon be able to see for themselves how well this tech handles the quality and precision required in aerospace. We look forward to seeing how it goes.
Source: Rosotics