3D concrete printing (3DCP) technology is already known to offer a more efficient approach to constructing buildings. A new type of 3DCP, however, is said to be even better, resulting in walls that are a claimed 72% lighter than their conventional counterparts.
At most 3DCP building sites, a robotically operated extruder nozzle moves in straight lines parallel to the ground, building up molds for walls one horizontal layer at a time. Once the hollow centers of those molds have been filled with rebar and more concrete, the walls are complete.
According to Dr. Mania Aghaei Meibodi and colleagues at the University of Michigan's DART Laboratory (Digital Architecture Research Technologies), such setups use more concrete than is necessary, plus they limit the architectural features of buildings to fairly simple shapes. That's where the university's Shell Wall system is intended to come in.
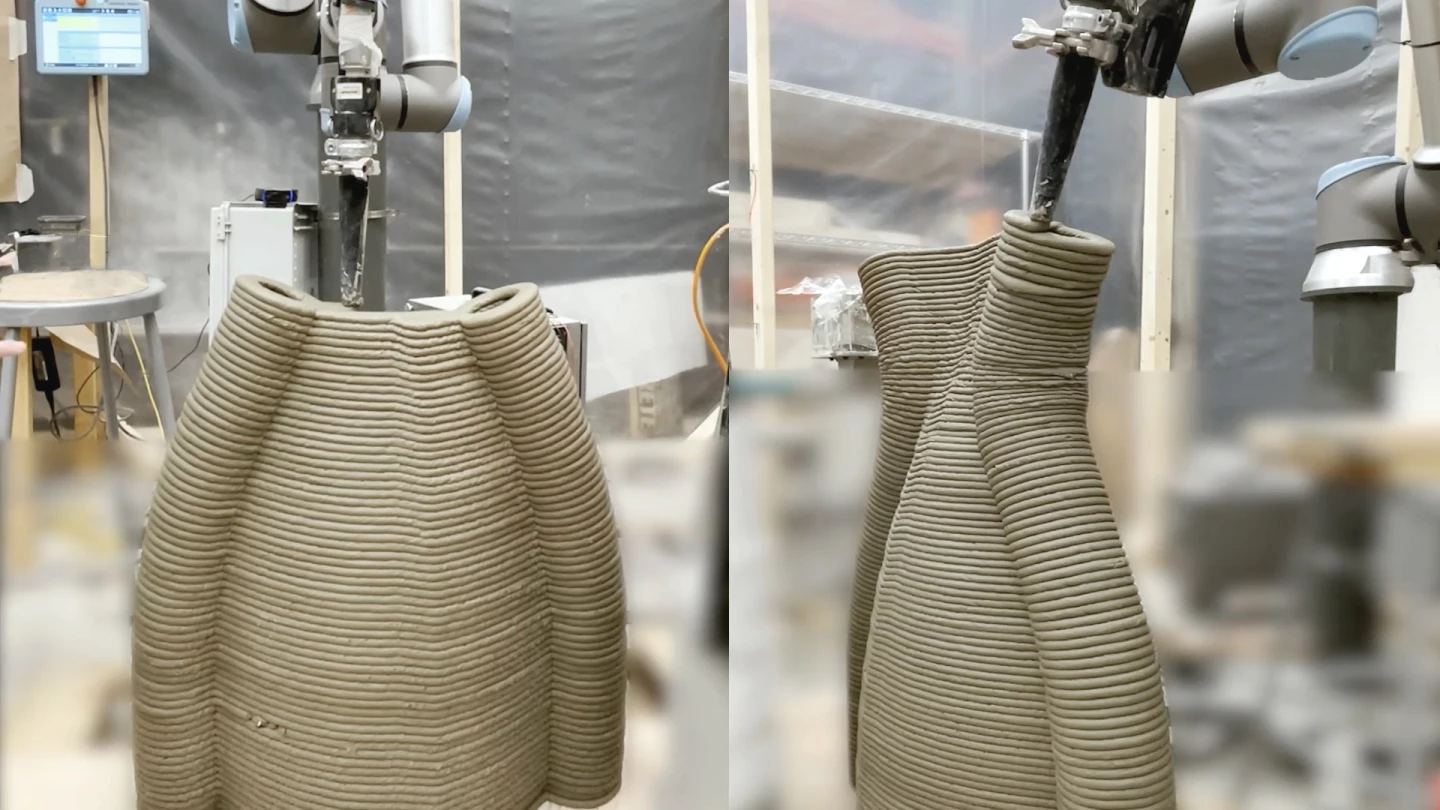
It begins with the creation of a computer model of the structure, which is based on the most efficient distribution of material needed to provide the required strength in each part of the building. In other words, no materials are included where they aren't necessary.
Guided by that model, the print nozzle then builds up layered wall elements consisting of curved vertical structural ribs with thinner curved membranes spanning the spaces between them. The layers of concrete are deposited in a non-planar fashion, meaning that they don't necessarily run parallel to the ground. And as each element is built up, vertical sections of rebar are inserted inside the hollow ribs, while thermal insulation is placed inside the hollow membranes.
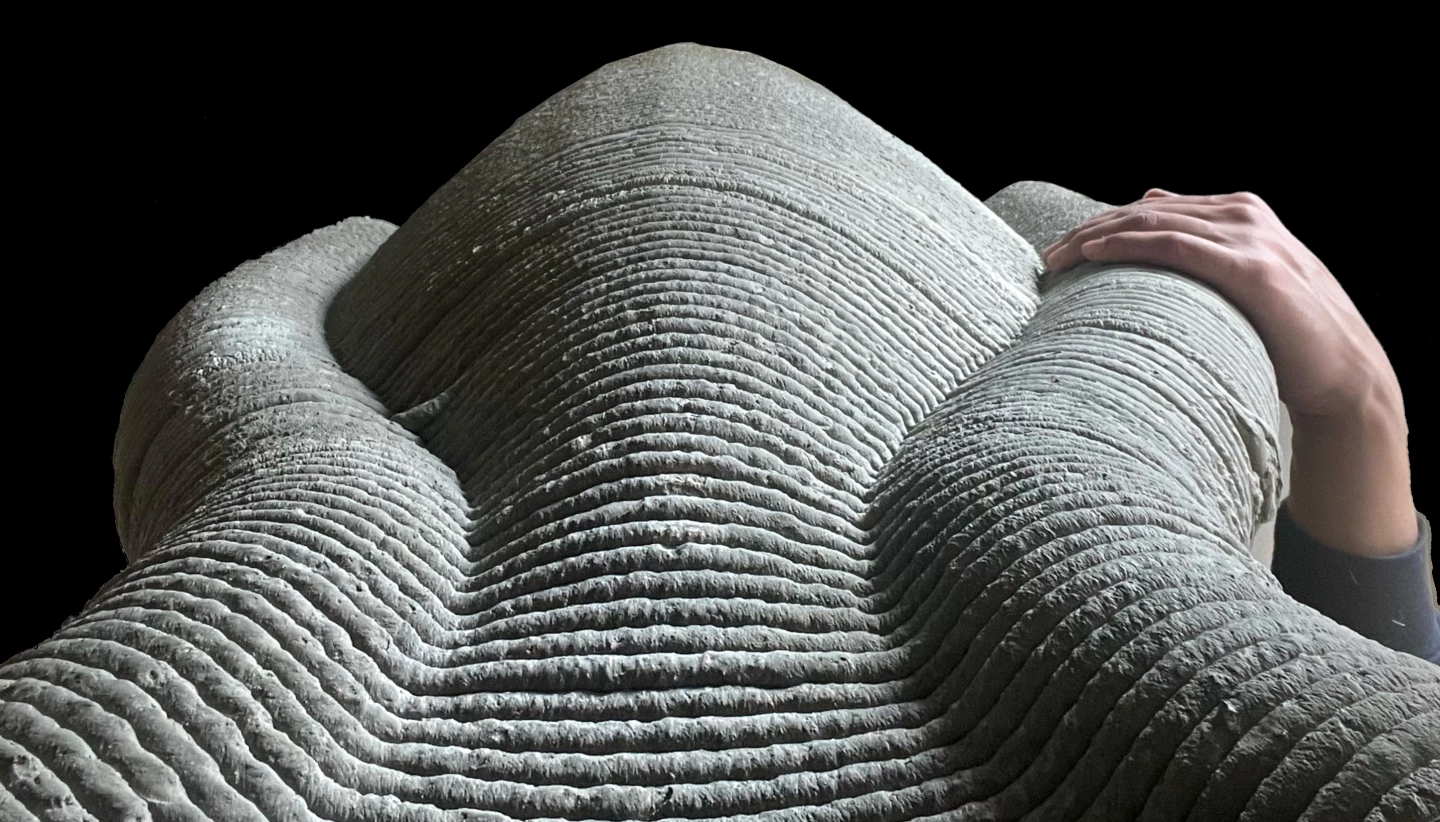
Small-scale tests indicated that as compared to same-size traditional walls built out of solid concrete, Shell Wall elements offer a 72% reduction in weight while providing the same structural strength. Full-scale tests of the technology at actual construction sites are now being planned.
You can see some of the models being printed, in the video below.
Source: University of Michigan