After spending 18 months building an entirely new form of flight control software, California's Jetpack Aviation has completed flight testing on its first prototype of the Speeder, a jet turbine-powered flying motorcycle. Top speeds on the final version will be rather epic.
When we last caught up with David Mayman, inventor, madman and one of the world's very few expert jetpack pilots, he was starting work on a new personal flight device very different to anything else on the market. The Speeder would be a very small VTOL aircraft, powered by the same extremely powerful miniature jet turbines Mayman has been flying his jetpacks around on. In this case, it would carry much higher loads, including up to two people, at higher speeds, and it'd also be much quicker and easier to deploy than a jetpack – you'd just hop on and fly.
Crucially, it would also be electronically self-stabilized, just like an electric VTOL. This sounds simple and routine, but it's not; electric motors deliver torque nearly instantly – that's why multicopter drones and eVTOLs can vary thrust across multiple props so quickly and balance themselves in the air.
Jet turbines are much slower to ramp thrust up and down; Mayman currently controls his jetpacks very manually, literally tilting the turbines with his arms and staying "ahead of the jets" on the throttle to keep himself aloft and in control.
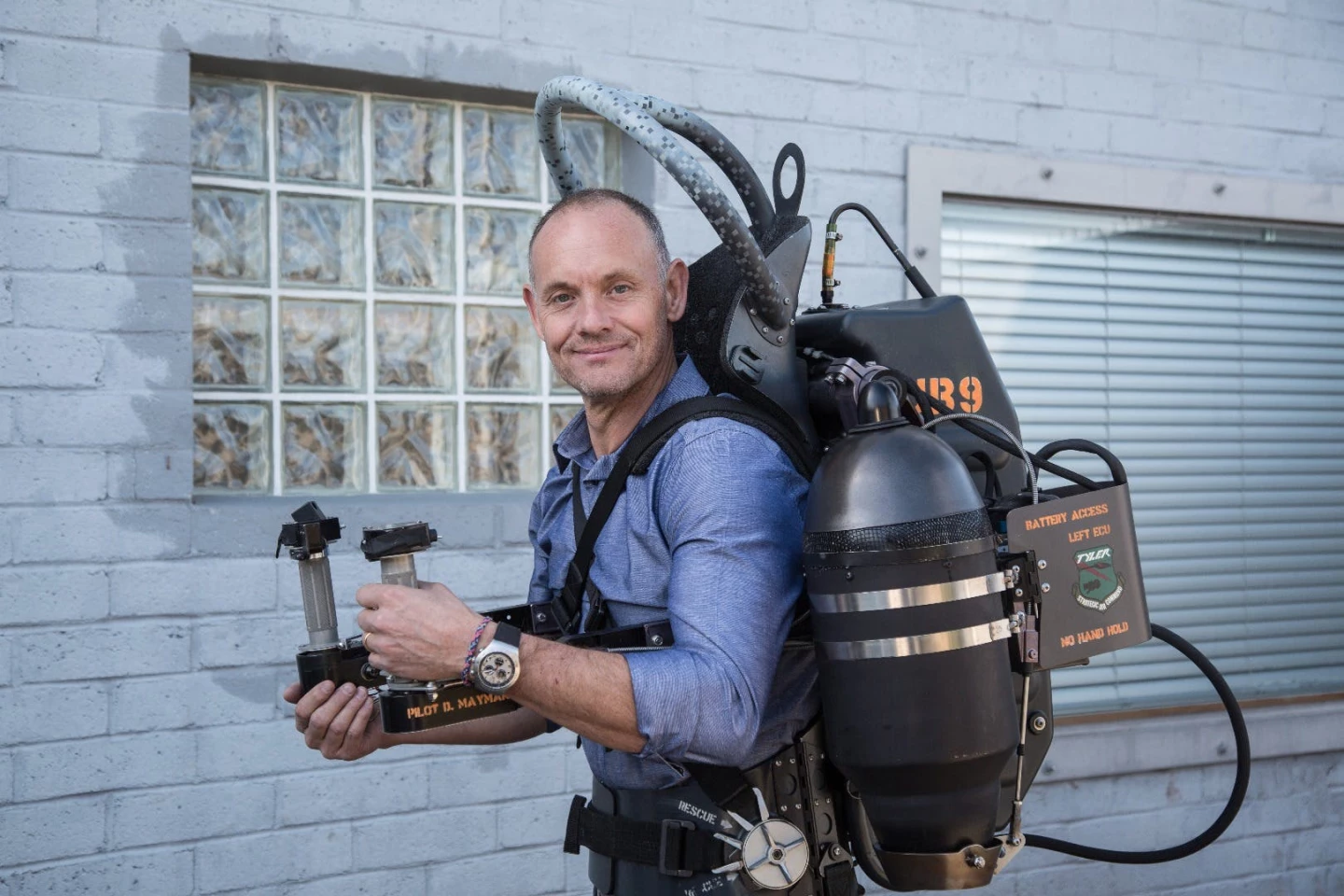
So to build a flying motorcycle that's as stable, safe and simple to fly as a drone (while flying much faster and farther, with more cargo), the Jetpack Aviation team had to go back to first principles and code a new type of flight control software that doesn't rely on rapidly varying thrust to balance and control itself.
"We had to start from scratch," Mayman tells us over a video call from his family home in France. "We have a great flight systems engineer, but he had to go back to physics modelling. And we had some different thrust configurations we wanted to try, so we had to create flight control software that could be totally flexible. Our first prototype, P1, is this big aluminum chassis, way larger than it needs to be, so we can move the engines around, try out different placements. If it was electric, you could go to a code library for a bunch of that. We had to write every line of code in the flight controller."
Instead of thrust differential, JPA uses what it calls jetovators – servo controlled nozzles that can quickly vector the thrust from each jet in 360 degrees to make lightning-quick balance corrections and execute maneuvers. And with the new flight control software, Mayman says it's working like a charm.
"It's pretty surprising how stable and resilient it is when we move engines around, shift the center of mass, or just the weight changes as the fuel load goes down," he says. "We've put dummy loads on it, it handles them very well, it just automatically counteracts that sort of thing. We've been test-flying it in 30-knot winds. I'll send you a video clip, you can see the safety tether's not supporting it."
"Right now we've verified it can take off, climb, do turns. It can hold itself in a stable hover using LiDAR. Nice and accurate. It does slowly drift a bit at the moment, maybe a foot over five minutes, but you can give it a decent shove with a pole and it'll wobble and then come right back to where it was."
"It's frustrating," he laughs. "We have these successful tests and then we look at each other and say 'well, $500 DJI drones have been doing that for years.' But obviously they've had millions of dollars spent on R&D, and they can use differential RPM. This is a whole different ballgame."
Indeed, JPA finds itself sitting on ground-up IP for a self-balancing VTOL system that'll work with a range of propulsion systems that don't have to be electric. Anything that can be thrust-vectored, any size, any configuration. Made in America, too, a fact that won't go unnoticed by the US Military's Agility Prime project.
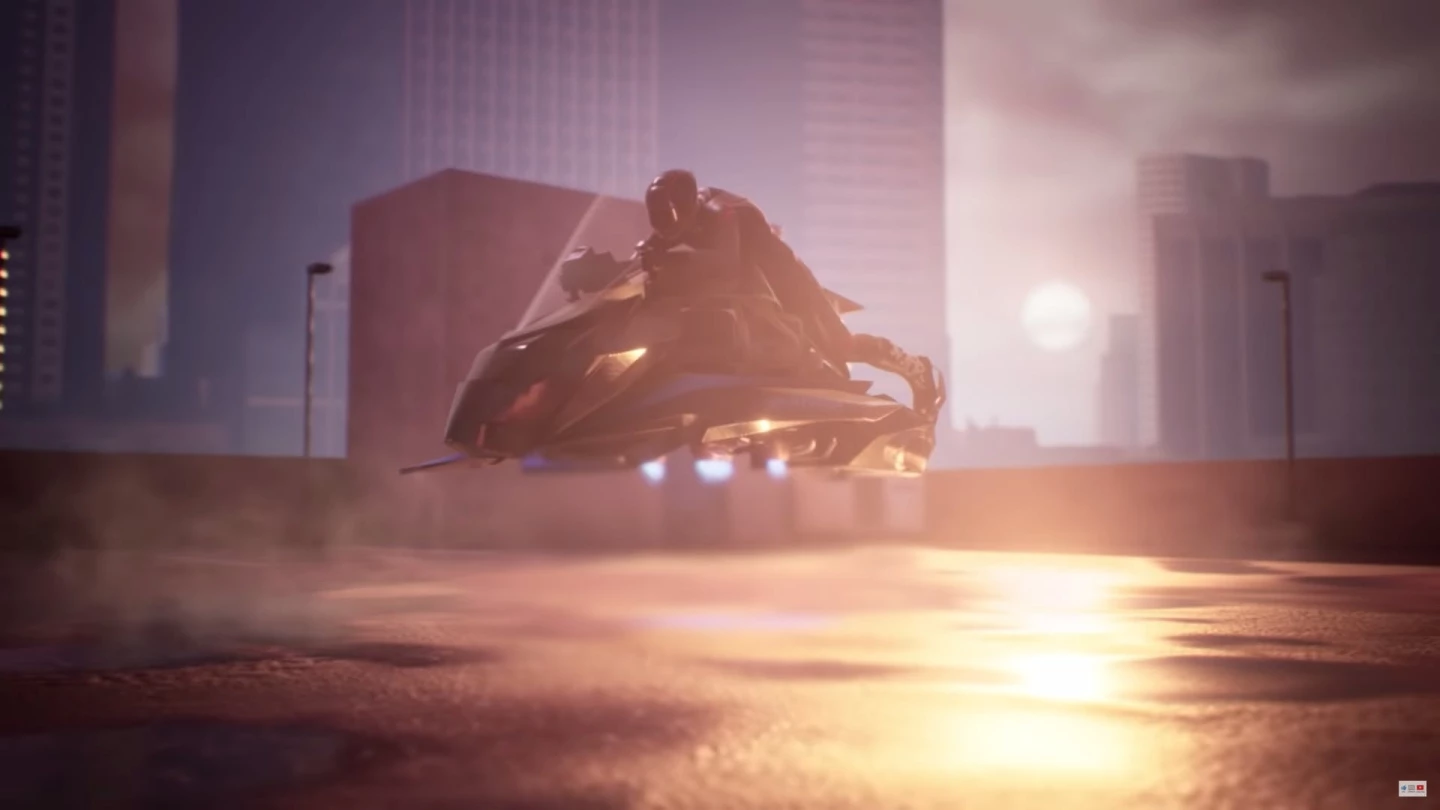
And it doesn't stop with the VTOL system. Each jet engine is also gimbaled, but Mayman says the gyroscopic forces inherent in fast-spinning turbines make those tough to move quickly enough for flight stabilization. Instead, this is to allow the jets to rotate slowly backwards for high-speed forward flight – fully backwards for the rear ones, and 60 degrees for the front ones. "That's just an airframe thing," says Mayman. "If you tilted the front jets fully backward on our current design, you'd basically torch your airframe."
This gives the Speeder the capability to achieve long-range, high-speed horizontal flight if the user clips detachable wings onto the sides. Like all VTOLs, it'll burn a lot of energy in a hover, so for many use cases it'll make sense to get into horizontal flight as quick as possible.
"Once we get on the wings, something like 70 percent of our lift is generated by the aerodynamic forces around the wing, rather than the vertical thrust component from the engines," says Mayman. "That's how we can go from flight times of 20 minutes to nearly an hour. The idea is to make it modular; we've got potential end users in the US Marine Corps that want to be able to fly, say, 300 miles (480 km). To do that, you'd need a large wingspan of 15-17 feet (4.5-5.18 m). And that's very possible, on that sort of wing you'd be running the rear engines at about 30 percent and the front ones at a flat idle."
The Speeder will be rack 'n' stackable, says Mayman, capable of deploying from a trailer, the back of a truck, or a launch pad. Wing options could easily be stored alongside the body, offering different sizes for different mission profiles. "Sometimes, you'll just want to fly the chassis, so it's got to be modular and field-adaptable. For really long-range work, it's possible to use a wet wing with a bladder full of additional fuel in it."
With wings attached, this flying motorcycle's top speed is pretty much determined by the shape it takes. "You're talking about engines here that regularly fly at Mach 0.8, 600-odd miles an hour," says Mayman. "So with a nice, slippery cargo version we're looking at more than 300 mph (480 km/h). Potentially well over, which is insane." Manned versions will be a fair bit slower, because the pilot will need to be able to see, and many will be open-top.
Winged flight would likely require control surfaces of some sort, all programmed into the flight control software to keep the pilot's control scheme super-simple and fly-by-wire. That's a whole new set of problems for the flight engineering team, because the software is going to need to be just as adaptable to different aerodynamic shapes as it is to different thrust and weight configurations.
As for what the final aircraft will look like, that's still up in the air, so to speak. The Speeder will not run the single, tightly bunched five-jet propulsion pod under the middle of the bike as shown in the original renders. That was handy for redundancy, says Mayman, but no good for vectoring thrust into a winged flight mode. Redundancy can be ensured by running two turbines on each corner instead. JPA will probably go with a head-first, belly-down motorcycle-style riding position, or it might go with a recumbent seat that would make something closer to a flying go-kart.
Or both; materially, it doesn't matter to Jetpack Aviation what this thing ends up looking like at this point. The company isn't just building a single product, it's building a platform that can adapt to running a range of different airframes with a range of different propulsion setups, to suit a range of different customer requirements.
A consumer version is still very much on the cards, and that's likely to be a single-seat machine running eight engines, two per gimbal for redundancy purposes. Mayman says the cost is creeping upward from the prior estimate of US$380,000 per unit, but it'll still be available in ultralight and experimental versions. The former will not require any kind of pilot's license, but will be limited in terms of speed (60 mph) and a fuel capacity (5 gallons). The latter will require a private pilot's license and will have no fuel or speed restrictions. JPA will provide specific Speeder training to whoever buys one, and the company's taking pre-orders – both for the consumer models and for industrial and government unit sales.
First, though, it'll likely debut as a special missions vehicle for the military and first responders. There may be no faster way to get a piece of cargo between two points, or get one or two people from ship to shore or shore to ship. "The Marines have asked us, could we transport something from a standing start to, say, 150 miles (240 km) downrange in 20 minutes, because that would make a material difference to the way they'd plan their warfighting environment," says Mayman. "Technically, yes we could; there's nothing they have now that could do that at four times the speed of a helicopter. The Special Forces guys have asked could we carry 2,000 pounds (over 900 kg). And the answer again is yes, the flight controller doesn't care if you're using four engines or twelve."
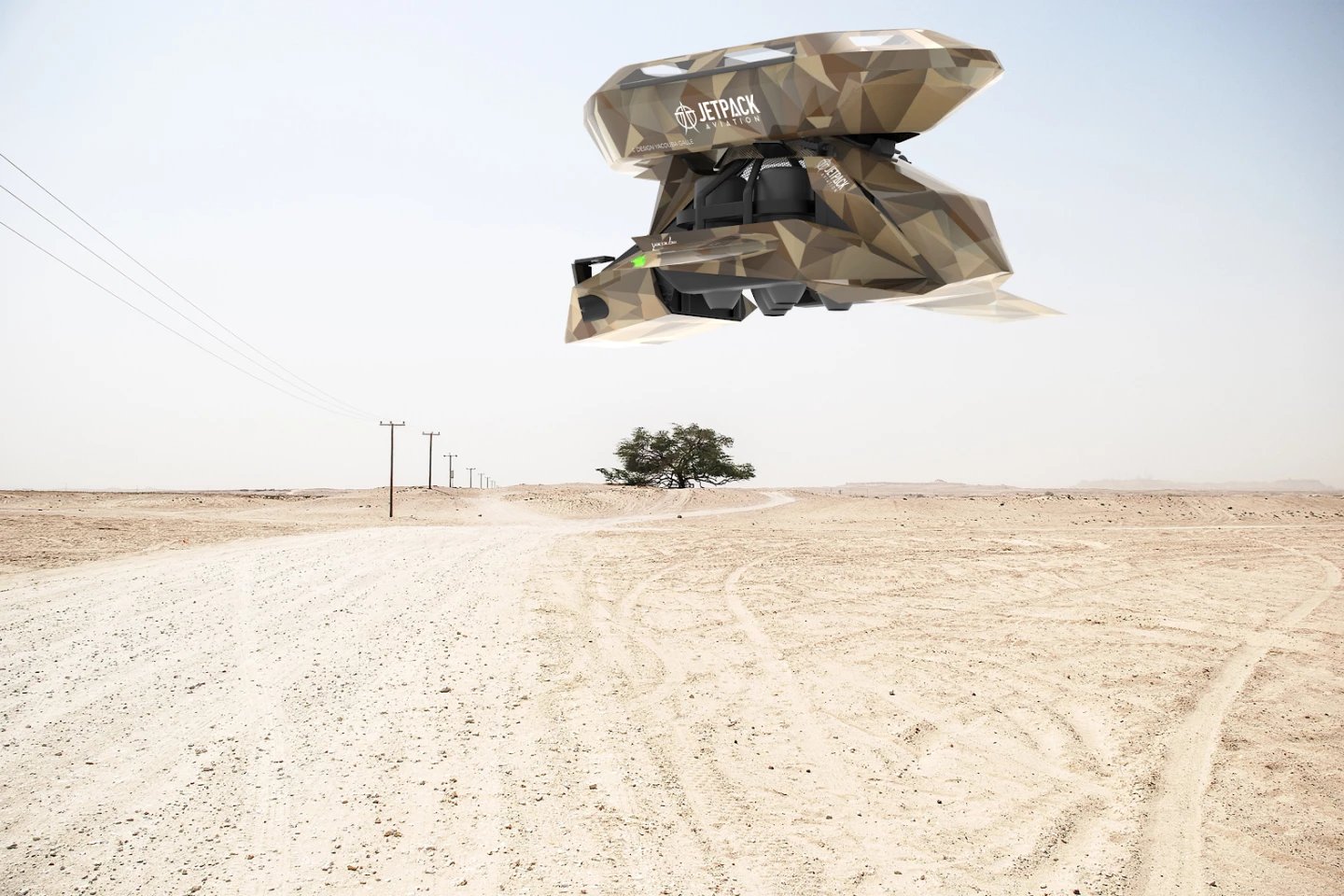
It could get a paramedic up a mountain to an injured skier faster than just about anything else, carrying a full kit of medical gear, and bring an injured person back down, either in a litter or in a second seat, just as quickly, needing only a very small flat spot to land on.
As a firefighting tool, it could deploy super quickly without a pilot, whether from a base or the back of a truck, carrying 660 lb (300 kg) of fire retardant right over a fire before it has a chance to really get raging. You'd need a massive electric VTOL to do that kind of job. "The lightning detection systems are getting so good now, that they actually know when a fire's starting," says Mayman. "Right now it's taking them too long to get an asset onto the fire, and that's where we're putting our hands up."
Work is currently underway on a P1.5 prototype that will ditch all the scaffolding and be much smaller and closer to the final passenger-carrying design, complete with a carbon fiber body. Again, it'll use four jet turbines – the final product will run eight – and JPA expects to have it in the air later this (Northern Hemisphere) summer. If all goes to plan, the P1.5 will fly off-tether. Its chief tasks are to demonstrate "increasingly rapid transitions as well as faster forward, rearward, and lateral flight."
This will be followed by a P2, which will introduce a fully-formed body, forward canards and field-removeable wings. This is the one that'll need to demonstrate high-speed forward flight, the transition in and out of a hover, and the use of any aerodynamic control surfaces in addition to the vectored thrust.
There's a chance as well to do some work on the ferocious noise that these jet turbines make. One approach, says Mayman, would be to scallop the exhaust tips like they do on commercial jet aircraft, reducing and possibly slightly phasing out some of the shear noise you get when the fast-moving jet exhaust comes up against still ambient air. Another might be to surround the turbines themselves with acoustic aerogel sound absorption.
It's unclear when the first manned Speeder flights will take place, but when it does happen, there's no doubt about who's going to be first to fly it. He may be spending a lot more time these days in CEO mode, fundraising and lining up deals, rather than cutting metal in the workshop or blasting around on one of his JB-series jetpacks, but David Mayman is a pilot first and foremost. "Oh yeah," he grins. "I'm putting myself up for the first manned test."
We wouldn't doubt that for a second.
Check out a video below.
Source: Jetpack Aviation