If you've had to move house often, or needed to live in compact spaces, you'll love this. Researchers at Carnegie Mellon University have developed a way to produce flat-pack furniture using a robotic quilting machine, which folds from lightweight cloth-covered panels into functional pieces for your home.
The team has created a chair, a side table, a lamp, and even a backpack, with plywood and acrylic panels sandwiched between a range of fabrics. The clever origami-inspired designs incorporate flexible fabric 'hinges' for easy assembly and greater strength.
According to the researchers, this work explores the possibilities we could unlock using existing CNC quilting machines to create all-new functional objects that don't require additional bits like metal hinges and the labor involved in fitting them before these are ready to use. What's also interesting is that it could inspire a whole new type of furniture that leverage this idea, and challenge creators to come up with unique geometric concepts for other products.
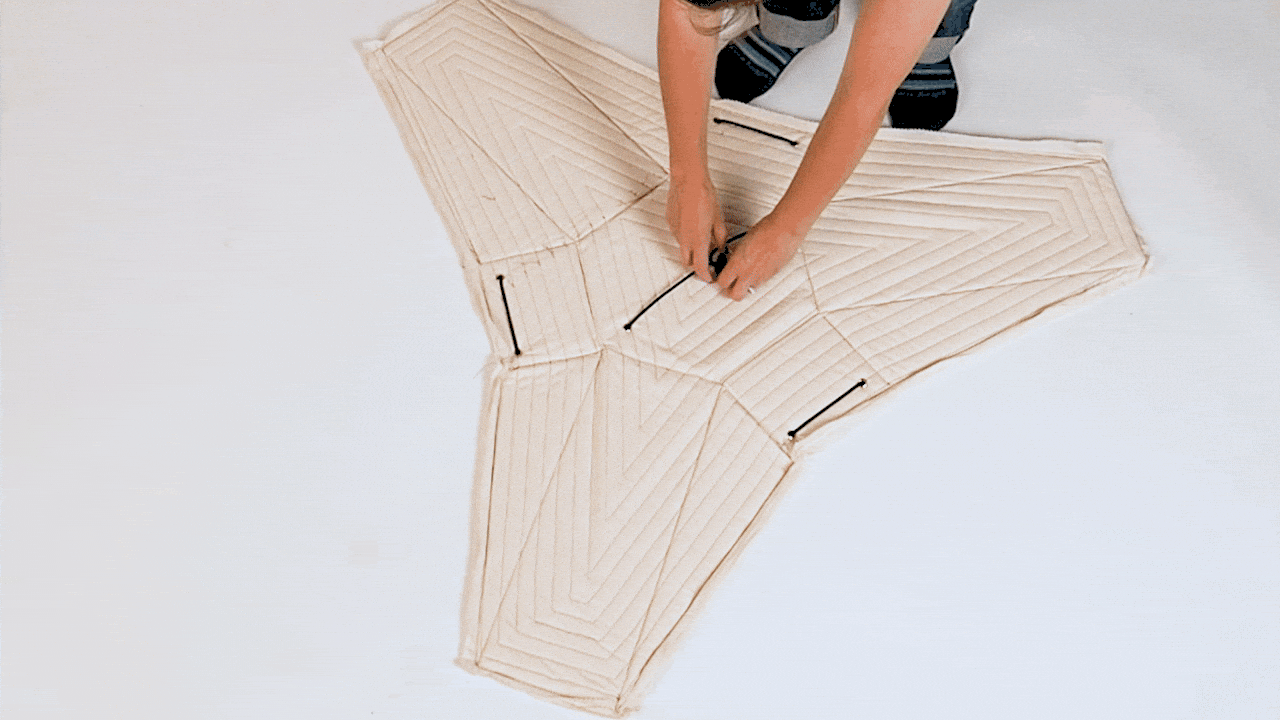
Let's take a closer look at this method. Basically, it uses what's called a CNC long-arm quilting machine – a computer-controlled sewing machine designed to work with large lengths of fabric, to join multiple layers of material together (like you'd see in a quilt or blanket). The team used a large one with a reach of 32 inches (0.81 m) and a total length of 13 feet (4 m) to work on a range of designs, and it also had the ability to follow vector paths uploaded into its companion software.
Each item's design incorporates rigid panels (made of plywood or acrylic) between layers of fabric. The sewing process secures these layers, creating soft hinges between the rigid inserts, which allow the object to deploy into 3D pieces.
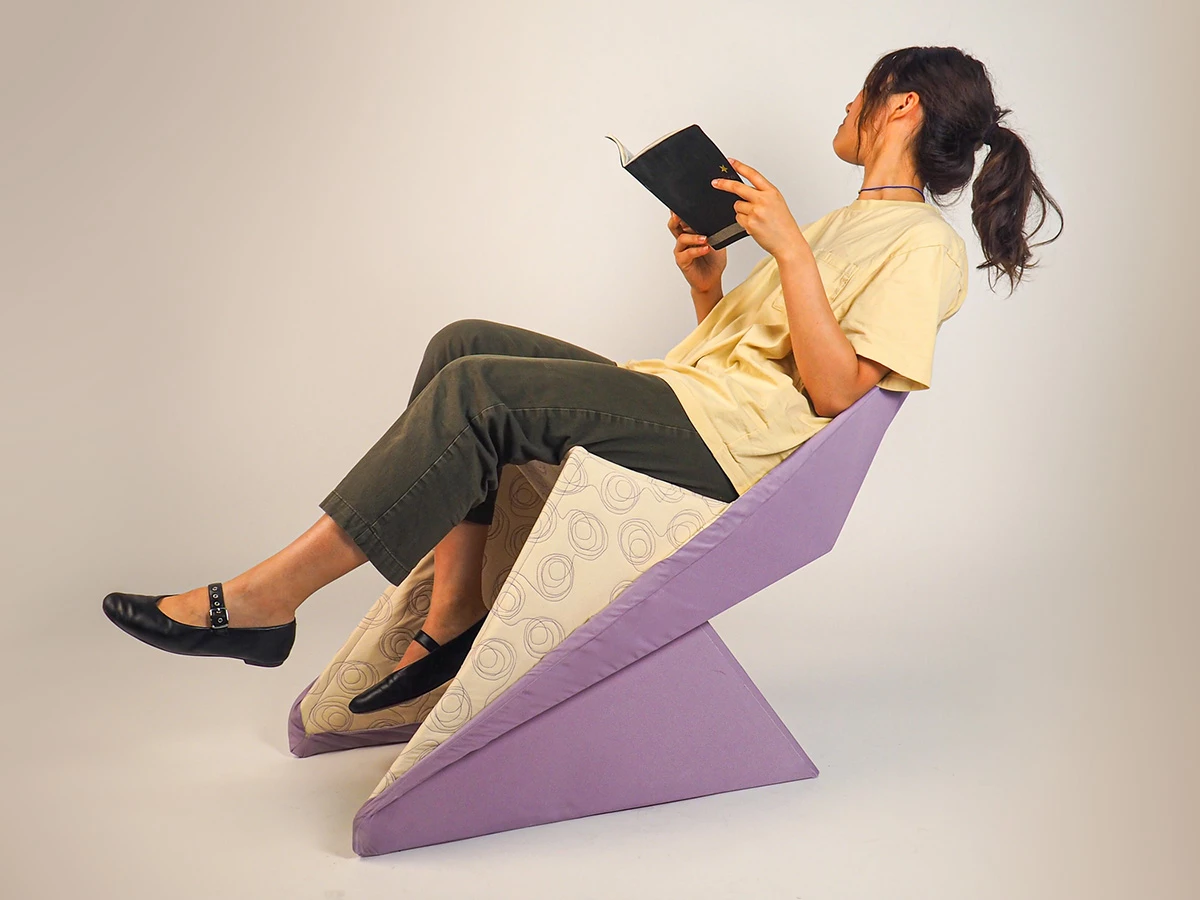
This is a flexible concept that allows for mixing and matching materials to suit the object's purpose and functions. For instance, the lamp uses sheer fabric to allow light to pass through, and the lounge chair uses thicker plywood for strength.
Additional mechanisms like tendon cords, magnets, and hook-and-loop fasteners are integrated during the sewing process to control deployment and stabilize the final form.

The designs showcased in this work each had some specific details for functionality built into them. The side table uses a tendon cord laced through struts to pull them inward and create the table's shape, which also provides stability in the deployed state. The backpack, inspired by packaging design, also uses a tendon cord system that doubles as straps for transformation. Hook-and-loop fasteners are included on the flaps to keep it closed.
The table lamp design is a modification of a 3D-printable pattern based on Lang's Elliptic Infinity lamp. It incorporates acrylic panels for visual lightness, and panels with mounted LEDs for lighting. The lounge chair is built to support the weight of an adult. So its thicker plywood inserts have neodymium magnets embedded into them to align the side panels when the chair is deployed.
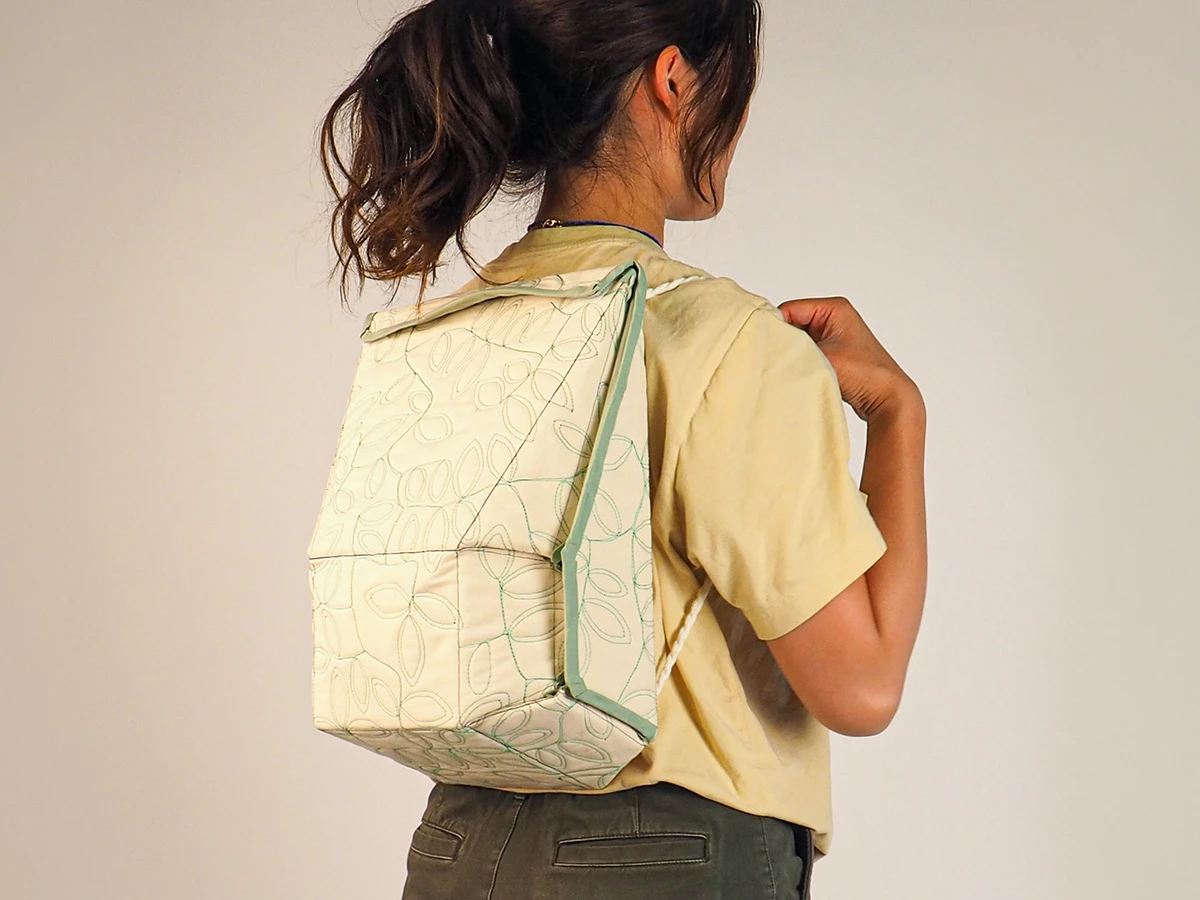
The crafty researchers had to do a whole lot more than just come up with these designs. For starters, they had to figure out ways to load and position fabric on the quilting machine so it had the right amount of tension for sewing. They also had to determine the ideal sequence of inserting panels into between the layers of fabric to prevent the materials from distorting, and learn to work with a variety of fabrics depending on the utility of each object.
That's a lot of work – but it could spell a whole new category of household products at some point in the future.
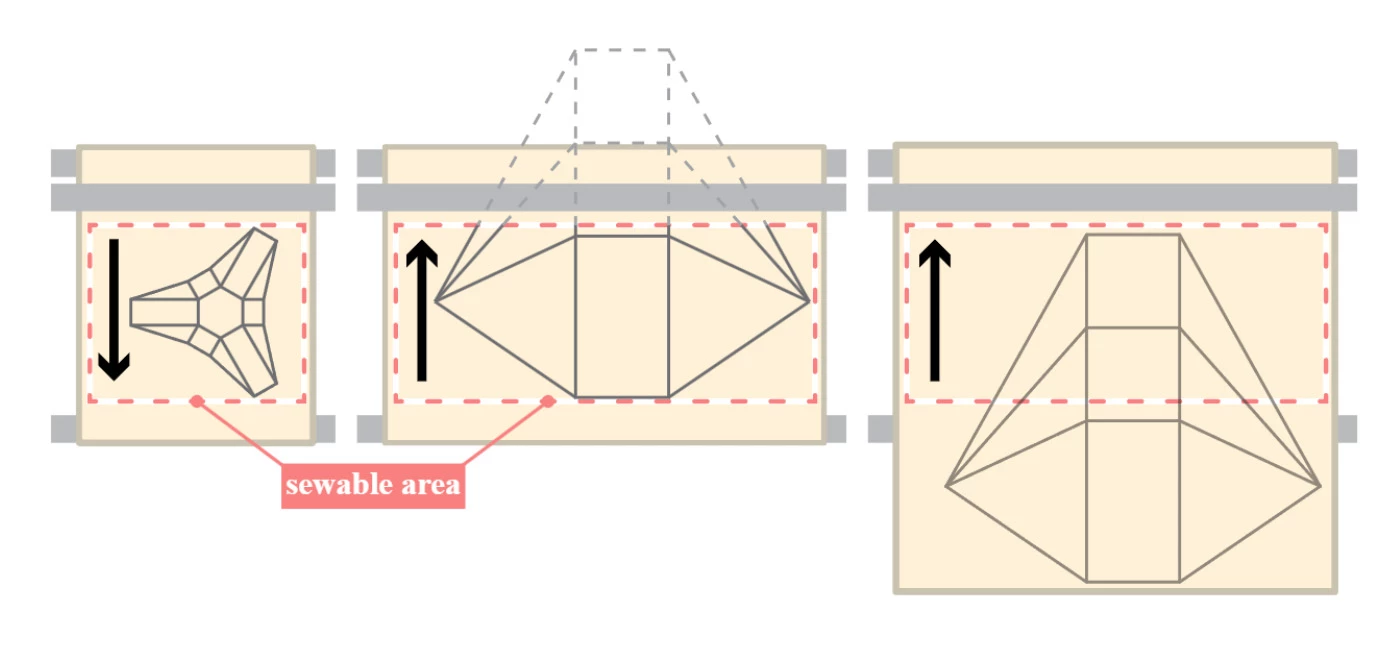
This flat-to-shape method was presented by Sapna Tayal, an undergraduate student at Carnegie Mellon's School of Design. You can see more of the work that went into it on Tayal's site – and while you're at it, dig her concept for modular long-lasting headphones.
Source: Carnegie Mellon University