Hitachi reports that the "world's first ultra-large full battery dump truck" is being put to work at an open-pit copper/gold mine in Zambia. The prototype will undergo validation testing under operating loads to verify basic performance of the vehicle itself, and the support infrastructure.
Mining is a dirty business, but we have seen a number of efforts aimed at cleaning up its act – at least as far as the heavy machinery is concerned. Previous attempts to curb emissions during mining operations have come from the likes of GM, Fortescue, Caterpillar and Anglo American.
Hitachi Construction Machinery began its project in 2021, joining forces with tech titan ABB "to explore opportunities for mine operators to target net-zero emissions from mining machine." Development of a battery electric dump truck kicked off in June of that year.
By 2023, First Quantum Minerals jumped into the partnership pool, agreeing to feasibility trials for the truck at its Kansanshi copper/gold mine in Zambia – where a number of Hitachi trolley trucks were already in operation.
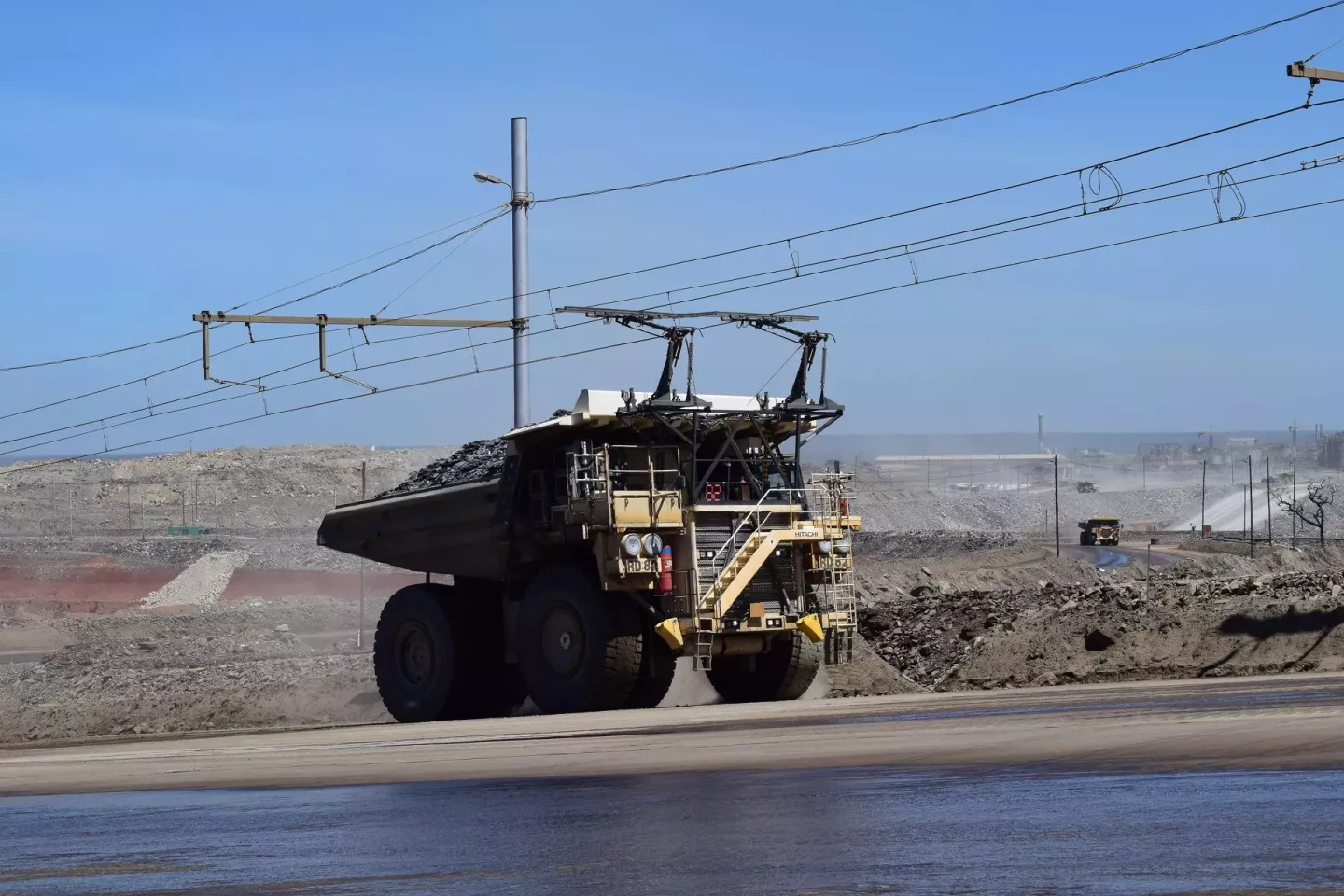
These diesel-electric vehicles trundle around the site using the internal combustion engine for power like a regular truck, but can also raise a panto to overhead cables and run on electric only. A battery electric rigid-frame version would cut diesel emissions out of the picture completely, which is particularly attractive for mining in Zambia as some 92% of the country's energy needs are met by renewables.
Spin forward to January of this year, and initial testing of the prototype was completed. The collaboration has used a Hitachi EH4000 AC-3 model as the template for the battery electric trolley test mule, which measures 47 ft in length (14 m), rolls on 29-in (74-cm) tires, is powered by a 2,500-hp Cummins engine and has a nominal payload of 243.6 tons (221 tonnes).
Now the fully kitted out prototype has arrived in Zambia, and embarked on a technology feasibility trial at the Kansanshi mine. The partnership expects the truck to be capable of continuous operation thanks to the existing network of overhead charging lines coupled with the prototype's regenerative braking system.
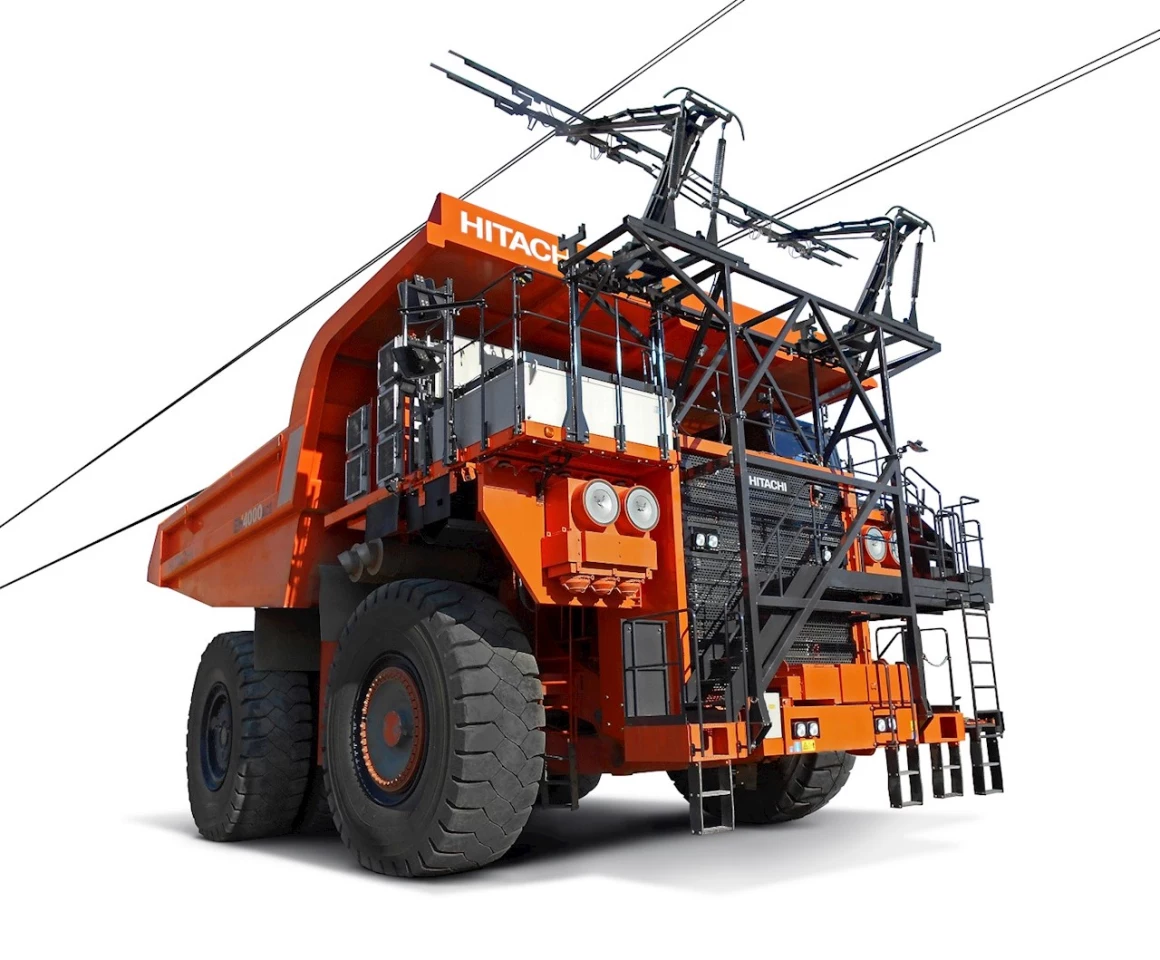
Though no capacity figures have been revealed, due to the dynamic charging setup – which should negate the need for the truck to stop and recharge – the size of the onboard battery pack is smaller than if the vehicle was to operate on battery/motor alone. This should translate to reduced production costs while also maximizing payload capacity.
"Battery zero emissions development with little to no impact on payload, production and fleet size is achievable with Trolley Assist and First Quantum have mastered this technology by working with 2,600V systems of Hitachi Construction Machinery to provide stable platforms with multiple trucks on the overhead line at the same time," said First Quantum's John Gregory. "This system is operational, practical and economical feasible solution that will reduce emissions in mining for many years to come."
The two-year-old video below demonstrates the thinking behind the project, along with a static charging option under consideration.
Source: Hitachi Construction Machinery